Slip, Trip, and Fall Prevention for Mining
- What are Slips, Trips, and Falls?
- Background & Burden
- Preventing Fall Fatalities
- Preventing Slips, Trips, and Falls from Mobile Equipment
- Eliminate slip, trip, and fall hazards in the environment
- Selection and Use of Grated Metal Walkways
- Fixed and Extension Ladder Safety
- Illumination
- Footwear and Work Boots
- Easy-to-use information
- Other resources
NIOSH researchers are actively working to help mining companies reduce slip, trip, and fall hazards in their work environments. The NIOSH Mining Program recently completed two research projects related to slips, trips, and falls:
- To identify and remediate fatal and non-fatal slip, trip, and fall incidents.
- To enhance situational awareness in underground mines through the development of novel visual interventions.
This page provides recommendations and resources for preventing slips, trips, and falls in mining.
What are Slips, Trips, and Falls?

Slip: A slip occurs when the foot unintentionally slides on a walking or working surface.
Trip: A trip occurs when the foot gets caught on an object or obstruction while walking.
Fall: Slips and trips can lead to falls, as can other hazards in the mining environment. Falls can occur to the same level or to a lower level.
Background & Burden
Slip, trip, and fall (STF) hazards in mining environments pose safety risks to mine workers. According to an analysis by NIOSH researchers of MSHA data, about 22% of all non-fatal injuries reported to the Mine Safety and Health Administration (MSHA) between 2014 and 2018 were associated with STF incidents. Each STF incident led to an average of 60 lost workdays.
For stone, sand, and gravel (SSG) operators, slips, trips, and falls occurred at a rate of 62 per 10,000 full-time equivalent employees per year (2008-2017) and led to approximately 23,800 total days lost per year, at an estimated cost of about $17.5 million per year (2008-2017). In addition, STF hazards identified during MSHA inspections cost the SSG mining sector approximately $3 million per year in assessed violations (2013-2017).
STF hazards can also lead to fatal incidents. Between 2006 and 2015, STF incidents accounted for 55 or approximately 11% of all surface mining fatalities.
Want more information?
- Burden associated with nonfatal slip and fall injuries in the surface stone, sand, and gravel mining industry
- Causes of Fall Fatalities at Surface Mines
Preventing Fall Fatalities
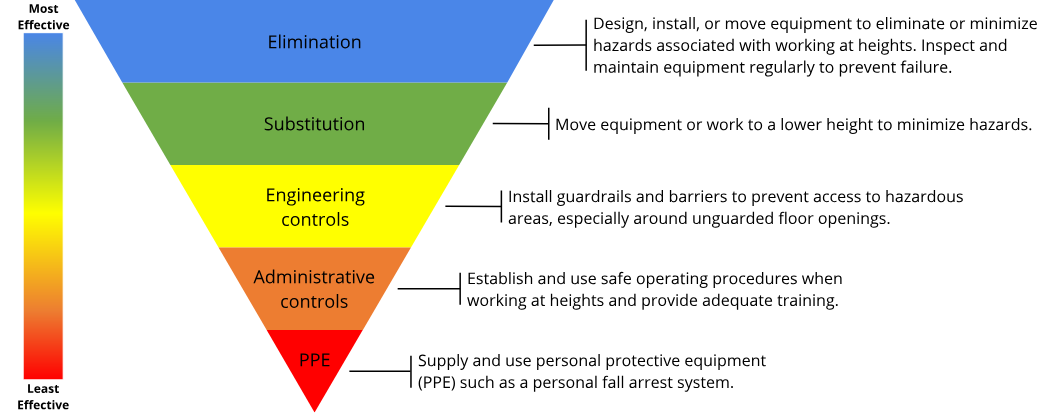
Hierarchy of hazard controls: Recommendations to prevent falls from height fatalities. (Click for larger image.)
Falls from heights are the leading contributor to fatal fall incidents. Laborers, equipment operators, mechanics/maintenance workers, and truck drivers are the most common victims. Performing maintenance and repair tasks, daily operations, and installation/construction/dismantling are common activities at the time of a fatality. Some specific recommendations to help prevent fall from height fatalities, based on NIOSH's version of the hierarchy of controls, is shown in the “Hierarchy of hazard controls” figure.
