Mining Feature: Proximity Detection: A Continuing Research Imperative
Monday, December 3, 2012
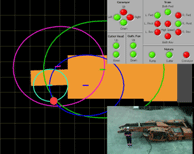
The NIOSH Intelligent Proximity Detection System uses multiple generators to determine the position of the worker relative to the equipment, only disabling those functions that would threaten worker safety.
So far this year five mine workers have been fatally injured in what are commonly referred to as pinning incidents, where the miner is between a moving piece of equipment and the rib or another machine. The NIOSH Office of Mine Safety and Health Research (OMSHR) is continuing research on an Intelligent Proximity Detection (iPD) system to help prevent pinning injuries and fatalities from happening.
OMSHR has developed specific research goals for preventing injuries involving powered machinery, and proximity detection is currently the primary research focus in this area. Acting as an impartial third party, OMSHR has evaluated commercially available proximity detection systems for both underground and surface mining. Based on these findings, recommendations for testing and implementing systems have been introduced and improvements are being developed.
Underground mining: OMSHR is developing a prototype intelligent proximity detection system that continuously monitors mine workers’ positions in relation to machines and established safety zones. Specific machine functions are disabled to prevent unsafe movement toward mine worker while allowing functions that do not put the worker at risk to remain operational.
What are the significant findings?
- OMSHR investigated the standing positions and visual attention locations for continuous mining machine operators, as well as safe operating speeds for mining machines.
- OMSHR has also developed sophisticated mathematical models of the magnetic fields used in proximity detection systems.
Based on these background studies, the iPD system was designed to provide situational protection based on the position of a mine worker relative to the machine. The iPD system has been shown to accurately track the position of mine worker and disable potentially hazardous machine motions.
For the latest information from MSHA, consult their single source page on the subject: MSHA Proximity Detection / Collision Warning Single Source Page
- An Active Proximity Warning System for Surface and Underground Mining Applications
- CFD Modeling of Spontaneous Heating in a Large-Scale Coal Chamber
- Effects of Far-Field Shearing Deformation on Fracturing Around an Underground Opening
- Engineering Considerations and Selection Criteria for Proximity Warning Systems for Mining Operations
- Innovative Safety Interventions: Feasibility of Using Intelligent Video for Machinery Applications
- Preventing Collisions Involving Surface Mining Equipment: A GPS-based Approach
- Programmable Electronic Mining Systems: Best Practice Recommendations (In Nine Parts): Part 3: 2.2 Software Safety
- Programmable Electronic Mining Systems: Best Practice Recommendations (In Nine Parts): Part 4: 3.0 Safety File
- Recommendations for Evaluating & Implementing Proximity Warning Systems on Surface Mining Equipment
- Rock Damage Characterisation from Microseismic Monitoring
- Test Results of Collision Warning Systems for Surface Mining Dump Trucks