Haul Truck Research Roadmap Report 2020
Executive Summary
Haul-truck-related accidents continue to be one of the leading health and safety concerns in mining. However, it is still unclear why these accidents continue to occur. The National Institute for Occupational Safety and Health (NIOSH) is not alone in searching for answers. In 2018, the Mine Safety and Health Administration (MSHA) started a Powered Haulage Safety Initiative to prioritize the prevention of haul-truck-related accidents and aims to propose rulemaking in the future. The mining industry is also responding with renewed efforts to alert mineworkers to the hazards posed by powered haulage and to promote best practices related to vehicle collisions, seat belt use, and conveyor safety. These best practices may include administrative controls, implementation of simple technologies such as seat belt interlocks, or the development of new technologies such as automation and collision avoidance and warning systems (CXS). However, the use of these advanced systems can make the problem even more complex, and it may take many years before implementation across the industry provides widespread benefit. Some industry groups are also mobilizing efforts to explore the effects of automation and CXS, but they are primarily Australian and focused on large mines.
To study this issue, NIOSH initiated a project to identify current gaps and create a roadmap for future research. More specifically, NIOSH aims to inform future work by identifying and characterizing haul-truck-related health and safety issues through a systematic evaluation of previous research, stakeholder needs, accidents and injuries, operators’ perspectives, and both administrative and technological interventions. As part of this effort, NIOSH also recognizes the urgent need to provide the mining industry with solutions and interventions related to issues that are currently affecting the mining industry and mitigate the risks associated with haul truck operations.
This report presents NIOSH’s initial findings to identify critical research, development, communication, and implementation gaps. To this point, NIOSH has held discussions with stakeholders, performed a survey of existing technologies, and analyzed haul-truck-related fatal accidents. Based on this preliminary work, NIOSH believes that there is a systemic lack of development, implementation, and integration of haul-truck-related health and safety interventions—both administratively and technologically. Work is being done in isolation or at too low of a level to be effective, such as developing technology without consideration for the users or system implementation. Examples of these gaps will be discussed in detail throughout the report.
NIOSH asserts that a systems approach should be taken to fully integrate new and previously developed interventions throughout operations to achieve maximum benefit across the mining industry. This approach takes into account the interactive and interdependence of both external and internal forces within each operation. Specifically, NIOSH identified 12 key areas across four system levels—external, organizational, workers, and environment and technology—where significant gaps exist (see Table 1). Each area is further discussed on this page and includes the state of the industry, specific concerns, and NIOSH’s ability to address these problems.
Table 1. Haul Truck Health and Safety System Gaps by System Level
External | Organizational | Workers | Environment and Technology |
---|---|---|---|
Regulation Instances where regulation does not align with the current state of the industry |
Policies and Procedures Instances where policies and procedures are not appropriate, effective, or communicated |
Human-Centered Design Human-machine-environment interactions where human-task mismatches exist |
Infrastructure Systems, networks, or installations where support, maintenance, reliability, or investment gaps exist |
Standards and Guidelines Instances where there are insufficient or multiple standards or guidelines |
Communication Instances where information or expectations are not transferred |
Situational Awareness Processes or interventions that limit or do not provide sufficient information or understanding |
Interoperability Systems, networks, or installations where communication and compatibility gaps exist |
Industry Forum Lack of a cohesive group, venue, or openness to facilitate sharing of information and exploration |
Workforce Aspects of the workforce composition at all levels that lead to gaps in communication, expectations, or inclusion |
Trust Instances where lack of trust (e.g., among people, technology, organization) leads to increased risk |
Analytics Systems, databases, or processes where gaps in processing, application, or consideration exist |
(For more information on the identified gaps, click the appropriate hyperlinked text to learn more.)
Out of the 12 key areas, NIOSH identified 21 action items for further consideration. These action items are not an exhaustive list but were identified as areas that NIOSH can lead or support the mining industry in relation to haul truck health and safety. Overall, NIOSH has a strong background in systems research and is uniquely qualified to help the mining industry as a neutral agency with multidisciplinary expertise. Out of the 21 areas, NIOSH has prioritized the following five activities to lead and begin acting on.
- Stakeholder Engagement: Mine Automation and Emerging Technologies Partnership
(Action Item 1; External, Regulation) - Intervention Research: Change Management for the Implementation of New Technologies
(Action Item 5; Organizational, Communication) - Basic/Etiologic and Educational Research: Surface Mine Wireless Communications Networks
(Action Item 15; Environment and Technology, Infrastructure) - Capacity Building: Engineering Systems Thinking
(Action Item 16; Environment and Technology, Infrastructure) - Intervention Research: Control/Dispatch Operator Interface Design
(Action Item 18; Environment and Technology, Interoperability)
(For more information on the above action items, click the hyperlink to jump to the full description that appears lower on this page.)
Roadmap Vision
Currently, there is a systemic lack of development, implementation, and integration of haul-truck-related health and safety interventions. Work is being done in isolation or at too low of a level to be effective. A systems approach should be taken to fully integrate new and previously developed interventions to achieve maximum benefit across the mining industry.
Introduction
Problem
Haul-truck-related accidents continue to be one of the leading health and safety concerns in mining, where haul trucks are wheeled vehicles used to haul material or equipment. However, it is still unclear why these accidents continue to occur and what should be done to prevent and mitigate them.
Burden
Consistently, powered haulage accounts for the greatest number of fatal accidents in the mining industry, where powered haulage includes both mobile equipment and powered conveyors. Powered haulage historically and continually accounts for approximately half of all mining fatal accidents every year [1]. Recently, 50% (14 of 28) of the fatal accidents in 2017 and 48% (13 of 27) in 2018 were classified as powered haulage [2]. In these same years, 6 of 28 and 6 of 27 fatal accidents were haul-truck-related [2]. Since haul trucks are attributed to nearly one-quarter of all fatalities in 2017-2018, a strong need exists to address this issue.
