Massachusetts Laborer Crushed in Baler at Paper Recycling Facility
Massachusetts FACE 00MA035
SUMMARY
On June 19, 2000, a 22-year-old male laborer (the victim) was fatally injured when he was crushed while inside a horizontal paper baler. The victim entered the hopper through a sliding glass door to clear a jammed paper bale. The operator of the baler left the machine’s controls to get a paper roll for the victim. The victim was crouched between the gathering ram and the jammed paper bale preparing for the paper roll when he was crushed by the gathering ram as it cycled in the forward direction. A call was placed for emergency assistance. The victim was pronounced dead at the scene and was transported to a local hospital by funeral home personnel under the direction of a medical examiner. The Massachusetts FACE Program concluded that to prevent similar occurrences in the future employers should:
- ensure that machines are operating properly to eliminate potential hazards to employees;
- develop and enforce a hazardous energy control program for all employees with procedures including specific lockout/tagout procedures for each machine;
- develop a training program that includes a protocol on how to clear jams and ensure that all workers are trained in the safe operation and the potential hazards of each machine;
- develop, implement, and enforce a comprehensive health and safety program.
INTRODUCTION
On June 19, 2000, the Massachusetts FACE Program was notified by OSHA through the 24-hour Occupational Fatality Hotline that on the same day a male laborer had been fatally injured. The victim had entered a paper baler to clear a jammed paper bale when the machine cycled and crushed him. An investigation was immediately initiated. The Massachusetts FACE Program Director traveled to the incident site where the recycling facility manager was interviewed on June 21, 2000. The state police and town police reports, death certificate, OSHA fatality/catastrophe report, photographs and interviews were obtained during the course of the investigation.
The employer, a paper baling company, was in business approximately 15 years at the time of the incident. The company employed approximately 65 people at the incident location; 22 of these employees worked the first shift of the two daily shifts with the victim. The company operated other facilities located throughout the United States and Canada. The Massachusetts facility did not have a written health and safety program or written task specific safety procedures. The company had monthly safety meetings and a safety committee, which consisted of only management and foremen. The company had a hazardous energy control program but it was not comprehensive and was written for the use of maintenance personnel while performing large repairs on the machines.
The victim, a resident alien, who immigrated from Guatemala, had been employed by the company since he was 18-years-old, approximately 4 years at the time of his death. His training was primarily on-the-job and did not include training on the hazards associated with his death. The victim was a laborer but routinely performed more skilled tasks such as operating various machines during the assigned operators’ breaks and days off.
INVESTIGATION
The facility was approximately 45,000 square feet and produced 6,500 tons of baled paper per month. The company sold the baled paper to recycling businesses that repulped and processed it into paper. Machines at this facility, all of which the victim would operate, included three balers, three large guillotine shears used to cut paper rolls in half, and one paper shredder.
The paper baler involved in the incident was an automatic two ram horizontal baler. The baler was operated by a control panel measuring approximately 1 foot wide by 3 feet long. The control panel was located on the operator platform approximately 10 feet from the floor level, accessible by a steel staircase that led up to it. Paper was fed into the baler’s feed hopper by a conveyor. The hopper side’s had been extended upward approximately 80 inches and a glass sliding door had been installed in the side of the hopper facing the operator’s platform. The glass sliding door was used as a guard to keep employees from accessing the rams during the operation and to reduce the amount of dust employees were exposed to during the compacting process. An electrical contact safety switch, interlocked with the machine’s controls, had been installed, which immediately shut down the machine if the door were opened while the baler was operating. The sliding glass door was approximately 3 feet from the control panel, which was just enough distance to make it difficult for the operator standing at the control panel to clearly see inside the bale chamber.
The baler had two hydraulic rams: a gathering ram and an extracting ram. While moving in the forward direction, the gathering ram would compact paper that entered the hopper via the conveyor. The gathering ram was approximately 96 inches long and 62 inches wide. The extracting ram’s forward motion was perpendicular to the forward motion of the gathering ram. The extracting ram pushed completed paper bales out of the bale chamber. The paper bales measured approximately 36 inches high by 40 inches wide by 48 inches long. As the extracting ram pushed the paper bales out of the bale chamber they were bound by metal wire approximately every foot by a strapper located to the right of the baler’s exit. The metal wire bound around the bale by the strapper provided the extra support needed while the bale was transported.
