Control of Exposure to Perchloroethylene in Commercial Drycleaning (Machine Design)
1997
DHHS (NIOSH) Publication Number 97-156
Hazard
Perchloroethylene (PERC) is the most commonly used drycleaning solvent. PERC can enter the body through respiratory and dermal exposure. Symptoms associated with exposure include: depression of the central nervous system; damage to the liver and kidneys; impaired memory; confusion; dizziness; headache; drowsiness; and eye, nose, and throat irritation. Repeated dermal exposure may result in dermatitis. NIOSH considers PERC a potential human carcinogen.
Controls
To reduce exposure to drycleaning solvents, a comprehensive control approach should be followed involving engineering measures, work practices, and personal protection. Engineering measures are the most effective means of control and should generally be considered first. Modern drycleaning machines can dramatically reduce exposures, save money in solvent costs, and permit easier compliance with safety, health and environmental regulations.
Types of Drycleaning Machines
- Drycleaning machines have evolved over time to better protect worker safety and health and the environment. Drycleaning machines encompass five “generations” which are currently used in the United States.
- 1st Generation: transfer machines These older and less expensive machines require manual transfer of solvent-laden clothing between a separate washer and dryer. Transfer machines were used exclusively until the late 1960s.
- 2nd Generation: dry-to-dry (vented) These machines are nonrefrigerated, dry-to-dry machines, using a one-step process that eliminates clothing transfer. Clothes enter and exit the machine dry. Second generation machines vent residual solvent vapors directly to the atmosphere or through a form of vapor recovery system during the aeration process.
- 3rd Generation: dry-to-dry (nonvented) Dry-to-dry machines with refrigerated condensers were introduced in the late 1970s and early 1980s. These nonvented machines are essentially closed systems, which are only open to the atmosphere when the machine door is opened. They recirculate the heated drying air through a vapor recovery system and back to the drying drum. These machines provide considerable solvent savings and reductions in PERC emissions over their predecessors.
- 4th Generation: dry-to-dry (nonvented with secondary vapor control) “Fourth generation” drycleaning machines are essentially “third generation” machines with controls to reduce residual PERC in the machine cylinder at the end of the dry cycle. These machines rely on both a refrigerated condenser and carbon absorber to reduce the PERC concentration at the cylinder outlet below 300 ppm at the end of the dry cycle. These machines are much more effective at recovering solvent vapors than machines equipped with a carbon adsorber or refrigerated condenser alone.
- 5th Generation: dry-to-dry (nonvented with secondary vapor control and drum monitor) “Fifth generation” machines, widely used in Germany but seldom in the United States, have the same features as “fourth generation” machines. However, they also have a monitor inside the machine drum and an interlocking system to ensure that the concentration is below approximately 300 ppm before the loading door can be opened.
Exposures and Occupational Limits
- The current OSHA permissible exposure limit (PEL) for PERC is 100ppm, as an 8-hr time-weighted average (TWA). The acceptable ceiling concentration is 200 ppm for 5 min in any 3-hr period, not to exceed a maximum peak of 300ppm.
- “4th and 5th generation” machines, unlike their predecessors, can maintain worker exposures below the OSHA maximum peak of 300 ppm.
Peak (ppm) | TWA (ppm) | |
---|---|---|
1st Generation: | 1,000-4,000 | 40-60 |
2nd Generation: | 1,000-4,000 | 15-20 |
3rd Generation: | 1,000-4,000 | 15-20 |
4th Generation: | 10-300 | <3 |
5th Generation: | 10-300 | <2 |
Important Machine Design Features
The following drycleaning machine design features are important for shop owners to consider when purchasing new equipment to minimize worker exposures to PERC.
- Dry-to-dry design that eliminates clothing transfer
- Primary & secondary vapor control systems
- The primary vapor control on each machine should have the following features:
- A refrigerated condenser that can achieve outlet temperature of 45F, within 10 min of initiation of cool-down
- The ratio of machine capacity to compressor size should be 12 or less
- The secondary vapor control on each machine should have the following features:
- A carbon adsorber capable of reducing the PERC concentration in the cylinder at end of the drycycle below 300 ppm
- Carbon capable of holding 200% of maximum quantity of PERC that it is designed to capture
- Carbon desorption that does not involve contact between steam or any other form of water andcarbon
- A drying sensor that automatically controls the dry cycle by monitoring the solvent recovery process.
- A door locking mechanism that prevents the loading and unloading door of the drycleaning machine from opening before the end of the dry cycle.
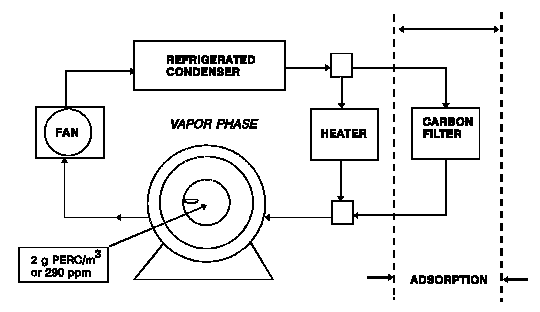
Figure 1. Vapor phase of the “4th and 5th Generation” dry-cleaning machines. The large, regenerable, carbon filter is used to reduce concentrations in the drum below approximately 300 ppm during the final phase of the dry cycle.
Retrofitting
- Retrofitting is a less expensive option than purchasing new equipment. Retrofitting is not always practical and can be fairly difficult depending on the machine. A refrigerated condenser could be retrofitted on many machines currently using a water- or air-cooled condenser. This retrofit lowers short-term exposures by approximately 50% and increases solvent mileage. A carbon adsorber could be retrofitted onto a 3rd Generation machine. This retrofit lowers short-term exposures by approximately 90%.
Other Machine Features
- Other machine features that help reduce occupational exposures to PERC include: safety switches to insure closed-door operation; safety interlocks for heating, cooling and still system failures; emission-free still cleaning devices; regenerable solvent filtration systems; emission free solvent filling devices; seals and fittings with tighter tolerances that resist deterioration; process controls that lower garment residuals after drying process; and controls that reduce vapors escaping from the button and lint traps.
A NIOSH technical report, Control of Health and Safety Hazards in Commercial Drycleaners: Chemical Exposures, Fire Hazards, and Ergonomic Risk Factors, has been published on this subject. This document is one in a series of seven HAZARD CONTROLS concerning control of hazards in the drycleaning industry that are available free upon request.
*NIOSH is the Federal agency responsible for conducting research and making recommendations for preventing work-related illnesses and injuries. All HAZARD CONTROLS are based on research studies that show how worker exposures to hazardous agents or activities can be significantly reduced.
Acknowledgments
The principal contributors to this publication are Gary S. Earnest, Rosmarie T. Hagedorn, and Jerome P. Flesch.
This document is in the public domain and may be freely copied or reprinted. NIOSH encourages all readers of this HAZARD CONTROLS to make it available to all interested employers and workers.
Control of Exposure to Perchloroethylene in Commercial Drycleaning (Machine Design)