Haul truck health and safety concerns also have the potential to affect many workers. In the U.S., according to the Bureau of Labor Statistics (BLS) May 2018 Occupational Employment Statistics data, there are approximately 38,140 workers employed as heavy or industrial truck drivers and 8,410 heavy vehicle and mobile equipment service technicians and mechanics in mining or in support of the mining industry [3]. In fact, haul trucks account for over 45% of the mining equipment market [4], and there are currently estimated to be over 48,500 active haul trucks (over 90 tons) at surface mines worldwide [5]. However, these numbers are likely an underestimate due to the large number of delivery drivers and customer drivers exposed to the same risks when entering mine sites.
Additionally, the emergence of collision avoidance and warning systems (CXS) may increase the potential for haul-truck-related health and safety concerns. As one example of the emergence of this technology, the Republic of South Africa has made collision avoidance systems mandatory on underground and surface mobile equipment; however, minimal validation testing has been conducted [6, 7]. It is unclear how well these systems will work and how they may affect the mining system overall. However, the trend is continuing within the U.S., where MSHA has also expressed interest in rulemaking in surface haulage. MSHA has already mandated proximity detection systems (i.e., collision avoidance systems) on place-changing continuous mining machines [8] and proposed a rule for underground mobile haulage [9]. Moving forward, MSHA has indicated that it would work on a proposed rule related to surface mobile equipment and powered haulage in its regulatory agenda [10].
Similarly, there is also an industry interest in autonomous haul trucks. There are currently three companies in Australia (Rio Tinto, BHP, and Fortescue Metals Group) operating full- and semi-autonomous fleets [11], another company in Canada (Suncor) with the world’s largest autonomous haul truck and planning to implement 150 autonomous vehicles over the next six years [12], and one mine in the U.S. that is currently piloting five autonomous haul trucks [6]. While there have not yet been any fatal accidents or injuries related to these systems, there have been numerous incidents and collisions [13]. As these systems become more prevalent and intermixed with manned operations, there is some concern that these technological solutions might inadvertently create new exposures and risks.
Need
Over the past two decades, NIOSH, MSHA, and other industry stakeholders have conducted research and developed various interventions (e.g., pre-shift pocket card, CXS) to help address haul-truck-related issues. This work has identified many of the common haul-truck-related accident and injury causes, but more work needs to be done to clarify why these types of incidents continue to occur. Preliminary NIOSH work includes the creation of a classification system for haul truck accidents [14], developing ergonomic recommendations (e.g., ErgoMine) [15], and assessing safety technologies [16, 17, 18] to improve haul truck safety. Building on this research, a concerted effort to compile this previous work and identify additional gaps would allow NIOSH to more systematically plan and direct future research that may better address this ongoing issue.
In accordance with previous accident analyses by NIOSH [19, 20, 21], specific focus should be given to identifying and characterizing human-machine interface issues, especially those related to human performance, machine control, and the identification of hazards. With a large percentage of the area around a haul truck being in a blind spot for the operator and the cab being fully enclosed and elevated, operators are highly reliant on policies and procedures as well as the information transmitted (e.g., dispatch radio) and presented by the technology (e.g., CXS) to understand their environment. Furthermore, the mining environment is dynamic and ever-changing [22], requiring operators to constantly be vigilant. Current NIOSH research also suggests that even safety professionals fail to identify a significant portion of workplace hazards at mine sites [23]. More work needs to be done to better understand what information haul truck operators need to safely operate their vehicles, identify hazards, and maintain situational awareness as well as how these goals can be achieved through effective interventions.
NIOSH is well-positioned to perform further investigation into haul truck health and safety issues, as the Institute has completed decades of haul-truck-related work and has multidisciplinary expertise. NIOSH also has experience with engineering and human factors research on mobile proximity detection systems for underground mobile equipment [24]. As a federal agency, NIOSH will also be able to direct research funding priorities using evidence-based rationale. Unlike mine operators or labor organizations, NIOSH is an unbiased entity with cross-sector expertise that investigates issues at large and small mines alike.
Impact
Given the problem and the need, the primary goal of this effort is to identify research, development, communication, and implementation gaps related to haul truck health and safety. Through the process of gap exploration, this work will also identify user requirements that can be used to design, develop, and improve safety interventions related to haul trucks. Overall, NIOSH is working to provide the industry with clearer direction and actionable solutions to address health and safety concerns related to haul trucks.
Background
Over the years, numerous researchers have investigated haul-truck-related accidents and injuries [21, 25, 19, 20, 26]. In general, these incidents have been shown to be related to vehicle control and hazard recognition. An analysis of 152 fatalities between 1995 and 2014 found that 42% involved loss of control of the haul truck (e.g., speeding, backing over a drop-off, drowsiness) and 11% of the fatalities involved berming hazards [20]. Similarly, an earlier analysis of non-fatal accidents also found that operator failures (e.g., fatigue, error) and ground control hazards (i.e., hidden voids) were two of the most commonly reported contributing factors [19]. The previous analyses also recognized the contribution of human performance [21]. Monotonous driving, rough roads, rapidly changing conditions, limited visibility, and low responsiveness make operating haul trucks challenging. However, operator error does not provide the whole picture. It is necessary to also consider latent causes (e.g., poor policies and procedures) at all levels of the work system [27, 28].
Numerous methods exist to study accidents and assess risk on a systems level, including the Swiss Cheese Model [29, 30, 31], the Human Factors Analysis and Classification System (HFACS) [32, 33], AcciMap [34], Nertney Wheel [35], and others [36]. These models include various system levels (Table 2) that can be grouped into four overarching categories: external, organizational, workers, and environment and technology.
