Mining Topic: Programmable Electronic Systems
What is the health and safety problem?
Equipment control and emergency stop functions that were once hardwired can now be implemented with software and programmable electronic (PE) systems. This transition can result in increased flexibility because control functions can be rapidly changed or added via software, improved quality by efficiently providing a variety of control functions and features, and decreased costs. At the same time, PE systems have also created new concerns and challenges about worker safety, introducing software programs whose exact outcome for varied inputs can be uncertain. In some cases that even contain a moderate amount of software, all possible failure modes are not completely known, or the behavior under fault conditions cannot be completely determined for PE-based systems. Also, there are new failure modes that are different from electromechanical systems.
What is the extent of the problem?
PE systems are widely used in the mining industry, including in longwall mining equipment, continuous mining machines, and mine hoists. The safe application of this new technology has been a challenge because methodologies to evaluate these technologies for safety and health purposes did not exist for the mining industry. Currently, only the permissibility of electrical equipment is addressed; hence, the equipment can still be functionally unsafe when operated under PE control. This leaves unanswered questions on how to develop, evaluate, and maintain functional safety as well as how to effectively conduct accident investigations involving PE-based systems.
How is the NIOSH Mining program addressing this problem?
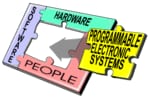
Programmable Electronic Systems.
A safety panel composed of representatives from the mining industry, equipment manufacturers, an industry trade association, the Mine Safety and Health Administration (MSHA), NIOSH Mining, and academia was formed to discuss safety issues of PE-based mining equipment. Additional project input was received from Penn State University and the University of Alabama, who completed an industry study to identify safety issues based on mine site visits.
Next, NIOSH researchers used the safety panel input to guide the development of a nine-part best practice recommendation reports to address the safety life cycle for programmable electronic systems. The reports consist of a nine-part series that address hardware and software for the life cycle stages of inception, design, approval and certification, commissioning, operation, change management maintenance, and decommissioning. These recommendations were developed as a joint project between NIOSH and MSHA. They are intended for use by mining companies, original equipment manufacturers, and aftermarket suppliers to these mining companies. Users of these reports are expected to consider the set in total during the design cycle
What are the significant findings?
A safety life cycle approach is needed to address all phases of a PE system. Safety must be analyzed at every step of the life cycle, in particular early in the requirements definition phase, and not be conducted only when the system design is completed. Addressing complexity is especially important in safety analysis because as PE-based systems proliferate, system sophistication and complexity escalate and increase the likelihood of design errors and new hazards.
What are the next steps?
The nine-part best practice recommendation documents should be used as a basis for a mining industry standard addressing the functional safety of PE-based systems. Other industries such as the chemical process industry have generated industry-specific standards for addressing the functional safety of PE-based systems. Also, the hazard and risk methods and techniques identified in the nine-part best practice recommendations could be applied to non PE-based mining equipment and mining processes.
- Addressing the Safety of Programmable Electronic Mining Systems: Lessons Learned
- A Complexity Assessment Methodology for Programmable Electronic Mining Systems
- Engineering Considerations and Selection Criteria for Proximity Warning Systems for Mining Operations
- A General Design and Implementation Procedure for Sensor-Based Electrical Diagnostic Systems for Mining Machinery
- A GPS Based System for Minimizing Jolts to Heavy Equipment Operators
- Handbook for Dust Control in Mining
- Heavy Construction Equipment Noise Study Using Dosimetry and Time-Motion Studies
- A Measurement Method for Determining Absorption Coefficients for Underground Mines
- Musculoskeletal Symptoms Among Operators of Heavy Mobile Equipment
- Operationalizing Normal Accident Theory for Safety-Related Computer Systems
- Programmable Electronic and Hardwired Emergency Shutdown Systems: A Quantified Safety Analysis
- Programmable Electronic Mining Systems: Best Practice Recommendations (In Nine Parts): Part 1: 1.0 Introduction
- Programmable Electronic Mining Systems: Best Practice Recommendations (In Nine Parts): Part 2: 2.1 System Safety
- Programmable Electronic Mining Systems: Best Practice Recommendations (In Nine Parts): Part 3: 2.2 Software Safety
- Programmable Electronic Mining Systems: Best Practice Recommendations (In Nine Parts): Part 4: 3.0 Safety File
- Programmable Electronic Mining Systems: Best Practice Recommendations (In Nine Parts): Part 5: 4.0 Independent Functional Safety Assessment
- Programmable Electronic Mining Systems: Best Practice Recommendations (In Nine Parts): Part 6: 5.1 System Safety Guidance
- Programmable Electronic Mining Systems: Best Practice Recommendations (In Nine Parts): Part 8: 6.0 Safety File Guidance
- Programmable Electronic Mining Systems: Best Practice Recommendations (In Nine Parts): Part 9: 7.0 Independent Functional Safety Assessment Guidance
- Safety Framework for Programmable Electronics in Mining