Mining Topic: Illumination
What is the health and safety problem?
A significant challenge in an underground mine is providing adequate lighting for mine workers to work safely. An underground mine is the most difficult environment to illuminate according to the Illuminating Engineering Society of North America (IESNA). A dynamic environment, an underground mine includes dust, confined spaces, and surfaces that reflect light poorly and offer low visual contrasts. Lighting is critical to mine workers since they depend heavily on visual cues to see fall of ground, pinning and striking hazards, and slipping and tripping hazards. Consequently, illumination greatly affects mine workers’ ability to perform their jobs safely.
Age is a significant factor affecting one’s visual abilities. The physiology of the human eye is such that visual performance degrades as a person ages. These physiological changes include reduced pupil size and cloudier lenses, which results in less light reaching the retina. As an example, there is 40% less light reaching the retina of a 45-year-old person compared to a 24-year-old person. Also, there is a reduction in the number of rod photoreceptors that play a dominant role in vision as light levels decrease. Thus, it can become more difficult for older mine workers to see various hazards, and they can be more sensitive to glare which can cause eye discomfort or reduce their ability to see various hazards.
What is the extent of the problem?
Inadequate lighting can be a contributing factor for some of the accidents that occur in mining. These include slip and fall hazards which can be more difficult to detect in low light. Mine Safety and Health Administration (MSHA) accident data for 2016-2021 indicates that slip or fall of a person is the second leading accident class of nonfatal lost-time injuries at underground mining work locations. For this period, 5,532 injuries occurred resulting in about 25% of all nonfatal lost-time injuries. Inadequate light can also prevent a mine worker from seeing an approaching machinery hazards and could result in pinning and striking accidents.
Age is also an important factor that needs to be considered in illuminating the underground mine environment, given that the median age of the mining workforce is about 43 years. As the mining workforce ages, the need for effective underground lighting becomes even more pressing.
How is the NIOSH Mining Program addressing this problem?
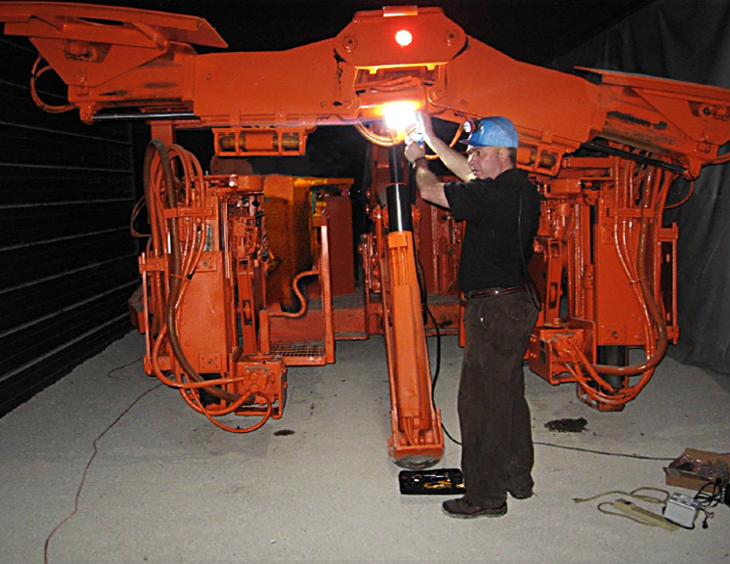
Figure 1. Machine-mounted luminaire
NIOSH Mining is conducting mine illumination research to improve mine worker safety by improving a mine worker’s ability to see mine hazards. Thus far, 20 papers have been published, covering diverse topics such as cap lamps, machine-mounted lighting, glare, lighting maintenance, postural control and stability, roof bolter lighting (Figure 1), and light-emitting diode (LED) technology issues. NIOSH researchers have also developed an LED cap lamp, the Saturn and Jupiter LED area lighting, and a machine Visual Warning System that addresses struck-by and pinning accidents.
LED cap lamps were developed in two research phases. The phase I cap lamp focused on enhancing the color of light. The phase II cap lamp extended the gains from the phase I cap lamp by changing the lighting distribution such that floor and moving machinery hazards received more light to make them more visible. The phase II LED cap lamp is also approved by the Mine Safety and Health Administration (MSHA).
One method to address the issue of less light at the retina of an older person is to increase illumination; however, this approach also increases glare and decreases the availability of battery power. NIOSH’s approach to address age-related issues is to manipulate the visible light color spectrum of a cap lamp. At low-light (mesopic) ambient conditions, such as those found in underground mining, an increased short-wavelength spectral content can improve visual performance because the eye is more sensitive to that wavelength of visible light. Therefore, NIOSH developed an LED cap lamp that enhanced these short wavelengths of light.
