General Safety and Health Provisions for Construction
October 2003
DHHS (NIOSH) Publication Number 2004-101
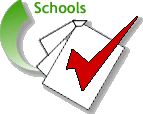
Self-Inspection Checklist
Name of school: |
Date of inspection: |
Career-Technical program/course/room: |
Signature of inspector: |
Guidelines
This checklist covers selected construction regulations issued by the U.S. Department of Labor, Occupational Safety and Health Administration (OSHA) under 29 CFR 1926. It applies to temporary worksites associated with construction, alteration, demolition, or repair work, including painting and decorating. Fixed facilities, such as Career-Technical educational classrooms, are not covered by these regulations. The regulations cited apply only to private employers and their employees, unless adopted by a State agency and applied to other groups such as public employees. A yes answer to a question indicates that this portion of the inspection complies with the OSHA or U.S. Environmental Protection Agency (EPA) standard, or with a nonregulatory recommendation. Definitions of terms in bold type are provided at the end of the checklist.
The following construction regulations have not been covered in a checklist: asbestos (29 CFR 1926.58); hazard communication (29 CFR 1926.59); battery locations and battery charging (29 CFR 1926.441); cranes, derricks, elevators, and conveyors (subpart N – 29 CFR 1926.550 to 1926.556); motor vehicles, mechanized equipment, and marine operations (subpart O – 29 CFR 1926.600 to 1926.606); excavations (subpart P – 29 CFR 1926.650 to 1926.652); concrete and masonry construction (subpart Q – 29 CFR 1926.700 to 1926.706); steel erection (subpart R – 29 CFR 1926.750 to 1926.752); underground construction, caissons, cofferdams, and compressed air (subpart S – 29 CFR 1926.800 to 1926.804); demolition (subpart T – 29 CFR 1926.850 to 1926.860); blasting and use of explosives (subpart U – 29 CFR 1926.900 to 1926.914); power transmission and distribution (subpart V – 29 CFR 1926.950 to 1926.960); and rollover protective structures and overhead protection (subpart W – 29 CFR 1926.1000 to 1926.1003). Please consult the OSHA regulations for these situations.
- Is an injury prevention program established for construction worksites? [29 CFR 1926.20(b)(1)]
- Does the program include frequent regular inspections by a designated competent person of the worksite, materials, and equipment? [29 CFR 1926.20(b)(2)]
- When machines, tools, materials, or equipment are identified as unsafe, is one of these procedures followed?
- they are tagged
- the controls are locked to render them inoperable; or
- they are immediately removed from the work area?
[29 CFR 1926.20(b)(3)]
- Are only qualified employees (by training or experience) permitted to operate machinery? [29 CFR 1926.20(b)(4)]
- Are all employees and students trained to recognize and avoid unsafe conditions? Do they know the regulations applicable to the work environment? [29 CFR 1926.21(b)(2)]
- Have employees and students been instructed regarding the safe handling and use of poisons, caustics, and other harmful substances? Are they aware of the hazards, personal hygiene, and personal protective measures required? [29 CFR 1926.21(b)(3)]
- In areas where harmful plants or animals may be present, have employees and students been instructed regarding the hazards, how to avoid injury, and first aid procedures to be used in the event of injury? [29 CFR 1926.21(b)(4)]
- Have employees and students who are required to handle or use flammable liquids, gases, or toxic materials been instructed in the safe handling and use of these materials? [29 CFR 1926.21(b)(5)]
- Have all employees and students who are required to enter confined or enclosed spaces been instructed in the nature of the hazards involved, the necessary precautions to take, and the use of protective and emergency equipment required? [29 CFR 1926.21(b)(6)(i)]
- Are medical personnel available for advice and consultation? [29 CFR 1926.23 and 1926.50(a)]
- Are provisions made in advance of any project for prompt medical attention in case of serious injury? [29 CFR 1926.50(b)]
- If emergency medical care is not readily available, is a certified person available to render first aid? [29 CFR 1926.50(c)]
- Are first-aid supplies readily available at the worksite? [29 CFR 1926.50(d)(1)]
- Are first-aid supplies at the worksite in a weatherproof container with individual sealed packages for each type of item? [29 CFR 1926.50(d)(2)]
- Are first-aid supplies checked to replace expended items each time they are sent to the worksite and at least weekly if left at the worksite? [29 CFR 1926.50(d)(2)]
- Is transportation available for taking an injured person to medical care, or is a communication system available for contacting an ambulance service? [29 CFR 1926.50(e)]
- Are telephone numbers of physicians, hospitals, or ambulances conspicuously posted at the worksite? [29 CFR 1926.50(f)]