To start the baler the operator would insert a key into the control panel and select an operating mode, either automatic or manual by using a switch located on the control panel. In the automatic mode, the gathering ram would cycle continuously as paper entered the hopper. In the manual mode, a joystick control located on the control panel allowed the operator to control the direction and speed of the gathering ram. While the machine compacted paper, the operator typically would stand at the control panel.
On the day of the incident, the baler was compacting corrugated cardboard. The victim, a laborer, was separating the incorrect grades of paper from piles and off a conveyor when one of the three balers had a paper bale jammed inside the bale chamber. The jammed bale could not be ejected from the machine by the extracting ram due to a bulged section caused by excessive corrugated cardboard.
The operator of the baler requested the victim’s help in clearing the paper bale jam. The victim had to climb up the machine’s steel staircase onto the operator platform and enter the hopper through the glass sliding door to begin clearing the jam. On this particular machine, there was a light, small handrail and step inside the hopper to help employees climb down into the hopper. The victim first tried to clear the jam by manually removing the excess cardboard. Unsuccessful in this attempt, he grabbed a paper roll that he had carried with him to help clear the jam. A typical paper roll used to clear jams, which occurred daily, varied in length and was approximately 12 inches in diameter. He positioned the roll lengthwise with one end against the bulging section of the paper bale and the other against the end of the gathering ram and signaled to the operator to start the machine. The operator shut the glass sliding door to disengage the interlock to operate the baler. The victim stood on top of the gathering ram as the operator manually controlled the ram in the forward direction. It was intended that the paper roll compress the bulged area so the bale could pass through the exit.
This attempt did not clear the jam and the victim stayed inside the compacting chamber while the operator went to get a second paper roll. Although unwitnessed, evidence indicates that the machine was not locked out and the sliding glass door was kept in the closed position allowing the machine to cycle while the operator was away from the control panel.
Still inside the bale chamber, the victim was crouched in front of the jammed paper bale preparing for the second paper roll when the gathering ram cycled. The baler operator was at the bottom of the staircase when he heard the machine cycle. He ran back up the stairs opened the sliding door and looked down into the hopper to find the gathering ram just about fully extended. The operator then shut the glass sliding door to disengage the interlock, started the baler in manual mode, and retracted the gathering ram as he yelled for help. The operator then opened the sliding door and found the victim lying inside the compacting chamber. The victim had been crushed between the jammed paper bale and the gathering ram.
Other employees heard the operator’s yell for help and went to notify management and placed a call for emergency assistance. The company’s vice president and facility manager went to the baler involved in the incident. The vice-president and an employee climbed inside the hopper to assist the victim. The vice-president stayed with the victim until emergency assistance arrived. The town police and fire departments arrived at the incident site within minutes. The town police then called the state police department who responded with personnel from the district attorney’s office. Next, the town police informed OSHA and they also responded quickly to the facility. The victim was pronounced dead at the scene and was transported to a hospital by a local funeral home under the direction of a medical examiner.
The baler involved in the incident had several components that were not functioning properly that may have contributed to the fatal injuries. The machine was equipped with a trampler, whose main function was to help clear jams, but it was not operable. The trampler was similar to a ram and moved vertically at the edge of the hopper and bale chamber to cut away any excess paper from the bales allowing them to be extracted.
Other components that were not functioning properly included a pressure gauge, audible safety device and the lockout lever in the main power panel door. The pressure gauge was located on the control panel and used during operation in the manual mode. The operator would have known when a paper bale was fully compacted by watching this pressure gauge. To compensate for the faulty pressure gauge, a visual indicator was painted on the inside hopper wall opposite the conveyor. A second visual indicator was painted on the gathering ram. When the gathering ram moved forward the two lines would come together. When this occurred and the operator detected resistance to forward motion of the gathering ram, the operator knew the paper bale was complete and ready to be extracted.