Over 50% of MSHA-issued imminent danger orders at metal/nonmetal mines were associated with fall risk (2010-2017). Of the imminent danger orders related to fall risk, 84% involved the workers not using fall protection, fall protection not being provided, or the improper use of fall protection. Tasks commonly performed by miners when the imminent danger order was issued were standing on mobile equipment, performing maintenance and repairs on plant equipment, or working near highwalls. Using fall protection would have prevented the imminent danger order from being issued and allowed the task to be completed safely.
Want more information?
- Analysis of Fall-Related Imminent Danger Orders in the Metal/Nonmetal Mining Sector
- Contributing Factors to Slip, Trip, and Fall Fatalities at Surface Coal and Metal/Nonmetal Mines
- Causes of Fall Fatalities at Surface Mines
- Falls Can Kill!
- Fall protection: As Easy as A-B-C
- Fall protection: As Simple as 1-2-3
Preventing Slips, Trips, and Falls from Mobile Equipment
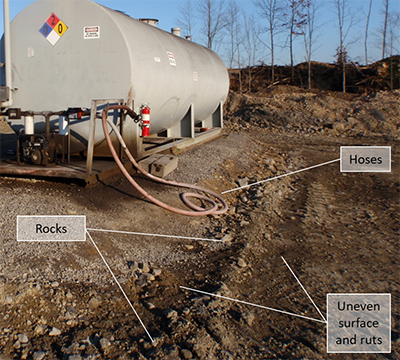
Fueling station hazards: Uneven ground, ruts, rocks, and hoses around a fueling station that pose a slip, trip, and fall hazard. (Click for larger image.)
Large trucks (haul trucks), loaders, and dozers were the three pieces of mobile equipment most commonly associated with STF incidents. Nearly 50% of the injuries occurred during ingress and egress and about 25% occurred during maintenance.
For haul trucks, 26% of non-fatal injuries related to haul trucks were due to STF incidents, with nearly 50% occurring during egress, about 25% during ingress, and 16% during maintenance and repair. STFs from haul trucks were most often due to the foot slipping.
For wheeled front-end loaders, nearly 65% of injuries occurred during egress and 25% occurred during ingress. Slips were the most common cause of the incident for front-end loaders, which can be caused by contaminants like water, ice or snow, and mud on the equipment. Stepping on rocks, stepping down onto uneven ground such as ruts and holes, and objects on the ground like hoses and pipes also contribute to ingress and egress injuries (some examples are shown in the “Fueling Station Hazards” figure). Equipment failure and unexpected movement also contributed to the wheeled front-end loader injuries.
NIOSH researchers interviewed mobile equipment operators to explore their views on mobile equipment ingress and egress system safety. Mobile equipment operators identified egress as being more dangerous than ingress, similar to findings for front-end loaders, due to limited visibility when descending. Mobile equipment operators felt equipment ladders posed a risk due to flexible rails, high lower rung heights, and inadequate traction on ladder rungs and felt stairs are safer. Mobile equipment with adequate lighting was preferred. Finally, some routine maintenance tasks can pose a hazard due to poor access and the need to carry items limiting the use of three points of contact on ladders.
Based on the above research and best practices from the industry, NIOSH has developed a list of recommendations for the design of safe mobile equipment access areas. The “Mobile equipment access area” figure shows a preview of these recommendations in an interactive format.
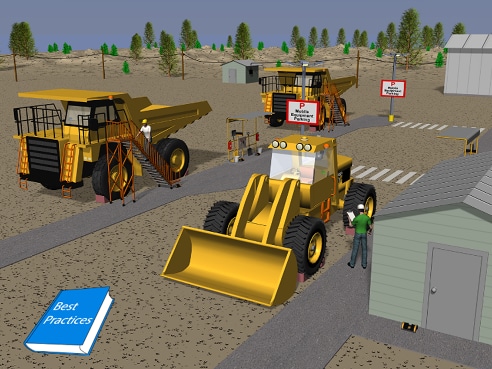
Mobile equipment access area: Best practices for the design of safe mobile equipment access areas as an interactive image.
- Provide designated parking areas free of hazardous ground conditions.
- Ensure consistent rung heights from the ground level, through the ladder, and to the cab.
