Machine Assembler Crushed Between Machine Sections During Assembly
New Jersey FACE 00-NJ-040
![]() |
![]() |
Fatality Assessment & Control Evaluation Project
On June 5, 2000, a 53-year-old machine assembler was crushed between two parts of a large machine as a forklift attempted to move the parts together. The incident occurred at a machine fabrication shop that built and assembled industrial plastic processing machines. The victim had been working on a large precision coating machine and needed to connect the section containing the drive motor mechanism to the roller section. Both sections of the machine were set on metal blocks that leveled the machine and allowed access to a forklift. As the victim stood between the two sections to hold up a wire, a forklift operator positioned the lift under the drive section. This apparently caused one of the blocks to slip from underneath the machine, causing the top of the machine to pitch forward as it dropped to the floor. This forward movement was enough to pin the victim’s head between the two machine sections. NJ FACE investigators concluded that, to prevent similar incidents in the future, these safety guidelines should be followed:
- Employers should ensure that all loads on forklifts are properly positioned and secured before lifting.
- Employers should conduct a job hazard analysis of all work tasks with the participation of the workers.
- Employers should ensure that forklift operators are properly trained and certified according to the OSHA Industrial Truck regulation 29 CFR 1910.178.
INTRODUCTION
On June 15, 2000, NJ FACE personnel received a newspaper article describing a work-related fatality involving a forklift truck that occurred on June 5, 2000. A FACE investigator contacted the employer who requested that we call them at a later date to arrange an investigation. After subsequent telephone contacts, a site visit was conducted on October 24, 2000. During the visit, FACE investigators interviewed the employer and a witness, and photographed the incident scene and forklift. The machine involved in the incident was not available for examination as it had been delivered to the customer. However, the company did have photos of the machine. Additional information on the incident was gathered from the OSHA investigation file, the police report, and the medical examiner’s report.
The employer was a company that designed, manufactured, and assembled precision industrial machinery for applying plastic coatings. In business for nine years, the company had been at this plant for five years and employed 35 workers at the time of the incident. The company had a very basic on-the-job training program for forklift operators, most of whom had prior experience before being hired. Two safety committees were at the plant; one for plant safety that met every six weeks and a second for product safety design. A safety consultant was also available when needed. The victim was a 53-year-old lead machine assembler who had worked for the company for nearly three years. The company owner stated that he had over 22 years of experience in machine manufacture and assembly.
INVESTIGATION
The incident occurred at the company’s machine fabrication plant located in an urban industrial area. The company was housed in a large building that contained the assembly shop and offices. Specializing in producing precision industrial machines, the company served clients who ordered from stock plans or had the machine custom designed. Machine components were produced by subcontractors and delivered to the company for assembly at the fabrication plant. After assembly and testing, the machines were disassembled and delivered to the customer who reassembled it using directions provided by the company. The company would also reassemble the machines at the customer’s site on request.
Production of the machines was often precise to within millionths of an inch, requiring strict production methods in a clean and orderly production shop. The machine involved in the incident was a multi-roll coating head; a machine that used 16-inch diameter metal rollers to apply a plastic coating to a material running through the machine. At the time of the incident, the machine was being built in two separate sections: the drive section, which contained the drive motors and gears, and the roller section holding the large metal rollers. The drive section was wedge shaped, weighed 3,425 pounds and measured 31-inches-long, 93-inches-wide, and 57- inches-high. Connected with the roller section, the entire machine measured approximately ten feet long, eight feet wide, and six feet high. During assembly both sections were set on special metal blocks that lifted them a few inches off the floor, ensuring that they were perfectly level and accessible to a forklift.
The incident occurred on Monday, June 5, 2000 at 1:15 p.m. The victim had been lead man on assembling this machine. Throughout the morning, he had been assisted by the plant manager in preparing the sections for joining. The morning passed without incident and the two men broke for lunch around noontime. After lunch, they started work on joining the machine sections, planning on using a forklift to move the drive section against the roller section and bolting them together. The victim knelt between the two machine sections to hold up a wire, apparently to keep it from being damaged as the machine was lifted. The plant manager operated the forklift, positioning the blades under the drive section. Due to the wedge shape of the section, most of the weight of the machine was forward on the ends of the forks but was well within the 4,425 pound lifting capacity of the forklift. As the co-worker started to lift the machine up and back, the forward part of the machine tipped forward off the mounting blocks and fell a few inches to the floor. This movement caused the top of the section to suddenly pitch forward, crushing the victim’s head against the roller section behind him. The workers immediately called 911 and freed the victim by lifting the section with an overhead hoist. Police and EMS arrived and started resuscitation efforts, and the victim was transported to the local hospital where he was pronounced dead due to head injuries at 1:58 p.m.
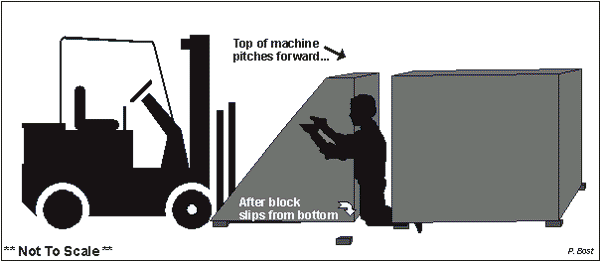
Figure 1. Illustration showing approximate locations of machine and victim
RECOMMENDATIONS/DISCUSIONS
Recommendation #1: Employers should ensure that all loads on forklifts are properly positioned and secured before lifting.