- External. Industry-wide forces that influence the adoption of health and safety interventions (e.g., courts, legislators, government regulatory agencies, standards commissions, associations, unions, insurance companies, neighbors).
- Organizational. Attributes of a mining company related to decision-making or policy and procedure creation that can affect the health and safety of workers (e.g., board of directors, corporate, accounting and finance, engineering, safety, training, maintenance, IT, culture).
- Workers. Individual workers at a mine site that make decisions or take actions that can affect the health and safety of themselves or others (e.g., equipment operators, maintenance workers, contractors, customers).
- Environment and Technology. Conditions, systems, solutions, and interventions at a mine site that affect the health and safety of workers (e.g., environmental hazards, engineering and administrative controls).
Table 2. Systems Theory-Based Levels of the Work System
Swiss Cheese | HFACS | AcciMap | Nertney Wheel | Other | |
---|---|---|---|---|---|
External | Systemic | External |
Regulators, |
External | |
Organizational | Workplace |
Organizational, |
Company, |
Procedural |
Company, |
Workers | Direct | Unsafe Acts | Staff | Personnel | Employees |
Environment and Technology |
Equipment, |
Preconditions | Work |
Environment, |
Acts, |
In addition to studying accidents and assessing risk on a systems level, mining companies and organizations are also making efforts to address vehicle interaction concerns more holistically and practically. The Earth Moving Equipment Safety Round Table (EMESRT)—a global initiative that formed among major mining companies in 2005 to advance the design of equipment to improve safe operability and maintainability beyond standards—recently updated its vehicle interaction group’s nine-level defensive control model as a part of its “Performance Requirements for Vehicle Interaction Systems (PR-5A)” (Table 3) [37]. This model was developed in conjunction with manufacturers and mine operators to provide a more practical interpretation of health and safety controls [37]. The model has also been adopted by the International Council on Mining and Metals (ICMM) and is included as a part of its critical control management approach [38]. The ICMM also has a vehicle interaction initiative, “Innovation for Cleaner Safer Vehicles,” that aims to “promote collision avoidance technology capable of eliminating fatalities from vehicle interactions so that it is available to mining companies by 2025” [39]. The ICMM plans to achieve this goal by creating a knowledge hub, creating a maturity framework, generating technology specifications, increasing communication and engagement, and supporting capacity building. In other efforts, the Mine Safety and Health Research Advisory Committee (MSHRAC) formed a workgroup to provide recommendations on potential health and safety issues related to the implementation of automation and other advanced technologies in U.S. metal mining [40]. While the final report was focused on automation in metal mining and was not specific to surface mining, many of the key findings relate to human technology interaction with direct applicability to general vehicle interaction concerns.
Table 3. EMESRT's Nine-Level Control Model
Categories | Definition | Levels | Examples | Time Frame |
---|---|---|---|---|
Design Controls | Improvements in equipment and mine design | Level 1: Site Requirements | Equipment specifications, standards, mine design/plans |
Years |
Design Controls | Improvements in equipment and mine design | Level 2: Segregation Controls | Berms, access control, traffic segregation, work planning separating mining activities | Months |
Operation Controls | Optimization of operations | Level 3: Operating Procedures | Formal operating and maintenance practices: e.g. road rules, communication protocols, work instructions, isolations, etc. | Weeks |
Operation Controls | Optimization of operations | Level 4: Authority to Operate | Training, licenses, induction, site access control, operator experience, etc. |
Days |
Operation Controls | Optimization of operations | Level 5: Fitness to Operate | Fatigue and stress state, alcohol and other drugs management, medicals to confirm capability, operator experience, etc. | Shifts |
Operation Controls | Optimization of operations | Level 6: Operating Compliance | Equipment pre-start check, equipment health monitoring, operator performance monitoring, etc. | Hours |
Reactive Controls | Systems to manage residual risk | Level 7: Operator Awareness | Cameras, live maps, mirrors, lights, visible delineators, simple proximity alerts | Minutes |
Reactive Controls | Systems to manage residual risk | Level 8: Advisory Controls | Alerts with advice: e.g. directional proximity alerts, fatigue monitoring systems, over-speed, vehicle stability | Seconds |
Reactive Controls | Systems to manage residual risk | Level 9: Intervention Controls | Non-operator intervention: equipment slow/stop, interlock for start or rollback, retarder, etc. |
Milliseconds |
Related to the efforts of these groups, the development of safety controls, administrative or engineering, also falls into phases of the design cycle. However, in order to combat incompatibilities and unintended consequences, it is critical that the mining industry takes a more user-centric approach such as human-centered design [41]. As an example, Figure 1 depicts the traditional design cycle annotated with human-centered design activities, where the user is incorporated into the design process from beginning to end. It is also important to note that just as the design process is iterative, so can be the human-centered design contributions. In this graphic, the iterative nature is only explicitly denoted around the design phase, but many stages can and should be repeated to create a successful intervention.