- Ensure that adequate handholds are provided along the length of the ladder and into the cab.
- Construct ingress/egress platforms with stairs that allow operators to access the cab of the equipment without using ladders.
- Provide housekeeping supplies at a designated and marked location in the parking area to allow workers to remove contaminants from the equipment.
- Provide at least 20 lux of uniform illumination (measured using a lux meter) in the parking area and at least 100 lux around mobile equipment to improve detection of hazardous ground or ladder conditions.
- Regularly and thoroughly inspect and maintain ingress/egress systems on mobile equipment.
- Always maintain three points of contact when using ladders and fall protection when working at heights.
Want more information?
- Fall From Equipment Injuries in U.S. Mining: Identification of Specific Research Areas for Future Investigation
- An Analysis of Injuries to Haul Truck Operators in the U.S. Mining Industry
- An Analysis of Injuries to Front-End Loader Operators During Ingress and Egress
- Operators' Views of Mobile Equipment Ingress and Egress Safety
- Preventing Slips, Trips, and Falls from Front-End Loaders
- Designing Safe Mobile Equipment Access Areas
Eliminate slip, trip, and fall hazards in the environment
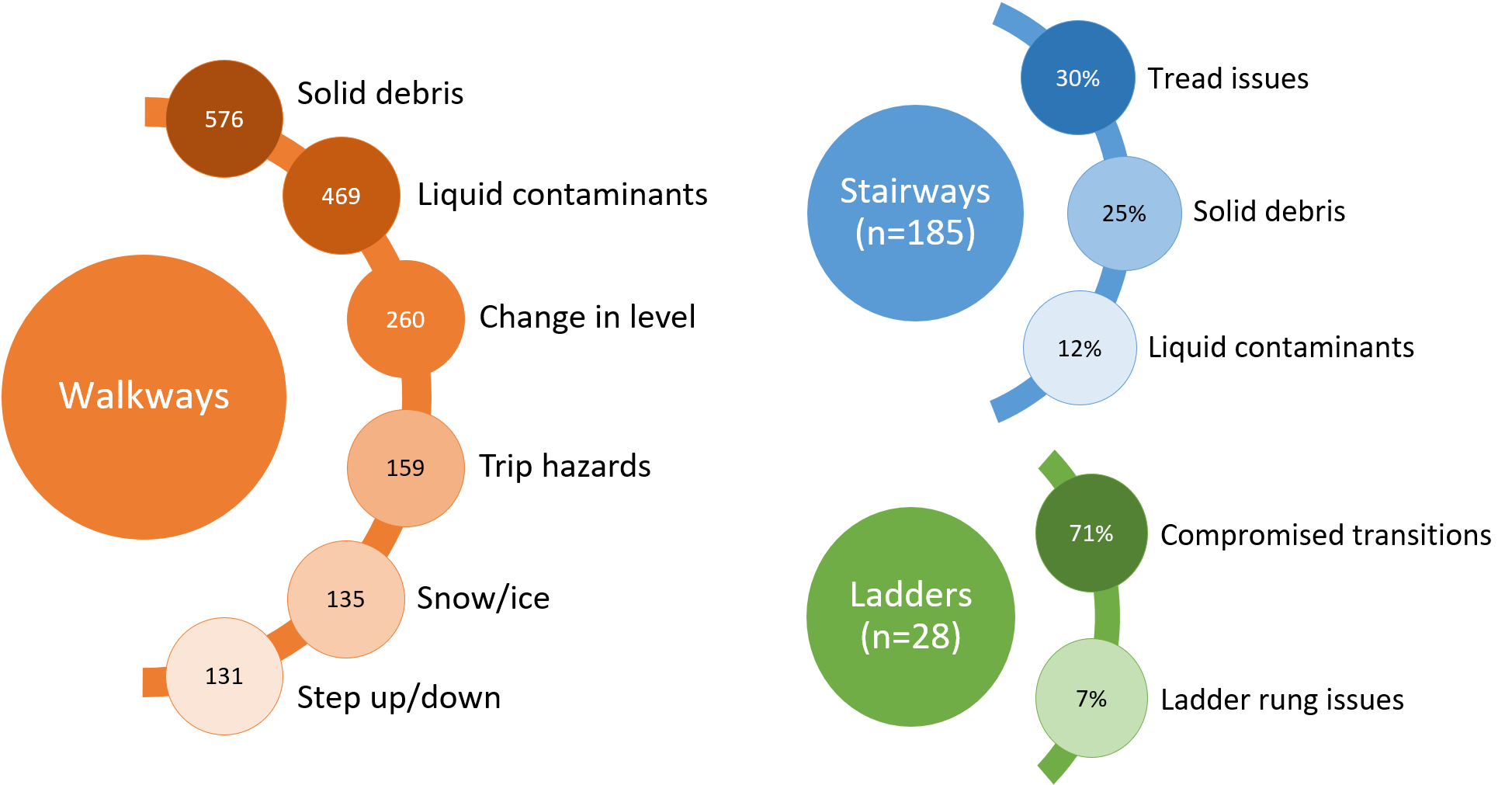
Slip, trip, and fall hazards in the environment: The figure shows the most common hazards identified during the 36-hour shadowing period. Hazards on walkways (left figure) shows the number of times specific hazards were encountered. Hazards on stairways (top right), shows the percent of stairways which had the specific hazards out of 185 stairways. Hazards on ladders (bottom right) shows the percent of ladders which had the specific hazards out of 28 ladders. (Click for larger image.)