Discussion: The incident occurred after the forklift operator tried to lift a heavy, unevenly distributed load, which caused the load to become unbalanced and fall forward. To prevent future incidents, FACE recommends that all forklift loads be carefully positioned before lifting. If there is any possibility that the load may be unstable, it should be tied securely to the forks. Cranes and other types of equipment should be used for large or unusual loads that cannot be safely lifted with a forklift. Additional information is included in the attached NIOSH ALERT: Preventing Injuries and Deaths of Workers Who Operate or Work Near Forklifts
Recommendation #2: Employers should conduct a job hazard analysis of all work tasks with the participation of the workers.
Discussion: Proper planning can often find problems that could present a danger to workers. FACE recommends that employers and workers conduct a job hazard analysis of the work area at the start of a job and during major operations in the production. A job hazard analysis begins by reviewing the tasks of each worker and the equipment needed. Each task is examined for fall, electrical, chemical, environmental, or other hazards the worker may encounter. Afterwards, appropriate controls and safety training can be used to eliminate the hazards. More information can be found in the attached OSHA publication, Job Hazard Analysis.
Recommendation #3: Employers should ensure that forklift operators are properly trained and certified according to the OSHA Industrial Truck regulation 29 CFR 1910.178.
Discussion: All employers who use forklift trucks must comply with the new OSHA Powered Industrial Truck standard 29 CFR 1910.178. This standard requires classroom and hands-on training for the operators and must be specific to the worksite and equipment used. Trainers must be competent to train forklift operations. Operators must be certified as having passed the training and must be periodically reevaluated. It should be noted that the employer in this incident had come into compliance with the Powered Industrial Truck standard following the incident.
The Powered Industrial Truck standard and information on other OSHA regulations are available from the four local area offices in New Jersey or the federal OSHA website (www.osha.gov). Other sources for occupational safety and health information include the following:
U.S. Department of Labor, OSHA
On request, OSHA will provide information on safety and health standards. OSHA has several offices in New Jersey that cover the following counties:
Hunterdon, Middlesex, Somerset, Union, and Warren counties…………………..(732) 750-4737
Essex, Hudson, Morris, and Sussex counties…………………………………………..(973) 263-1003
Bergen and Passaic counties………………………………………………………………..(201) 288-1700
Atlantic, Burlington, Cape May, Camden, Cumberland, Gloucester,
Mercer, Monmouth, Ocean, and Salem counties……………………………………..(856) 757-5181
NJ Public Employees Occupational Safety and Health (PEOSH) Program
The PEOSH act covers all NJ state, county, and municipal employees. The act is administered by two departments; the NJ Department of Labor (NJDOL) which investigates safety hazards, and the NJ Department of Health and Senior Services (NJDHSS) which investigates health hazards. Their telephone numbers are:
NJDOL, Office of Public Employees Safety ……………………………………………(609) 633-3896
NJDHSS, PEOSH Program…………………………………………………………………(609) 984-1863
NJDOL Occupational Safety and Health On-Site Consultative Program
Located in the NJ Department of Labor, this program provides free advice to private businesses on improving safety and health in the workplace and complying with OSHA standards. For information regarding a safety consultation, call (609) 292-0404, for a health consultation call (609) 984-0785. Requests may also be faxed to (609) 292-4409.
New Jersey State Safety Council
The NJ Safety Council provides a variety of courses on work-related safety. There is a charge for the seminars. Their address and telephone number is: NJ State Safety Council, 6 Commerce Drive, Cranford, NJ 07016. Telephone (908) 272-7712
Internet Resources
Information and publications on safety and health standards can be easily obtained over the internet. Some useful sites include:
www.osha.gov – The US Department of Labor OSHA website, which include all OSHA regs.
www.cdc.gov/niosh/ – The CDC/NIOSH website.
www.state.nj.us/health/eoh/peoshweb/ – The NJDHSS PEOSH website. (Link updated 12/11/2007)
www.dol.gov/elaws/ – USDOL Employment Laws Assistance for Workers and Small Businesses
ATTACHMENTS
Job Hazard Analysis. OSHA 3071, US Department of Labor, Occupational Safety and Health Administration, Washington DC. 1998.
NIOSH ALERT: Preventing Injuries and Deaths of Workers Who Operate or Work Near Forklifts. DHHS (NIOSH) Publication 2000-112, December 1999. NIOSH Publications Dissemination, Cincinnati OH. Telephone 1-800-356-4674, website www.cdc.gov/niosh.
Fatality Assessment and Control Evaluation (FACE) Project
Investigation # 00-NJ-040-01
Staff members of the New Jersey Department of Health and Senior Services, Occupational Health Service, perform FACE investigations when there is a report of a targeted work-related fatal injury. The goal of the FACE Program is to prevent future incidents by studying and identifying the risk factors that contribute to workplace fatalities, by recommending intervention strategies, and by disseminating information to employers and employees. NJ FACE data is reported to NIOSH for trend analysis on a national basis. All identifiers are removed from the FACE reports and other data to protect the confidentiality of those who participate in the program.
NIOSH funded state-based FACE Programs include: Alaska, California, Iowa, Kentucky, Massachusetts, Minnesota, Missouri, Nebraska, New Jersey, Ohio, Oklahoma, Texas, Washington, West Virginia, and Wisconsin.
|
NJ Department of Health & Senior Services |
|
To contact New Jersey State FACE program personnel regarding State-based FACE reports, please use information listed on the Contact Sheet on the NIOSH FACE web site. Please contact In-house FACE program personnel regarding In-house FACE reports and to gain assistance when State-FACE program personnel cannot be reached.
Back to New Jersey FACE reports
Back to NIOSH FACE Web