Mining Publication: Machine Injury Prediction by Simulation Using Human Models
Original creation date: January 2003
Authors: DH Ambrose, JR Bartels, AJ Kwitowski, RF Helinski, S Gallagher
NIOSHTIC2 Number: 20023601
Digital Human Modeling for Design and Engineering Conference and Exhibition (June 2003, Montreal, QC, Canada), Society of Automotive Engineers, Inc., technical paper 2003-01-2190; :1-11
This paper presents the results of a study using computer human modeling to examine machine appendage speed. The objective was to determine the impact of roof bolter machine appendage speed on the likelihood of the operator coming in contact with the appendage. A contact means two or more objects intersecting or touching each other, e.g., the appendage makes contact with the operator's hand, arm, head, or leg. Incident investigation reports do not usually contain enough information to aid in studying this problem. Lab experiments with human subjects are also not feasible because of safety and ethical issues. As an alternative, researchers developed a computer model approach as the primary means to gather data. By simulating an operator's random behavior and a machine's appendage velocity, researchers can study the potential hazards of tasks where it is not possible to perform experiments with human subjects. Analysis information is helpful to the mining industry in terms of making recommendations that reduce the likelihood that roof bolter operators experience injury due to contact with a moving boom. Data analysis of roof bolter simulations show that the virtual operator's response time has little effect on the number of contacts experienced. Based on frequency and cross-tabulation, regardless of other variables, contact incidents were always greater when the boom was moving up, were always greater on the palm, and were always greater for the boom part of the machine. Also, regardless of boom speed, the 25th-percentile-sized operators experienced more contacts than operators of other sizes. Furthermore, regardless of boom speed, the 152-cm mine seam experienced more contacts than other seam heights tested. Results of a survival analytic approach suggest that controlling the boom speed is the most important factor in determining the risk of an operator making contact. Based on the data collected, boom speed greater than 41 cm/s results in a substantial increase in risk to the roof bolter operator and should probably be avoided. Speeds less than or equal to 25 cm/s are associated with a more modest relative risk, which represents an acceptable level of risk. Also, at speeds between 25 and 41 cm/s, there could be a particular boom speed in this range at which a significant inflection point in the relative risk estimates occurs. Based on the results, this issue needs to be addressed by future research.
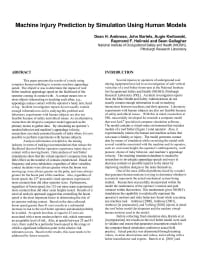
NIOSHTIC2 Number: 20023601
Digital Human Modeling for Design and Engineering Conference and Exhibition (June 2003, Montreal, QC, Canada), Society of Automotive Engineers, Inc., technical paper 2003-01-2190; :1-11
- An Analysis of Roof Bolter Fatalities and Injuries in U.S. Mining
- Analyzing Factors Influencing Struck-By Accidents of a Moving Mining Machine by Using Motion Capture and DHM Simulations
- Developing Random Virtual Human Motions and Risky Work Behaviors for Studying Anthropotechnical Systems
- A General Framework for Prioritizing Research To Reduce Injuries and Diseases in Mining
- Mining Roof Bolting Machine Safety: A Study of the Drill Boom Vertical Velocity
- SPONCOM - A Computer Program for the Prediction of the Spontaneous Combustion Potential of an Underground Coal Mine
- SponCom - Spontaneous Combustion Assessment Software - 2.0
- Technology News 545 - NIOSH Updates Spontaneous Combustion Assessment Software
- Upper Extremity Joint Moment and Force Predictions When Using a Joystick Control
- Verification and Validation of Roof Bolter Simulation Models for Studying Events Between a Machine and its Operator