After mobile equipment operators, laborers and mechanics were the next two occupations associated with the highest number of non-fatal STF incidents at surface stone, sand, and gravel (SSG) mines (2015-2017). Walking and running was identified as the most common activity at the time of non-fatal STF incidents at surface SSG mines (2015-2017).
NIOSH researchers shadowed laborers and mechanics to identify environmental STF hazards at surface SSG mines. Shadowing is a technique where researchers can follow miners without interfering with work while researchers take notes of hazards encountered. NIOSH researchers focused their efforts on walkways, stairs, and ladders; and looked for hazards on the surface and environmental features which could lead to STF incidents. The “Slip, trip, and fall hazards in the environment” figure shows the most commonly identified hazards during the 36-hour shadowing period.
A few proactive ways to eliminate identified STF hazards are listed below, some of which are already adopted at mines.
- Regularly grading unpaved surfaces.
- Remove large rocks and ruts from walkways and working surfaces.
- Follow basic housekeeping, such as removal of material accumulation on walkways and stairs and returning hoses and cables to their designated storage locations.
- Install and maintain designated walkways, especially along common paths of travel.
- Install and maintain drainage around wet processes to prevent accumulation of water in puddles and move water away from walkways and working surfaces to settling or catchment ponds.
- Fix or replace bent, broken, or damaged stair treads
- Provide and maintain level, flat, and stable landings at the base of all ladders
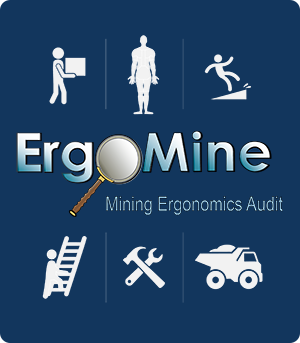
ErgoMine: A safety and ergonomics audit tool for the mining industry
Hazard recognition is an essential first step to eliminating STF hazards. However, there is no comprehensive list of STF hazards to aid hazard recognition or create workplace evaluation tools. In response, NIOSH researchers developed a taxonomy—a categorized, comprehensive list—of STF hazards on walkways, stairways, and fixed ladders at surface mining sites and also developed recommendations to fix the identified hazards. The taxonomy and recommendations were based on regulations, standards, guidelines, and best practices and are available online. The taxonomy was also used to create STF evaluation checklists which was incorporated into ErgoMine—a safety and ergonomics audit tool designed specifically for mining.
Want more information?
- Why slips, trips, and falls are still a problem: A hazard assessment at surface mines
- Overcoming common slip, trip, and fall hazards
- A taxonomy of surface mining slip, trip, and fall hazards as a guide to research and practice
Selection and Use of Grated Metal Walkways

Grated metal walkway materials tested: Diamond weave (left), showed the best performance in preventing slips when wet. The circular perforated pattern (center) and serrated rectangular bar (right) both resulted in slips starting at a 10° inclination when the surface was wet. (Click for larger image.)
