Worker Falls Into Mixing Tank
February 5, 2003
Nebraska FACE Investigation 02NE044
SUMMARY:
A 45-year-old mixer operator was killed when he apparently lost his balance and fell through an opening in an operating mixing machine. The victim was cleaning the inside of the mixer by spraying water from above through one of three top side openings covered by protective grates. The victim had not shut the mixer off. As he stepped onto the top of the mixer, he fell through the middle opening. A worker one floor below heard a sound, saw blood coming from the machine and immediately activated the emergency shut off switch. The victim was pronounced dead at the scene.
The Nebraska Workforce Development, Department of Labor’s Investigator concluded that to help prevent future similar occurrences, employers should:
- ensure that all employees are aware of the basic elements of the company’s Lock-out/Tag-out program.
- ensure that employees abide by written policy regarding Lock-out/Tag-out procedures when cleaning out mixers.
- conduct an evaluation of the workplace and operations in the plant to determine if there are any permit-required confined spaces that require a written program.
- develop, implement and enforce a permit required confined space entry program for employees to follow during permit required confined space entries.
- ensure that adequate training, knowledge and skills are provided to employees to safely perform duties as necessary for permit-required confined space entries.
- ensure that written procedures are in place and employees trained regarding notifying OSHA regarding fatalities/catastrophic events.
PROGRAM OBJECTIVE:
The goal of the Fatality Assessment and Control Evaluation (FACE) workplace investigation is to prevent future work-related deaths or injuries, by a study of the working environment, the worker, the task the worker was performing, the tools the worker was using, and the role of management in controlling how these factors interact.
This report is generated and distributed solely for the purpose of providing current, relevant education to employers, their employees and the community on methods to prevent occupational fatalities and injuries.
INTRODUCTION:
On August 30, 2002, at approximately 12:45 p.m., a 45-year-old water soluble mixer operator died after he fell into a mixing machine that he was cleaning. The Nebraska Department of Labor was notified of the fatality the same day by the Occupational Safety and Health Administration (OSHA). The Nebraska FACE Investigator met with the investigating OSHA Compliance Officers (COSHAs) and company officials on September 3, 2002 at the mishap location.
The victim’s employer manufactures feed products for feed manufacturers, animal health distributors and large livestock producers (SIC Code 2048). The company has been in business since 1972 and at this location since 1998. At the time of the mishap the company employed 60 employees at the incident location, including the victim. The company did have a written safety program which contained all the required basic program elements. All training given to employees is documented and those documents were provided for the investigation. The employer had no previous history of fatalities at this location.
INVESTIGATION:
Victim: The victim was a 45-year-old male. He had been employed by this company for one year as a “Water Soluble Mixer Operator”. His normal shift start time was 7 a.m., normally working 8 hours per day with some occasional overtime. He worked 5 days per week, Monday through Friday.
Training: The company had a “Company Health and Safety Manual” with which all employees are trained upon initial employment. Training was conducted in English which the victim spoke very well. Spanish was also spoken by the victim in the workplace.
Established written procedures require mixer operators to shut down and lock out their mixer prior to cleaning. Depending on the substance being mixed, cleaning may be accomplished either by spraying the internal surface and impeller with water or by using a broom. At times it is also necessary to “jog” the impeller to ensure all materials were completely washed out and the surfaces clean.
Lock-out/Tag-out Program: There was a written Lock-out/Tag-out (LOTO) program. The victim had been trained using this program. Each piece of equipment, including the incident mixer, has specific written LOTO procedures. There are lock stations located throughout the plant facility including one for the incident mixer. The victim had been physically trained using the locks to lock out the incident mixer and this training was documented.
Confined Space Entry Program: Physical entry into the mixers are required occasionally. These mixers should have been classified as a Permit Required Confined Space, but none were marked as such. A generic written program did exist in the company’s Safety and Health Manual, but specific program elements were not addressed.