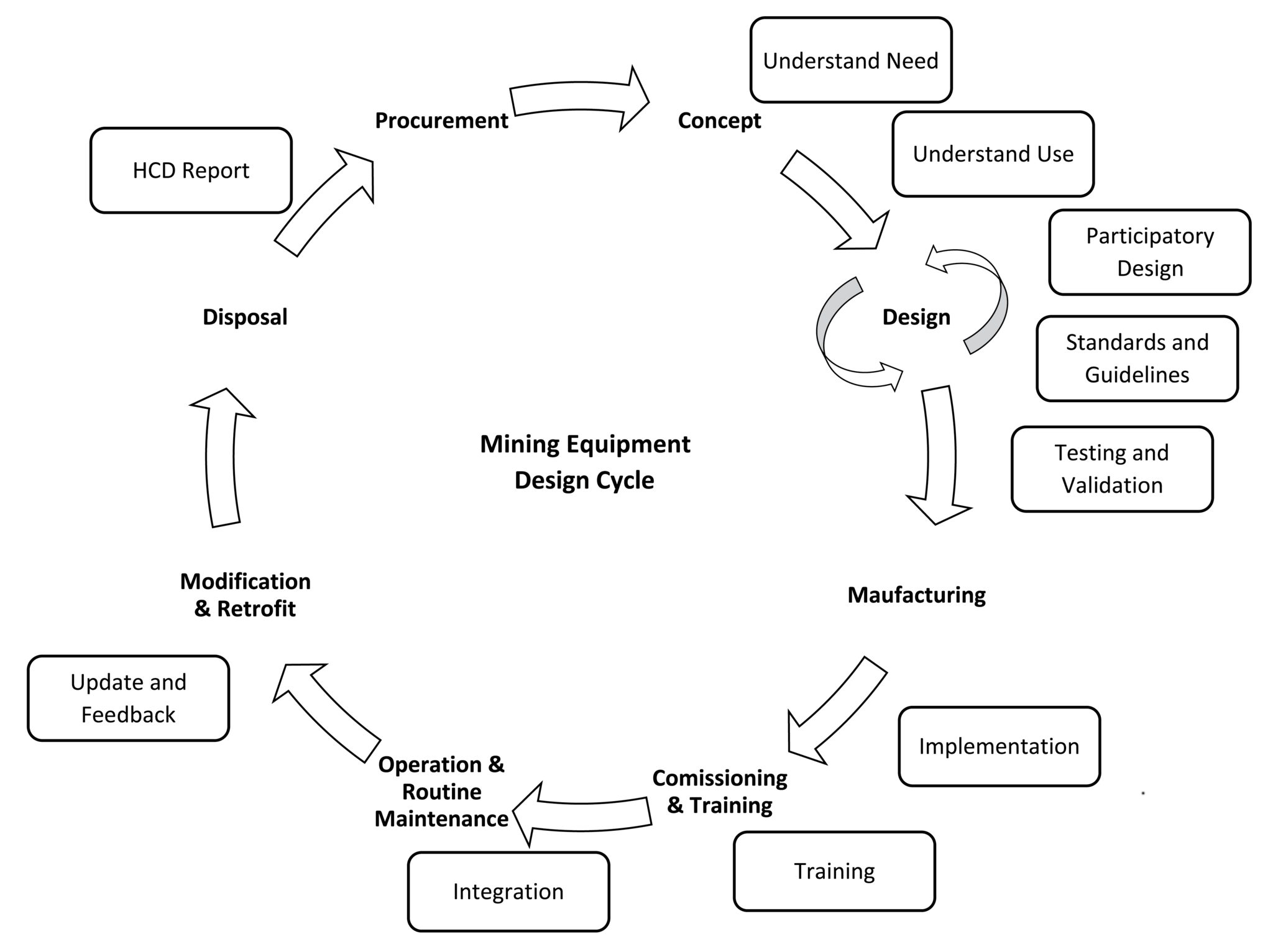
Figure 1. Graphic depicting the typical mining equipment design cycle with human-centered design (HCD) activities associated with each stage. Adapted from Horberry, Burgess-Limerick, and Steiner [43]. Click for larger image.
Beyond human-centered design, human factors considerations can similarly contribute to improved intervention development in other ways, such as health and safety management systems (HSMS). NIOSH supports the mining industry in translating its research to practice in many ways and across many phases of development. NIOSH aims to accomplish this through identifying needs, evaluating workplace solutions, communicating implementation information, and evaluating impact. Specifically, NIOSH uses six core elements to impact health and safety: partnerships, intramural science, extramural science, technology transfer, communication, and evaluation [42].
Research Objective: Current Project
The objective of the current project, Characterization of Haul Truck Health and Safety Issues, is to develop a roadmap to inform current and future health and safety research related to haul trucks by identifying and characterizing haul truck health and safety issues through a systematic evaluation of previous research, stakeholder needs, accidents and injuries, operators’ perspectives, and administrative and technological interventions. Additionally, NIOSH also recognizes the urgent need to provide the mining industry with relevant and current solutions and interventions and to mitigate the risks associated with haul truck operations.
Methods
Stakeholder Discussions and Mine Visits
In order to develop a focused research protocol, NIOSH researchers engaged industry stakeholders in various ways to capture their health and safety concerns related to haul trucks. NIOSH researchers presented their plan at two large meetings (proximity detection systems partnership, MSHRAC), held discussions with two representative industry associations (California Construction and Industrial Materials Association [CalCIMA], Pennsylvania Aggregates and Concrete Association [PACA]) and four mine operators (Graniterock, Marigold, Barrick, Freeport McMoRan), and made numerous site visits. Through these discussions, NIOSH researchers targeted four overarching areas: challenges, solutions, state of the industry, and emerging technologies. Researchers asked stakeholders the following general questions:
- What is your biggest concern related to haul truck health and safety?
- What makes this issue particularly challenging?
- What are some of the other health and safety challenges you face related to haul trucks?
- What are your top three concerns?
- What are some solutions you have successfully implemented?
- Where do you think the industry as a whole is on finding solutions for these health and safety issues?
- What do you think of autonomous haul trucks?
- How do you see the industry actually implementing automation related to haul trucks? (In phases? Right to full automation? Not for a long time?)
Technology Survey
NIOSH researchers also performed a survey of the available technologies related to haul truck health and safety. These technologies fell into the following categories: mine design, fleet management, driver assist, operator safety systems, and data analytics. The survey involved online searches, attendance at two trade shows (Elko Mine Expo, Society for Mining, Metallurgy & Exploration [SME] Annual Conference and Expo), discussions with four manufacturers (CAT, Komatsu, ASI, Hexagon), as well as a contract with an integration company and CXS expert (Sedna: Jonathan Keyes). In discussions with stakeholders, NIOSH researchers focused on four key areas: the market, technology specifics, safety, and future trends. Some of the specific questions included:
- What problems/features are your customers looking to you for solutions?