Grated metal walkways are common in the mining industry, especially along conveyors and around fixed equipment. A NIOSH laboratory investigation found that slips occurred on grated metal walkways at inclinations as low as 10° when the walkways were artificially contaminated. Hence, it is importation to consider the type of grated metal walkway material used for walkways. Some recommendations based on an investigation of grated metal walkways are listed below.
- Diamond weave grating provides significantly better slip-protection compared to serrated bar and perforated gratings when dry or wet.
- Avoid inclinations over 10° when slippery conditions may exist.
Want more information?
Fixed and Extension Ladder Safety
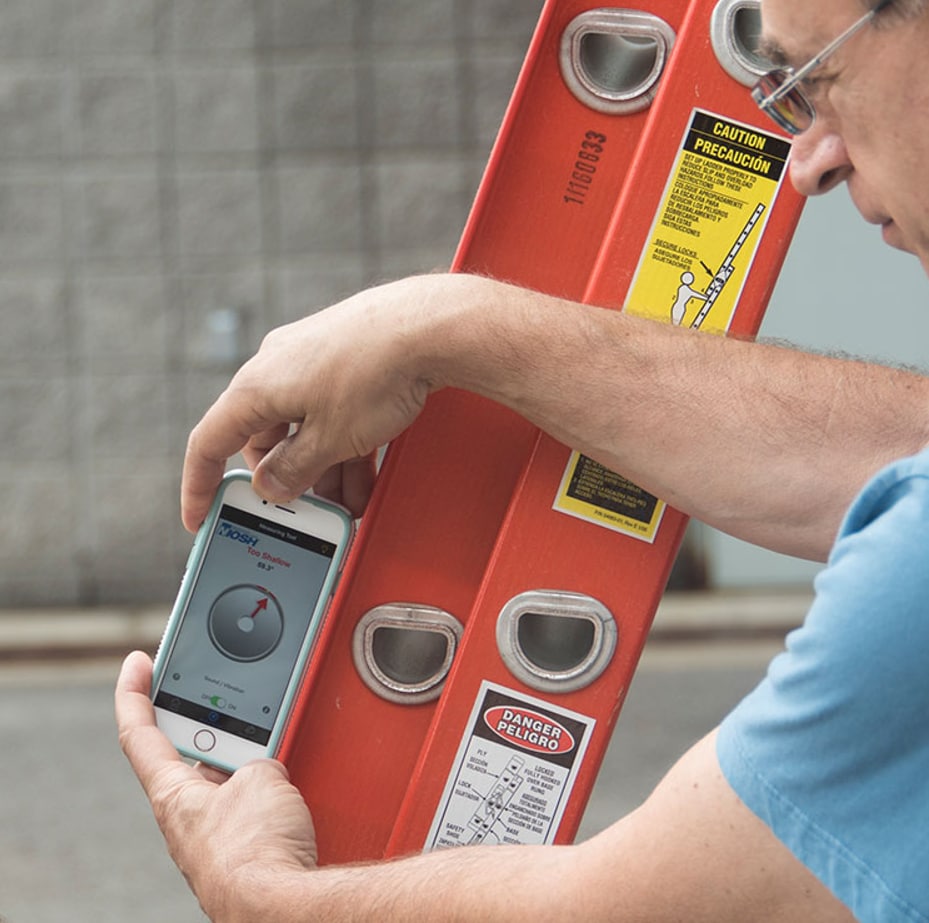
Using the Ladder Safety App: The Ladder Safety App being used to position an extension ladder.
Extension ladders should be positioned at such an angle that the horizontal distance from the top support to the foot of the ladder is about 1/4 the working length of the ladder (OSHA Quick Card: Portable Ladder Safety). The NIOSH Division of Safety Research identified that the main causes of falls from extension ladders were the ladder base slipping out, ladders tipping, workers slipping while on ladders or transitioning from a ladder to a surface at height, and mechanical failures. Research indicated that using a multimodal angle indicator (both visual and auditory) to help position extension ladders led to a more accurate position as compared to standing at the base of the extension ladder with toes against the rails and holding the ladder rungs with the arms outstretched horizontally. Using a multimodal indicator to help position ladders also significantly decreased ladder positioning time.