The audible safety device would warn employees that the machine was starting by ringing a bell for a count of ten rings. A quiet low toned clunk was the only sound this audible safety device made, which was difficult to hear even while standing a short distance away. The baler’s main power switch had been replaced at an unknown date. The replacement switch did not to fit the lockout lever in the door of the power panel making the lockout lever inoperable. The machine could not be locked out directly at the replacement switch because the switch didn’t contain a location for a lock.
It was revealed during the investigation that jams were a common occurrence at the facility and when compacting corrugated cardboard, the balers at this facility would jam about twice a day. Reportedly, employees entered balers using paper roles to clear those jams. The company said they had an unwritten rule that before employees entered a bale chamber, the machine should be shut down and the key removed from the control panel. Despite the employee’s frequent entry into the chamber, the facility manager maintained that he had never witnessed an employee entering a bale chamber with out the machine being shut down and the key removed.
CAUSE OF DEATH
The medical examiner listed the cause of death as massive crushing injuries.
RECOMMENDATIONS/DISCUSSION
Recommendation #1: Employers should ensure that machines are operating properly to eliminate potential hazards to employees.
Discussion: The baler involved in this incident reportedly jammed daily, requiring employees to enter the machine where they were exposed to the point of operation. Several different components of the machine were not operating properly, which contributed to frequent jamming. The trampler device, intended by the manufacturer to clear jams, had not been working for several years. There was also a broken pressure gauge on the control panel, which, if operating properly, would have allowed the operator to know when bales were ready to be extracted from the machine. Although the company had made a “quick fix” attempt to let employees know when bales were compacted, this was not effective and the baler constantly jammed. Proper maintenance would have reduced the likelihood of jams and the need for employees to enter the baler. Employers should establish a regular maintenance schedule to assure that all baler components are operating properly. If the machine had been properly maintained, the machine might have jammed less frequently minimizing the potential hazard.
Recommendation #2: Employers should develop and enforce a hazardous energy control program for all employees including specific lockout/tagout procedures for each machine.
Discussion: In this case, the employer’s written hazardous energy control program only addressed large maintenance procedures. Operators of balers and laborers that worked in close proximity to the balers were not aware that a hazardous energy control program existed. The hazardous energy control program should address all employees including operators and laborers as well as maintenance personnel working in close proximity to the machine. A hazardous energy control program should also include specific procedures for each machine because similar machines can utilize different types of energy including electrical, hydraulic, pneumatic, and mechanical.
Control of hazardous energy (lockout/tagout) (29 CFR 1910.147) required by OSHA when any of the following conditions occur:
- The employee must either remove or bypass machine guards or other safety devices, resulting in exposure to hazards at the point of operation;
- The employee is required to place any part of his or her body in contact with the point of operation of the operational machine or piece of equipment; or
- The employee is required to place any part of his or her body into a danger zone associated with a machine operating cycle.
Prior to the victim entering the baler it should have been properly locked out; the main power switch should have been turned off and a lock applied by and controlled by the person working inside the machine. This might have minimized the possible re-starting of the machine while the employee was inside.
In addition, the hazardous energy control program should include the use of a block for the rams because they utilize hydraulic energy. A block could be developed in many ways such as two pins inserted into the sides of the hopper when the ram was retracted. When in place these pins would prohibit the gathering ram from moving in the forward direction. These same style pins should be developed and used for the extracting ram as well.
Recommendation #3: Employers should develop a training program that includes a protocol on how to clear jams and ensure that all workers are trained in the safe operation and the potential hazards of each machine.
Discussion: Baler machines can be very dangerous when the operator and workers in the immediate area are not properly trained on how to run the machine or on the potential hazards of the machine. The employer should develop safe operating procedures including a protocol for clearing jams. If employers do not provide training in safe operating procedures then, as in this case, it forces employees to develop their own way to complete tasks.
The employer did provide some on-the-job training to a few machine operators while laborers typically received no training on the machines in the facility. The victim, a laborer and a relief operator would operate the various machines during the assigned operators’ breaks and days off. Employers should provide adequate training for all employees on every machine they would enter, operate or work near. Training for all employees on balers should include but not be limited to:
- A protocol on how to clear jams including controlling hazardous energy and the use of the lockout process;
- how to properly startup and shutdown the machine and the functions of all controls;
- informing employees of all hazards associated with operating the machine;
- how to shut down the machine in an emergency including the locations of emergency stops; and
- which employees are qualified to perform certain tasks.