- What is your target market? (commodity, mine size, surface/underground?)
- How many current installations do you have?
- What are the biggest challenges to adoption of this technology by industry?
- What underlying technologies are you using? (new or adapted from other industries?)
- Do your solutions support competitor interoperability/open data?
- What testing and validations have been done on the overall solution and subsystems?
- What specific safety issue(s) does your technology address?
- What research gaps do you see related to haul truck health and safety?
- What can NIOSH do to help advance the technology in this area?
- What are your current R&D tasks related to haul truck health and safety?
Fatal Accident Analysis
NIOSH researchers worked in collaboration with a human factors expert (Dr. Robin Burgess-Limerick) to review MSHA’s final fatal accident Report of Investigations for 91 haul-truck-related fatal accidents that occurred in the U.S. from 2005 to 2018. Throughout this report, this context of NIOSH’s analysis of the haul-truck-related fatal accidents will be referenced, with the percentages cited based on the 91 accidents studied.
In studying these accidents, researchers first reviewed the mine demographics, then constructed bow-tie representations of each event based on MSHA’s final fatal accident reports. The analyses focus on the initiating event, event outcome, hazards present, and possible preventative and mitigative controls. In order to translate the results, researchers then categorized the hazards (control failures) and preventative and mitigative controls according to the EMESRT nine-level defensive control model [37]. Researchers analyzed the results to answer the following questions:
- What mines are these accidents occurring at?
- What types of accidents are occurring?
- How are accident types changing over time?
- What are the possible causes of these accidents?
- What controls could have prevented or mitigated these accidents?
- How do these controls vary over the different accident types?
Most of the accidents resulted in a vehicle-environmental interaction (54%), where the haul truck collided with an environmental hazard (e.g., drove off highwall). This was followed by vehicle-person (15%), person-vehicle-environment (11%), and vehicle-vehicle (9%) interactions. Loss of control was the most common initiating event (36%), followed by equipment malfunction (22%) and loss of situational awareness (18%). This resulted in 61% of the accidents being initiated by the operator (i.e., loss of control, situational awareness, loss of balance) [44]. Furthermore, the initiating event types tended to result in different outcomes. Vehicle-environment interactions were mostly initiated by loss of control, while vehicle-vehicle interactions were predominantly initiated by loss of situational awareness [44]. These findings are consistent with other NIOSH analyses [20]. The results of this study highlight the need to re-focus the mining industry’s attention on effective low-level defensive controls (EMESRT’s levels 1-6). These include improvements in the implementation of low-level defensive controls that may have averted many of the accidents in this study and are believed to be the most effective.
Future Tasks
In addition to the methods described above, NIOSH researchers are further exploring operator decision-making, organizational preparedness, and technology maturity through two additional tasks: operator and management interviews and technology readiness assessments. These issues were identified through the preceding tasks by way of differing expectations, lack of communication across workgroups, and insufficient controls. The results of the work will be integrated into this roadmap once completed at the end of fiscal year (FY) 2021.
Operator and Management Interviews
NIOSH researchers are using the critical decision method [45] and a more generic cognitive task analysis method [46] to interview haul truck operators and managers from various workgroups at several mine sites. These interviews will be focused on near-miss and serious accidents stemming from violations of policies and procedures. This focus was selected because a NIOSH analysis of haul-truck-related fatalities [44] showed that Level 3: Operating Procedures and Level 6: Operating Compliance were the most frequently identified hazard/control failures in the EMESRT nine-level defensive control model. Researchers aim to better understand how well policies and procedures apply to these non-routine situations and to understand what motivates operators to make choices that lead to these violations. This work will help to identify the current gaps in low-level controls (e.g., EMESRT levels 1-6) and possibly identify solutions or areas for improvement.
Technology Readiness Assessments
NIOSH researchers are performing technology readiness assessments on selected technologies in four basic areas: semi/autonomous haulage, fleet management, driver assist (e.g., CXS), and fitness for duty. These were identified as critical areas from the analysis of the fatal accident reports. Researchers will use this maturity evaluation framework to generate user requirements as well as to identify areas where more testing or development is necessary. This work will also help purchasers better understand what to consider when investing in technology and help manufacturers to direct their research and development work.
Other Efforts
In addition to the tasks included in this project, NIOSH researchers are also currently developing project proposals to begin in FY21 and beyond, updating ongoing projects, and working on organizational initiatives to address the action items identified in the report. This work is described in the Current Efforts section later in this report.
Gaps
Why do haul-truck-related fatal accidents continue to occur?
Work on health and safety issues related to haul trucks has been taking place for many decades. As long as the mining process involves mobile machines interacting to move material, there will be exposure and risk. However, much of this risk can be mitigated or avoided with an effective risk management plan. Despite continual advances in ideology, technology, and performance, accidents and injuries still occur. Based on the methods outlined above, NIOSH believes that the root of the problem lies in incomplete development, implementation, and integration of health and safety interventions across the mining system. NIOSH identified 12 key areas across four system levels where significant gaps exist. For each of the key areas listed in Table 4, gaps include future research, development, communication, and implementation. The gaps will be further expanded with examples and action items in each section that follows.