To aid with ladder positioning, the NIOSH Division of Safety Research has developed a mobile application, (Ladder Safety App), which helps identify the correct angle at which to position an extension ladder and improves extension and step ladder safety. The “Using the Ladder Safety App” image shows the app being used to position an extension ladder.
An analysis of MSHA data indicated that more than 120 mine workers are injured per year due to falls from ladders. A NIOSH review of Occupational Safety and Health Administration (OSHA) regulations and American National Standards Institute (ANSI) standards yielded a few simple steps that mine workers can take when using ladders to prevent falls. These steps are listed below and available in the Steps to Ladder Safety infographic.
- Wear safe shoes: Wear shoes that have heels with a defined front edge.
- Remove contaminants: Clean debris, mud, ice, or grease from the ladder and from gloves and shoes.
- Inspect the ladder: Check the ladder for defects such as broken, loose, or bent parts before climbing.
- Face the ladder: Face the ladder when climbing up and down.
- Climb and descend carefully: Never jump from a ladder or climb more than one rung at a time.
- Maintain three points of contact: When climbing, don’t carry anything in your hands. Use a backpack or shoulder strap for tools and personal items.
Want more information?
- Extension-ladder safety: Solutions and knowledge gaps
- Research to improve extension ladder angular positioning
- NIOSH Ladder Safety App
- Steps to Ladder Safety
Illumination
Illumination around Mobile Equipment
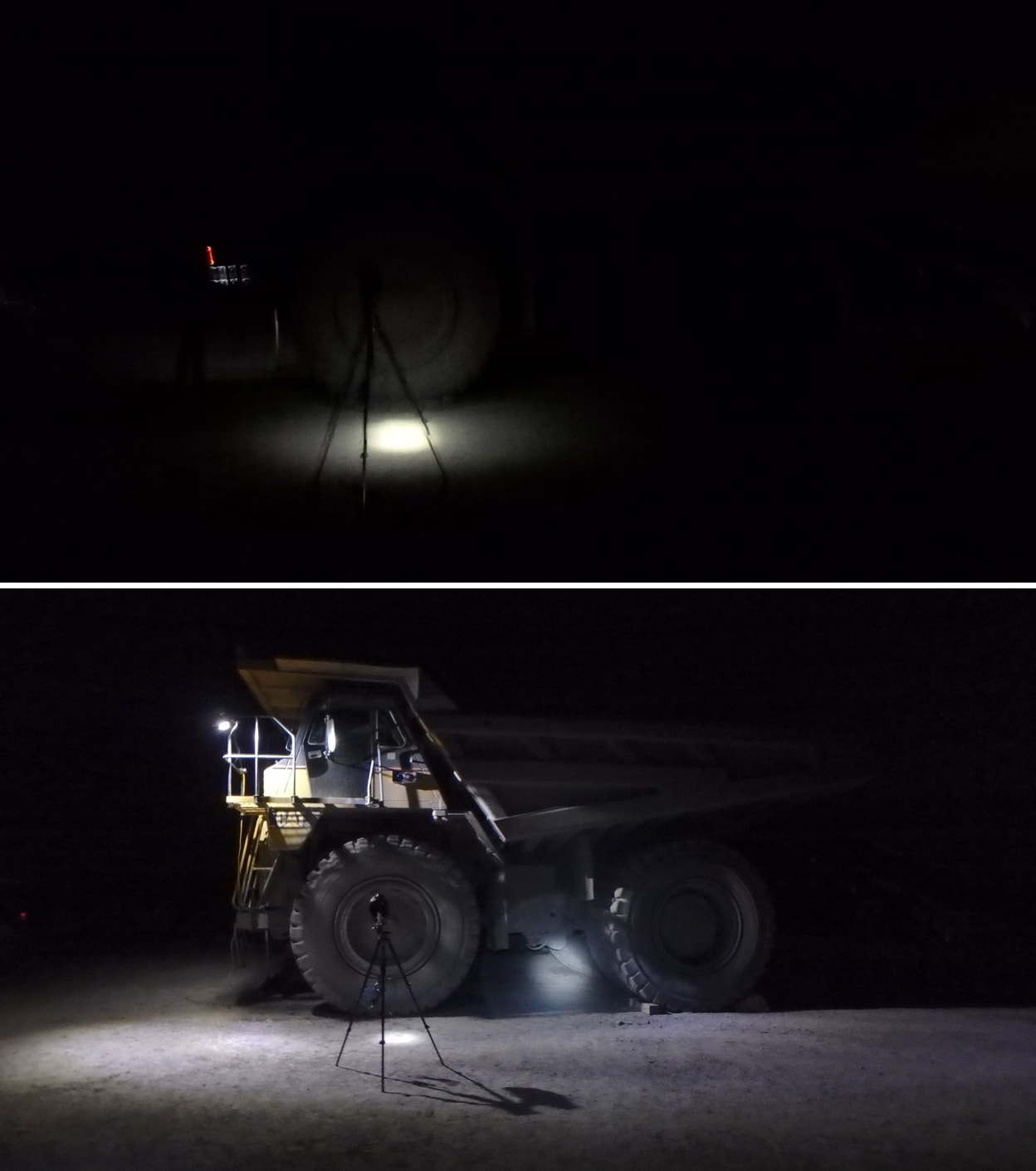
Improved illumination with area luminaires: Mobile equipment illuminated with only a headlamp (top), compared to mobile equipment illuminated with a headlamp and an equipment mounted area luminaire (bottom).