Equipment: The incident mixer (Mixer #6) is 4 years old. It was purchased new and installed in it’s current location on the third floor in 1998. The basic function of the mixer is to mix the water soluble ingredients used in the company’s products. The mixing tank is 5 feet deep and 20 feet long. It has an impeller that runs the length of the tank. It is centered inside the tank and the blades extend to each side in order to ensure materials are mixed thoroughly. (See pictures 4 & 5)
The tank is set against a wall on the far side, while a metal platform built against the mixer on the near side allows personnel access. This is gained by walking through a 16 inch opening between the platform’s right support leg and a wall, then proceeding up 7 expanded metal steps on the mixer’s right side to a working platform. This platform is 59 inches high with safety rails on two sides and a ¼” safety chain on the “load” side. It is 78 inches square. (See picture 1)
On the far side of the platform there is a 6 inch “step down” to the mixer top. On top of the mixer are three square grates, each with an external measurements of 27 inches square, and internal measurements of 23 1/8 inches square. The grates consist of 12 tubular steel rods embedded in bar steel, spaced equally along the length of the opening. Each end bar is laid over a piece of steel welded inside the opening to prevent the grates from falling inside. (See pictures 3 & 4)
The controls for the mixer are located on the left side outside edge of the upper safety railing, directly in line with the three mixer openings. The control box has a red EMERGENCY STOP button on both the left and right side. In between is a green START button and a three position function (hand/off/auto) switch. Depressing either EMERGENCY STOP button on the control box would automatically stop the machine (See picture 2). There is also an EMERGENCY STOP button located directly below on the second floor where the final mixed product emerges.
ANALYSIS/SYNOPSIS:
On the morning of the incident the victim started his shift at 7:00 a.m. At approximately 12:30 p.m. he had finished mixing the day’s assigned batches. The only task left for that day was to clean the mixer, a process that normally took 15-20 minutes. He removed a water hose that was located inside the room, turned on the water, and climbed on top of the mixer to wash it out. The mixer was not shut off nor locked out. This practice of not utilizing proper lock-out/tag-out procedures was common amongst the employees required to clean and/or enter the mixers.
It is believed that the victim removed the center grate to allow easier cleaning. The victim either stepped backward onto the lip of the opening and fell inside or reached inside to spray and was pulled into the opening.
A worker directly below on the 2nd floor heard a voice that sounded like it said “oh”, then heard a bang and saw blood running from the bottom of the machine. He hit the emergency shut off button on his level and summoned help. When company employees arrived they found the center grate ajar, and the other two in place. During the investigation all support bars for the grates were physically checked and all appeared to be secure. Attempts were made to dislodge the grates by simulating an employee stepping on them, etc. but they would not move out of position.
The water hose did not show any physical evidence of being drawn into the mixer. (See picture 6)
There were no witnesses to this incident. It can only be assumed that the victim removed the center grate to gain easier access to perform his cleaning task. Somehow the victim either fell into or possibly reached into the mixer while the impeller was rotating and was pulled in.
CAUSE OF DEATH:
According to the death certificate, the cause of death was: Blunt trauma to head, chest, abdomen and extremities.
RECOMMENDATIONS/DISCUSSION:
Recommendation #1: The employer should ensure that all employees are aware of the basic elements of the company’s Lock-out/Tag-out program.
Discussion: Adequate training in the recognition of hazardous energy sources, along with the methods and means to isolate them must be provided to employees who are authorized to perform lock-out/tag-out tasks throughout the facility. Although all employees were aware of the company’s safety and health program, not all employees had received training to their level of involvement in the Lock-out/Tag-out program. 29 CFR 1910.147(c)(7)(i)
Recommendation #2: The employer should ensure that employees abide by written policy regarding Lock-out/Tag-out procedures when cleaning out mixers.
Discussion: Although locks and training were provided, neither the victim nor the employee working directly underneath ensured the mixer was shut off and locked out during the cleaning operation. Regular spot inspections by management may be necessary to ensure compliance with established written procedures. 29 CFR 1910.147(c)(2)(ii)
Recommendation #3: The employer should conduct an evaluation of the workplace and operations in the plant to determine if there are any permit-required confined spaces that require a written program.
Discussion: An assessment of the facility and its operations concerning permit-required confined spaces, had not been conducted prior to the incident. Identification of such spaces will require written procedures that mandate locking out the mixers. Placards will need to be posted to those mixers and other equipment indicating such. 29 CFR 1910.146(c)(1)
Recommendation #4: The employer should develop, implement and enforce a permit required confined space entry program for employees to follow during permit required confined space entries.
Discussion: A generic basic written program did exist as part of the company’s Safety and Health Manual, but it was not specific for this location or equipment. Employees have entered mixers without the employer ensuring that all procedures set forth in the regulatory standard were followed. Since the incident the company has bolted all of the safety grates on each mixer so that operators can not remove them. A system was implemented where only authorized personnel, not the mixer operators, are able to remove the grates. 29 CFR 1910.146(c)(4)
Recommendation #5: The employer should ensure that adequate training, knowledge and skills are provided to employees to safely perform duties as necessary for permit-required confined space entries.
Discussion: Investigation revealed that employees have entered into mixer tanks but the employer did not ensure each employee was trained on the hazards inherent to the permit confined space and the means needed to eliminate any of the potential hazards. 29 CFR 1910.146(g)(1)
Recommendation #6: The employer should ensure that written procedures are in place and employees trained regarding notifying OSHA regarding fatalities/catastrophic events.