Table 4. Haul Truck Health and Safety System Gaps by System Level
External | Organizational | Workers | Environment and Technology |
---|---|---|---|
Regulation | Policies and Procedures | Human-Centered Design | Infrastructure |
Standards and Guidelines | Communication | Situational Awareness | Interoperability |
Industry Forum | Workforce | Trust | Analytics |
External
Industry-wide forces that influence the adoption of health and safety interventions
The U.S. mining industry has a long history of government regulation and oversight. Much of the regulation in the U.S. is highly prescriptive but can also be subjective, resulting in a complex, highly regulated environment. Mining regulation is also complex because different aspects of the mining process fall under different jurisdictions that sometimes do not align with each other. As one example, sites that are governed by both MSHA and the Occupational Safety and Health Administration (OSHA) must follow two different rules regarding fall protection. MSHA requires that workers must wear fall protection wherever there is a risk of falling (30 CFR § 56.15005), while OSHA mandates fall protection for construction workers working at a height of six feet or greater (29 CFR §1926.501). Furthermore, complexities are introduced as rules at the state and federal levels change over time. This can be when the regulation itself changes or when the way it is interpreted changes. However, regulation typically changes too slowly from a technological readiness standpoint, with new technologies outpacing regulation. This is especially true for haul-truck-related health and safety issues with the emergence of automation and other new technologies.
Outside of regulation, haul truck health and safety has also been repeatedly identified as a priority issue by MSHA. In 2010, MSHA specifically included seat belts and parking procedures in its “Rules to Live By” for fatality prevention. In 2012, MSHA included task training, ground stability, and the correction of hazardous conditions in the third installment of “Rules to Live By” [47]. Finally, in 2018, powered haulage was identified as an MSHA special initiative, with the agency focusing on seat belts, large vehicles striking smaller vehicles, and conveyor safety. As part of this initiative, MSHA posted a Request for Information (RFI) that is seeking more information about current and upcoming technologies including automated haul trucks and seat belts [48]. MSHA has also indicated that it plans to issue a proposed rule in the future [10].
Finally, the U.S. regulatory environment differs from that in other major mining countries such as Australia and the Republic of South Africa (RSA). Australia is more risk-based and collaborative [49], while the RSA is very prescriptive and regulatory-driven [50]. Many of the large mining companies and international equipment vendors that operate globally fall under all these jurisdictions. Therefore, these global corporations are working with international workgroups such as EMESRT and ICMM to establish global standards and guidelines. However, these workgroups tend to be Australian-focused and lacking a strong U.S. presence. This is likely the case because the mining industry is a key economic driver in Australia [51] and there is a lot of investment in these groups. Additionally, Australia is leading the way with respect to automation. Higher labor costs in Australia and the practice of fly-in fly-out to bring workers to remote mining districts have helped make the business case for remote and automated operations, where initiatives such as Rio Tinto’s Mine of the Future have led the industry in technological innovation [52].
Regulation
Health and safety regulations are intended to protect mineworkers by providing a minimum set of rules. However, as the industry has evolved, the body of regulations has expanded and oversight has increased, resulting in a highly regulated industry. Compliance with these regulations consumes a considerable amount of resources in most mining operations. As a result, much of the industry’s efforts focus on compliance rather than proactive health and safety actions to keep mineworkers safe, as evidenced by the significant amount of compliance-based communications supplied by MSHA [53] and NIOSH researchers’ discussions with stakeholders.
Gap Definition
Regulation. Instances where regulation does not align with the current state of the industry.
Examples
Powered Haulage Initiative. One of the concerns brought up by stakeholders was the possibility of powered haulage regulatory action. Many mine operators and manufacturers have expressed concerns that MSHA would mandate CXS on surface haulage. Stakeholders believe that both the technology and the operators are not ready to implement such a rule. Though MSHA has projected related rulemaking for the future [10], thus far there has been no indication of the scope or direction.
Automation Regulation. Automation is also a large stakeholder concern. Stakeholders that spoke with NIOSH researchers expressed concerns with over- and under-regulation in this area. Currently, MSHA is directing inspectors that rules related to autonomous equipment only apply if there is a specific hazard to a human worker [54]. While this may be an acceptable short-term approach to encourage operator experimentation, the industry has expressed interest in working with MSHA to produce more definitive guidelines. Furthermore, some mining companies are waiting to adopt new technologies, in part, because they are waiting to see how the technologies will be regulated and enforced. Unfortunately, the time lag between initial discussions and rulemaking may encompass several design cycles of automation systems, which could significantly change the direction of automation development.
NIOSH's Strength
Effective regulation should be developed through evidence-based approaches. NIOSH is uniquely positioned and has a long history of conducting scientific inquiry that informs the development of standards, best practices, and regulation. NIOSH also has a long history of working closely with MSHA to develop interventions in support of the health and safety of U.S. mineworkers. Accordingly, NIOSH should provide support across all levels of control and throughout the design cycle to ensure that intervention development aligns with regulation. The following is a specific action that NIOSH can take:
- Stakeholder Engagement: Mine Automation and Emerging Technologies Partnership. (Priority) Many mining companies have expressed interest in increased communication and contact with MSHA but are concerned about enforcement action. NIOSH could develop a partnership that creates an open forum to discuss technological advances, current research, and industry concerns. (Action Item 1)
Standards and Guidelines
Standards and guidelines help guide decision-makers while developing new processes or technologies. Standards provide measurable design requirements and guidelines provide areas of consideration that can help designers make high-level decisions. While standards and guidelines exist for many industries and disciplines, the mining industry typically lags in such development. Therefore, many manufacturers either are not aware that any standards exist or use related industry standards instead (e.g., construction, oil and gas, agriculture). Internationally and domestically, mining workgroups are collaborating to develop standards and guidelines that are industry-specific with regards to haul truck health and safety.
Gap Definition
Standards and Guidelines. Instances where there are insufficient or too many standards or guidelines.
Examples
ISO. The International Organization for Standardization (ISO) has many mining-specific standards that have been developed by different workgroups. The ISO has also published related industry standards such as intelligent transport systems for generic vehicles [55] and pedestrian CXS [56]. Specifically related to haul truck health and safety, there are several ongoing initiatives surrounding CXS [57] and seat belts [58]. These efforts have been primarily driven by EMESRT and are still under development. In addition, various industry groups have issued calls for support [59, 60]. While NIOSH is engaged with these groups, more resources are needed to appropriately and consistently ensure NIOSH representation.