Inadequate lighting at surface mines can lead to nonfatal injuries from STF. NIOSH researchers conducted a field study to investigate lighting on haul trucks and wheel loaders with regard to glare and illuminance levels recommended by the Illuminating Engineering Society (IES). The objective was to determine whether equipment mounted light-emitting diode (LED) area luminaires could improve illumination around mobile equipment by complementing the currently used headlamp luminaire. Measured levels of illumination demonstrated that illuminance met or exceeded IES-recommended levels with the headlamp alone and with the area luminaires plus the headlamp. Although headlamps provided adequate illumination, LED area luminaires illuminated a much broader area compared to the narrow spot lighting of the headlamp (see “Improved illumination with area luminaires” figure). Hence, the use of additional equipment mounted area luminaires can increase STF hazard recognition and detection. The study illustrated how strategically placed area luminaires can offer a simple to install and use, cost-effective, and practical solution for enhancing equipment operator safety during ingress/egress and pre- and post-shift walkaround inspection activities.
Want more information?
- Lighting mobile equipment for safer surface mining operations
- Investigation of Machine-Mounted Area Lighting to Reduce Risk of Injury from Slips-Trips-Falls for Operators of Mobile Surface Equipment
Illumination and Cap Lamps for Underground Mining
Detection and avoidance of hazards is best when there’s sufficient illumination without creating glare and distractions. NIOSH has developed two LED-based luminaires or lights for underground mines that can help improve the detection of trip hazards and reduce glare when compared to incandescent cap lamps. In a study conducted at NIOSH, LED-based cap lamps enabled detection of hazards on average 0.96 seconds or 13.6% faster than incandescent cap lamps. In addition, NIOSH has developed a Saturn LED area light that can improve trip hazard detection and reduce glare around roof bolters as compared to existing bolter lighting.
Want more information?
- Visual Performance for Trip Hazard Detection When Using Incandescent and LED Miner Cap Lamps
- The Saturn LED Area Light Provides Improved Illumination for Greater Roof Bolter Safety
- LED Lighting for Improving Trip Object Detection for a walk-thru roof bolter
- LED Area Lighting to Reduce Glare for Roof Bolter Operators
Footwear and Work Boots
Boot wear and replacement

Boot wear: An example of wear on the outsole of work boots for mobile equipment operators as compared to plant operators after 0, 9, and 18 months of wear. Note the additional wear on the plant operator's boots at 9 and 18 months. (Click for larger image.)
NIOSH researchers investigated how quickly the sole of footwear wears out when worn by miners and if worn boots pose a safety risk. Preliminary findings from this work indicate that boots worn by maintenance workers, utility workers, and plant operators wear out faster as compared to other occupations (an example is shown in the "Boot wear" figure). The main reason why miners felt their boots were not usable anymore was because they were "no longer waterproof," primarily due to separation of the outer sole from the upper part of the boots and was not related to wear on the sole.