Discussion: Understandably the work area is chaotic during and immediately after a tragedy of this type occurs. A checklist to be used by management or secretarial personnel during an emergency could be developed to ensure all required reporting steps are accomplished to prevent this from happening again. Reporting a workplace related fatality ensures prompt response to the incident scene allowing investigators to more truly ascertain the cause of the incident. By doing this, employees can be removed from potential hazard(s) quicker. 29 CFR 1904.39(a)
ATTACHMENTS
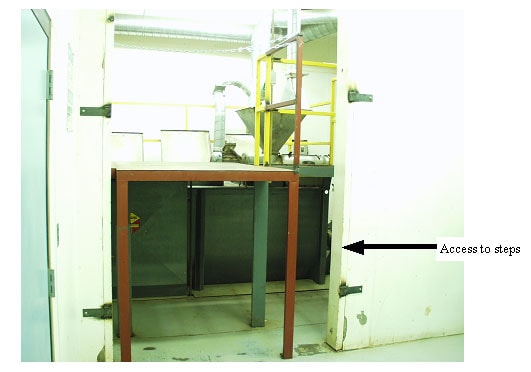
Picture #1 showing access to steps and working platform with safety chain.
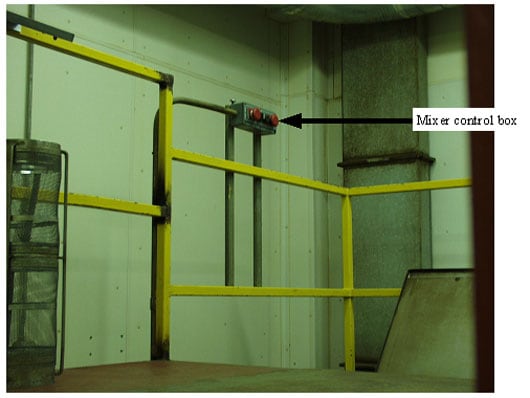
Picture #2 showing control box with emergency stop buttons on either side.
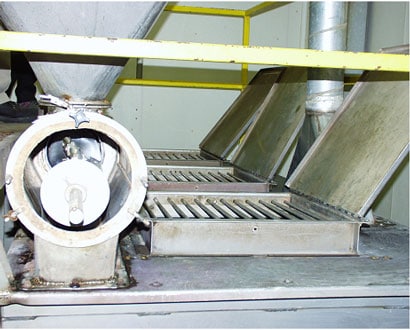
Picture #3 showing the three access openings with grates in place and lids open.
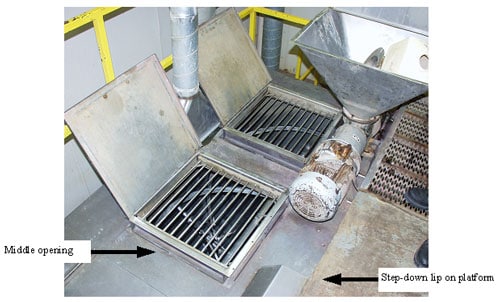
Picture #4 shows the middle grate where victim entered and the step-down between the work platform and mixer top.
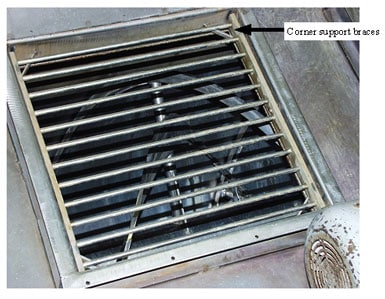
Picture #5 shows the middle grate with underlying support bars.
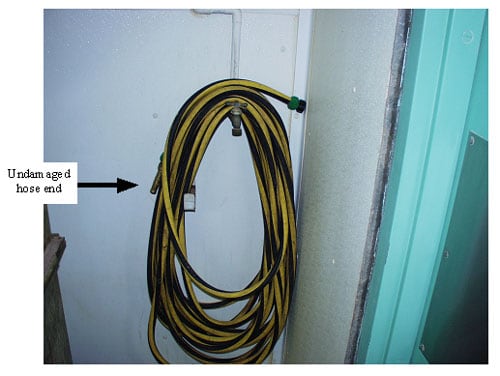
Picture #6 shows undamaged hose end.
To contact Nebraska State FACE program personnel regarding State-based FACE reports, please use information listed on the Contact Sheet on the NIOSH FACE web site Please contact In-house FACE program personnel regarding In-house FACE reports and to gain assistance when State-FACE program personnel cannot be reached.