Vehicle Interaction and Automation Guidelines. Many of the international mining groups also work to produce guidelines for the industry. As an example, one goal of EMESRT is to advance equipment design to improve operational safety and maintenance “beyond standards.” Most recently, EMESRT has developed a significant guidance document on vehicle interactions, “Vehicle Interaction System Performance Requirement 5A (PR-5A)” [37]. The Global Mining Guidelines Group (GMG) has also been actively producing guideline documents such as the “Guideline for the Implementation of Autonomous Systems” (April 2019) [61]. NIOSH has had limited input into the development of these guidelines.
NIOSH's Strength
NIOSH researchers have a wide variety of expertise in areas such as human factors and technology integration that may not be represented in these international groups. Furthermore, NIOSH researchers have a unique and broad understanding of the U.S. mining market including smaller operations and sectors such as stone, sand and gravel that are also under-represented or not represented. To ensure this experience and expertise are incorporated into standards and guideline documents, it is imperative that NIOSH provides input and support to all levels of controls and iterations of the design cycle. Namely, NIOSH can support the mining industry with the following specific action:
- Stakeholder Engagement: Standards Committees. NIOSH researchers should continue to play an active role in standards committees. In order to best facilitate collaboration and inclusion, this should include attending meetings in person. The time and resources for this activity should also be included in projects to ensure consistent organizational representation with a documented point of contact versus individual ad hoc participation. (Action Item 2)
Industry Forum
Industry forums are workgroups, associations, or societies that enable the sharing of information to advance the interests of their constituents. Numerous international workgroups serve the mining industry in this capacity and have done so for many years. Several of these groups have devoted significant efforts to haul truck health and safety and technology. As with standards development, the U.S. lacks significant participation in many of these key international forums.
Gap Definition
Industry Forum. Lack of a cohesive group, venue, or openness to facilitate sharing of information and exploration.
Examples
EMESRT. EMESRT is an industry engagement group between original equipment manufacturers (OEMs) and major mining companies. The group also engages other international workgroups with similar objectives. The goal of this endeavor is to advance equipment design to improve operational safety and maintenance “beyond standards.” While this group is open to international participation, its origins and principal participants are Australia-based. NIOSH has limited and inconsistent engagement with this group.
ICMM. ICMM is “an international organization dedicated to a safe, fair, and sustainable mining and metals industry.” This organization brings together 26 mining and metals companies and 35 regional and commodities associations. The ICMM works to strengthen environmental and social performance as well as to serve as a catalyst for change in order to enhance mining’s contribution to society [62]. The ICMM Risk Management workgroup and the ICMM Innovation for Cleaner Safer Vehicles workgroup work in close collaboration with EMESRT to develop vehicle interaction controls guidelines [63]. Currently, NIOSH has minimal engagement with these groups.
GMG. GMG has a broad mission to support “initiatives to align, advance and innovate the global mining industry” [64]. Paid memberships have three levels—leadership, collaborator, and general—where leadership members establish and govern the group’s activities. One of the group’s focus areas is on influencing global guidelines, protocols, and standards in which all members can participate. GMG is based in Canada and is a legal entity of the Canadian Institute of Mining, Metallurgy and Petroleum (CIM), with partnerships with professional societies in other countries, including SME in the U.S. NIOSH has moderate engagement with this group but this engagement lacks consistency and higher-level participation.
NIOSH's Strength
NIOSH researchers have experience and expertise in many aspects of mining health and safety that are recognized around the world. NIOSH also has strong connections with U.S. mine operators, regulatory agencies, and industry associations that gives the agency specialized insight into U.S. mining concerns, with some insight into global issues. A specific suggestion to foster additional global industry collaboration is as follows:
- Stakeholder Engagement: International Workgroups. NIOSH researchers should play a more active role in international workgroups. In order to best facilitate collaboration and inclusion, this should include attending meetings in person. This should also include regular attendance at monthly or quarterly calls where applicable. The time and resources for this activity should also be included in projects to ensure consistent organizational representation with a documented point of contact versus individual ad hoc participation. (Action Item 3)
Organizational
Organizational attributes of a mining company related to decision-making or policy and procedure creation that can affect the health and safety of workers
While operator error is often the most salient and immediate cause of an accident, to assume that only operators make mistakes would be very short-sighted. The Director General of the United Kingdom Health and Safety Executive is quoted as saying “human error is a major contributory cause in 90% of accidents of which 70% could have been prevented by management action” [65]. The mining industry has come a long way since that statement was made in 1989, but organizational gaps still exist.
Overall, there remains a lack of complete implementation and integration of health and safety management systems. To demonstrate, in an exploratory study, researchers found that the majority of day-to-day risk management activities identified by mine leaders were reactive as opposed to proactive, indicating that a systematic approach was not yet in place [66]. This lack of implementation is concerning because supervision and leadership are key elements to an effective organization. In fact, supervisor support has been linked to positive mineworker safety behaviors, especially when it is in the form of informational support [67].
Unfortunately, as in other industries, organizations in mining suffer from siloed departments that are segregated into specialized areas [68, 69]. This results in a breakdown in communication, which has the potential to cripple safety intervention implementation because all the areas are related. As an example, a camera system may be added to a haul truck by the safety department, but operations must run the rollout and maintenance must keep the system running. Similarly, a traffic control policy and procedure initiated by operations affects overall safety risk assessment and will need to be maintained, and ultimately the workers will need to be trained on the new rules. In short, communication is essential to an organization’s success.