Use of metatarsal boots
NIOSH researchers also conducted a laboratory study to identify if using boots with metatarsal guards affects gait and increases the risk of slips, trips, and falls. The figure "Metatarsal boots tested" show the four styles of boots tested, hiker and wader style each with and without metatarsal guards. Analysis of walking on a level surface and when ascending or descending an inclined walkway indicated no difference in gait between safety toe boots with metatarsal guards as compared to safety toe boots without metatarsal guards of similar construction and style. This indicates that there is no change in risk when using safety toe boots with metatarsal guards as compared to safety toe boots without metatarsal guards of similar construction and style. However, gait parameters (lower extremity range of motion) were affected by the boot style (i.e., hiker versus wader), possibly due to the increased shaft height or increased stiffness of the shaft in wader style boots.
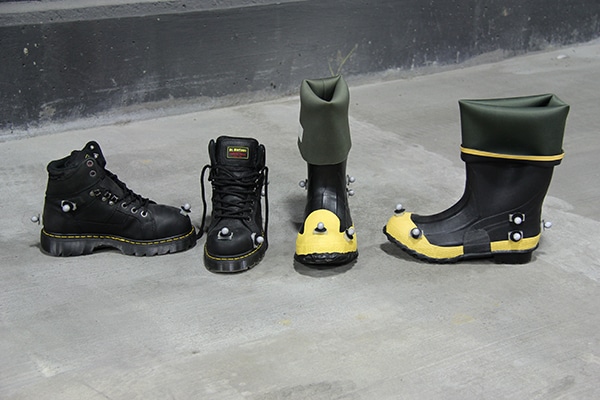
Metatarsal boots tested: Left to right - Hiker style safety toe boots without metatarsal guard, hiker style safety toe boots with metatarsal guard, wader style safety toe boots with metatarsal guard, wader style safety toe boots without metatarsal guard. Small silver dots on boots are markers used to track gait. (Click for larger image.)
In addition, preliminary analysis indicates no differences in toe clearances when ascending stairs using hiker-style safety toe boots with metatarsal guards as compared to hiker-style safety toe boots without metatarsal guards of similar construction and style. This indicates the risk of trips, due to getting the toe caught, does not increase when wearing boots with metatarsal guards when ascending stairs. These findings may only apply to the boots tested and may not be generalizable to boots of different construction and styles.
Want more information?
- When Work Boots Wear Out
- Inspect Your Boots for Signs of Wear
- Metatarsal Boot Safety When Ascending Stairs
- Effects of Metatarsal Work Boots on Gait during Level and Inclined Walking
Easy-to-use information
- ErgoMine: A mobile app to help you conduct an ergonomic audit at the mine site.
- Infographics: Single-page fliers/posters to provide guidance to mining companies and mine workers to prevent slips, trips, and falls.
- Interactive web graphic: An interactive website to provide guidance to mining companies on the design of safe mobile equipment access areas.
- Ladder Safety App: A mobile app that helps you correctly position an extension ladder and provides information on extension ladder safety.
- Simple solutions booklet: Examples of how to reduce exposure to risk factors for slips, trips, and falls and musculoskeletal disorders.
- Stickers: A graphic reminder of important topics to help prevent slips, trips, and falls. Stickers available include Report, Repair, and Revisit (RRR) the Hazard, ABC and 123 of Fall Protection, and Clean the Debris. E-mail mining@cdc.gov to request the stickers.
Other resources
- NIOSH Falls in the Workplace: Research carried out by NIOSH Division of Safety Research related to aerial lifts, ladders, and falls from heights.
- The Campaign to Prevent Falls in Construction: Training and other resources that can be adapted for use in mining.
- Age Awareness Training for Miners
- Burden Associated with Nonfatal Slip and Fall Injuries in the Surface Stone, Sand, and Gravel Mining Industry
- Contributing Factors to Slip, Trip, and Fall Fatalities at Surface Coal and Metal/Nonmetal Mines
- Designing Safe Mobile Equipment Access Areas
- Don't Slip Up!
- Ergonomics: Beyond Compliance
- Infographic: Steps to Ladder Safety
- Investigation of a Slip/Fall Accident
- Reducing Low Back Pain and Disability in Mining
- Slip, Trip, and Fall Hazard Identification, Investigation, and Remediation at Surface Mining Facilities
- Steps to Ladder Safety
- Visual Performance for Trip Hazard Detection When Using Incandescent and LED Miner Cap Lamps