Historically, lighting a roof bolter has been challenging given the machine’s size, limited space for mounting lighting, low contrast levels, and excessive glare due to the workers’ close proximity to the machine lighting. Proper lighting plays a critical role in enabling miners to detect hazards when operating a roof bolter, one of the most dangerous mining machines to operate. To address these challenges, NIOSH researchers developed the Saturn LED area light with the main objectives of reducing glare and increasing floor illumination to improve the ability of miners to see floor tripping hazards. A secondary objective was to reduce the size of the lighting to give more flexibility for mounting the lighting on roof bolters—thus, new mounting locations could potentially provide better illumination of hazards.
What are the significant findings?
A comparative study was conducted using the phase I prototype LED cap lamp with short wavelength enhancements, a commercial LED, and an incandescent cap lamp. The results indicated significant improvements for the oldest age group (> 50 yrs old) of test participants; 23.7% faster floor hazard detection; 15% faster peripheral motion detection (essential for detecting moving machinery hazards); and 53.8% reduction in disability glare. With the enhanced LED cap lamp, there was also 65% less power usage compared to the incandescent cap lamp.
In testing, the phase II LED cap lamp enabled 94% faster trip hazard detection and 79% faster peripheral motion detection. With the phase II LED cap lamp, there was no increase in glare and up to 50% less power usage compared to commercially available LED cap lamps.
Human subject testing of the Visual Warning System, as mounted on a continuous mining machine, improved the ability to detect machine movement hazards by 71%. Significantly, this improvement translates up to 1.5 feet of machine movement.
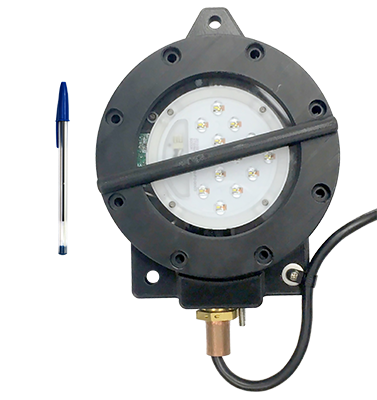
Figure 2. The Saturn LED area light developed for roof bolting machines
The roof bolter lighting study indicated significant reductions of discomfort glare and major improvements in detecting trip hazards when using the Saturn LED area light (Figure 2). Discomfort glare was improved up to three levels (from level 5 to 8). The De Boer 9-level rating scale for discomfort glare ranges between level 9 (just noticeable) and level 1 (unbearable). The mean trip hazard detection time for the oldest age group (> 50 yrs. old) was improved 58% with the Saturn LED area light.
What are the next steps?
The latest research addresses circadian disruption where shiftwork and decreased expose to natural light are factors. Underground miners have significant disruptions in the natural day/night cycle of light exposure which can disrupt their circadian rhythms. Circadian disruption can result in sleep loss, reduced alertness and an increased risk for accidents. Health problems may also result including obesity, diabetes, and cancer. NIOSH is investigating the feasibility and efficacy of human-centric lighting (HCL) interventions to reduce mineworker circadian disruption and improve well-being. HCL considers the visual and non-visual effects of light on humans, with the aim for safe and beneficial use. NIOSH researchers are investigating two lighting interventions: wearable lighted eyewear HCL worn before the shift starts and machine-mounted HCL during the shift.
Visit our Site Browser to see a listing of publications or products on lighting, improving visibility and visibility hazards. Once there, you can continue to add or remove search terms to find the information you need. Also, some Noteworthy Publications & Products are listed below.
- Crewstation Analysis Programs - An Easy to Use Personal Computer-based Lighting and Visibility Analysis Software Package for Underground Mining Equipment
- Discomfort Glare Comparison for Various LED Cap Lamps
- Do Light-Emitting Diode Cap Lamps Enable Improvements in Miner Safety?
- The Effect of Cap Lamp Lighting on Postural Control and Stability
- Evaluation of Glare for Incandescent and LED Miner Cap Lamps in Mesopic Conditions
- Evaluation of Visual Performance When Using Incandescent, Fluorescent, and LED Machine Lights In Mesopic Conditions
- Improved LED Mine Lamp Designs
- Infographic: Shine More Light on Hazards
- Mine Illumination: A Historical and Technological Perspective
- NIOSH Illumination Research Addresses Visual Performance Needs with LED Technology
- NIOSH Jupiter II Wide Area Light
- NIOSH Saturn Area Light
- The Potential Impact of Light Emitting Diode Lighting on Reducing Mining Injuries During Operation and Maintenance of Lighting Systems
- Technological Aspects of Solid-State and Incandescent Sources for Miner Cap Lamps
- Technological Aspects of Solid-State and Incandescent Sources for Miner Cap Lamps
- Technology News 556 - The NIOSH LED Cap Lamp Provides Improved Illumination for Greater Safety in Underground Mines
- Underground Coal Mine Lighting Handbook (In Two Parts): 1. Background
- Underground Coal Mine Lighting Handbook (In Two Parts): 2. Application
- Underground Coal, Metal, and Nonmetal Mine Illumination Systems for Improving Miner Visual Performance
- Visual Performance for Incandescent and Solid-State Cap Lamps in an Underground Mining Environment