- Is an adequate supply of drinking water at or near the worksite? [29 CFR 1926.51(a)(1)]
- If portable drinking water containers are used at the worksite, can they be tightly closed and are they equipped with a tap? [29 CFR 1926.51(a)(2)]
- Is dipping water from a drinking water container and use of a common drinking cup prohibited? [29 CFR 1926.51(a)(2) and (4)]
- Are washing facilities at or near the worksite for employees and students who handle paints, coatings, pesticides, or other harmful contaminants? [29 CFR 1926.51(f)]
- Has an effective fire protection and prevention program been established at the worksite through all phases of construction, repair, or alteration? [29 CFR 1926.24]
- Has all form and scrap lumber with protruding nails, and all other debris been cleared from work areas, passageways, and stairs in and around buildings or other structures? [29 CFR 1926.25(a)]
- Is combustible scrap and debris removed from the work area at regular intervals during the course of construction? [29 CFR 1926.25 (b) and 1926.252(c)]
- Are containers provided for the collection and separation of waste, trash, oily and used rags, and other refuse? [29 CFR 1926.25(c)]
- Are all solvent wastes, oily rags, and flammable liquids kept in fire-resistant, covered containers until removed from the work area? [29 CFR 1926.252(e)]
- Are all construction areas, aisles, stairs, ramps, runways, corridors, offices, labs, shops, and storage areas where work is in progress well lighted? [29 CFR 1926.26 and 1926.56]
- Is appropriate personal protective equipment used in all operations where hazardous conditions exist? [29 CFR 1926.28]
- Material Handling and Storage Are all materials that are stored in tiers stacked, racked, blocked, interlocked, or otherwise secured to prevent sliding, falling, or collapse? [29 CFR 1926.250(a)(1)]
- Is the minimum safe load limit of floors within buildings and structures, in pounds per square foot, conspicuously posted in all storage areas? [29 CFR 1926.250(a)(2)]
- Are maximum safe loads always maintained? [29 CFR 1926.250(a)(2)]
- Are aisles and passageways kept clear to provide for the free and safe movement of material-handling equipment and people? [29 CFR 1926.250(a)(3)]
- Are such areas kept in good repair? [29 CFR 1926.250(a)(3)]
- Where a difference in road or working level exists, are means such as ramps, blocking, or grading provided to ensure the safe movement of vehicles between two levels? [29 CFR 1926.250(a)(4)]
- Is material stored inside buildings under construction placed more than 6 feet away from any hoistway or inside floor openings, or more than 10 feet away from an exterior wall? [29 CFR 1926.250(b)(1)]Note: The exterior wall must not extend beyond the top of the material stored.
- Are noncompatible materials segregated in storage? [29 CFR 1926.250(b)(3)]
- Are bagged materials stacked by stepping back the layers and cross-keying the stack at least every 10 bags? [29 CFR 1926.250(b)(4)]
- Is it prohibited to store more material on scaffolds or runways than needed for the immediate operation? [29 CFR 1926.250(b)(5)]
- Are brick stacks limited to 7 feet in height? [29 CFR 1926.250(b)(6)]Note: When a loose brick stack reaches a height of 4 feet, it must be tapered back 2 inches on every foot of height above the 4 foot level.
- When masonry blocks are stacked higher than 6 feet, is the stack tapered back one half block per tier above the 6-foot level? [29 CFR 1926.250(b)(7)]
- Are all nails withdrawn from lumber before lumber is stacked? [29 CFR 1926.250(b)(8)(i)]
- Is lumber stacked on level and solidly supported sills? [29 CFR 1926.250(b)(8)(ii)]
- Is lumber stacked in a stable, self-supporting manner? [29 CFR 1926.250(b)(8)(iii)]
- Are all lumber piles 20 feet or less in height? [29 CFR 1926.250(b)(8)(iv)]
- Are lumber piles to be handled manually stacked a height of 16 feet or less? [29 CFR 1926.250(b)(8)(iv)]
- Are all structural steel, poles, pipe, bar stock and other cylindrical material (unless racked) stacked and blocked to prevent spreading or tilting? [29 CFR 1926.250(b)(9)]
- Are all masonry walls over 8 feet in height braced to prevent overturning? [29 CFR 1926.706(b)]
Definitions
Certified person: a person who has a valid certificate in first-aid training from the U.S. Bureau of Mines, the American Red Cross, or equivalent training that can be verified by documentary evidence. [29 CFR 1910.50(c)]
Confined or enclosed spaces: any space having a limited means of egress, which is subject to the accumulation of toxic or flammable contaminants or has an oxygen-deficient atmosphere. Confined or enclosed spaces include, but are not limited to, storage tanks, process vessels, bins, boilers, ventilation or exhaust ducts, sewers, underground utility vaults, tunnels, pipelines, and open top spaces more than 4 feet in depth such as pits, tubs, vaults, and vessels.