All training should be provided in the language that each employee clearly understands and feels the most comfortable with. If English is not the employees first language and the training is only provided in English, this may not give the employee a complete understanding of the training content.
In addition to providing training, employers should ensure that unsafe work practices are stopped immediately by performing periodic observations of employee performance. These observations are necessary so employers can be aware of how employees complete tasks and of any unsafe conditions.
Recommendation #4: Employers should develop, implement, and enforce a comprehensive health and safety program.
Discussion: Employers, with input from the employees should develop, implement, and enforce a comprehensive safety program. The comprehensive safety program should include but not be limited to who is responsible for specific safety issues, training, how employees should complete tasks, and hazard recognition. The comprehensive safety program and training must be routinely updated and include procedures for repair of machines which affect safe operations such as the trampler, pressure gauge and start-up alarm.
In this case, the company did not have a written comprehensive safety program. A comprehensive safety program would have clearly stated who was the person responsible for employee safety at this facility and that this person’s responsibility included performing regular inspections of how employees complete all required tasks. If the company had a comprehensive health and safety program the employees may have been able to identify safety hazards such as entering a bale chamber without the machine in the lockout stage. In addition, the employees would have known that they could report unsafe conditions and concerns and who to report them to.
REFERENCES
Code of Federal Regulations, Labor 29 Parts 1910.147 Lockout/tagout.
American National Standards Institute, American National Standard for Refuse Collection, Processing, and Disposal – Baling Equipment – Safety Requirements, ANSI Z245.5-1990, New York.
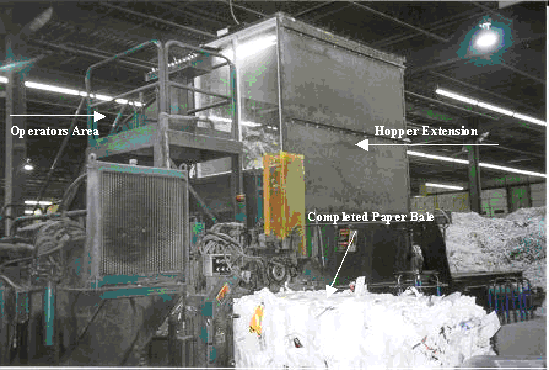
Figure 1 – Automatic Two Ram Horizontal Baler
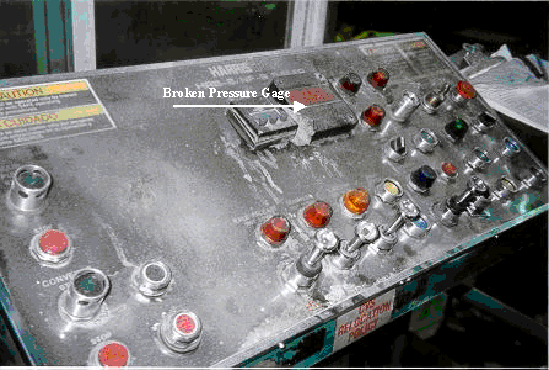
Figure 2 – Baler Control Panel
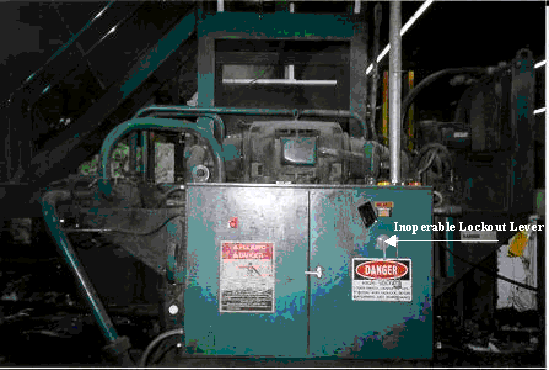
Figure 3 – Baler Power Panel
To contact Massachusetts State FACE program personnel regarding State-based FACE reports, please use information listed on the Contact Sheet on the NIOSH FACE web site Please contact In-house FACE program personnel regarding In-house FACE reports and to gain assistance when State-FACE program personnel cannot be reached.