However, communication is only one aspect of an organization’s culture. Culture is a complex and enduring attribute of an organization describing the fundamental values, norms, assumptions, and expectations that can be seen at least partially through safety management practices [70]. Good organizational culture has been shown to support technology integration [71]. However, with the rush of new technologies, mine operators sometimes neglect the low-level controls (EMESRT Levels 1-6) such as policies and procedures and training. For instance, in the vehicle interactions space, a push exists to add the latest CXS technologies, while in many cases basic traffic hierarchy and intersection design still does not meet current best practices [6]. Significant safety improvements could be realized by focusing on best practices for these low-level controls.
Another problem facing mining organizations is the segmentation of the workforce. In 2008, contractors were estimated to account for 30% of the mining workforce, and their proportion has been expanding since 1983 [72]. The increased use of contractors may be due to such factors as reduction in employment costs, reduction in mine operator risk, specialization (e.g., drill and blasting), and inflated worker productivity (i.e., contractors are not included in productivity calculations, resulting in inflated numbers). However, mine operators have less control over contractors in relation to what they do, how they operate, and the training and communication they receive.
Policies and Procedures
A large role of an organization is to establish policies and procedures. Policies and procedures are what an organization claims as being important [73]. Whether the organization is taking a bottom-up, top-down, or risk-based approach to safety, policies and procedures of a health and safety management system help to define and integrate safety into an organization [74, 38]. Unfortunately, these Level 3: Operating Procedures are often not formalized, are underdeveloped, are not communicated, or have limited employee buy-in. This is problematic, especially for sensitive issues (e.g., drug and alcohol policies), where employee acceptance is critical. For policies and procedures to be effective, they should be jointly developed by management and employees [75]. Currently, significant gaps also exist in understanding what policies and procedures are necessary as well as an application gap in what is enforced and practiced (e.g., seat belts). Policies and procedures should be reviewed at a systems level to ensure that they address and do not conflict with needs across the mining system.
Gap Definition
Policies and Procedures. Instances where policies and procedures are not appropriate, effective, or communicated.
Examples
Effectiveness. Stakeholders across the industry are concerned about the adequacy of company policies and procedures. Certain MSHA citations are phrased as a mine operator’s failure to ensure the organization has adequate policies and procedures in place to ensure compliance with a regulation. Furthermore, lack of or inadequate policies and procedures was identified in 53% (48 of 91) of the haul-truck-related fatal accidents studied by NIOSH researchers for this report. However, this is likely an underrepresentation in that it is unclear why in 76 of these 91 incidents, workers failed to follow one or more policies and procedures (e.g., seat belts, traffic control). Furthermore, all 91 incidents had at least one operational control failure (EMESRT levels 3-6). A greater effort to review and evaluate policies and procedures industry-wide is necessary.
Applicability and Consistency. In conjunction with the question of how well policies and procedures achieve their stated goal, they also must be reviewed for how well they align with the circumstances. Do they fit with the whole system? Are they applicable in all cases? NIOSH researchers identified numerous instances of poor alignment between policies and procedures and specific circumstances at mines. For example, one site had placed a stop sign at the bottom of a hill on a shared roadway (i.e., mixed heavy and light vehicles). Given the grade, it was not practical for loaded haul trucks to stop. Haul truck operators were given the instruction that the stop sign was not for them, but this was not indicated in any of the signage and was not the case elsewhere around the site. As further evidence of possible misalignment, 84% (76 of 91) of the fatal haul truck accidents reviewed by NIOSH researchers for this report had at least one instance of an operator not following a policy or procedure. While some of these incidents may truly be errors, it is unclear how many of these violations are due to inadequacy of policies and procedures.
Alignment and Consistency. In conjunction with the question of how well policies and procedures achieve their stated goal, they also must be reviewed for how well they align with the circumstances. Do they fit with the whole system? Are they applicable in all cases? NIOSH researchers identified numerous instances of poor alignment between policies and procedures and specific circumstances at mines. For example, one site had placed a stop sign at the bottom of a hill on a shared roadway (i.e., mixed heavy and light vehicles). Given the grade, it was not practical for loaded haul trucks to stop. Haul truck operators were given the instruction that the stop sign was not for them, but this was not indicated in any of the signage and was not the case elsewhere around the site. As further evidence of possible misalignment, 84% (76 of 91) of the fatal haul truck accidents reviewed by NIOSH researchers for this report had at least one instance of an operator not following a policy or procedure. While some of these incidents may truly be errors, it is unclear how many of these violations are due to inadequacy of policies and procedures.
Alignment and Integration. The key feature of a systems approach is to make sure that all aspects of the system fit and work together as a whole. Policies and procedures can fall short in this area as well, as in when one policy is at odds with another or a procedure is put in place that forces a violation in policy. Policies and procedures must be designed as a part of a health and safety management system in order to address active and latent failures [31]. The ICMM’s critical control method [38] begins to address this issue, but such holistic methods are not being widely used across the mining industry.
NIOSH's Strength
NIOSH possesses a wide range of expertise that could support work in policy and procedure development and implementation. Specifically, NIOSH has several experts in health and safety management systems that bring a holistic understanding of the process as well as subject matter experts that have task- and equipment-specific knowledge necessary to understand areas such as traffic control (e.g., roadway and equipment design). This work would involve NIOSH support throughout the entire design cycle but may be particularly focused on evaluation at the end of the design phase and during modification and retrofit. Based on the above concerns and strengths, a specific suggested action is as follows:
- Intervention Research: Traffic Controls Evaluation. Researchers would survey and evaluate traffic control policies and procedures in order to develop a data-driven best practices document. Researchers would specifically target all levels and areas of the organization to evaluate compatibility and compliance. (Action Item 4)
Communication
Communication is another key component of health and safety management systems. Along with policies, training, planning, control, and incentives, communication is a critical dimension necessary for an effective system that involves top-down, bottom-up, and lateral information flow to motivate and engage workers at all levels of the organization [76]. Unfortunately, organizational communication has been cited as a basic accident cause since at least the 1930s and has persisted [77]. Specifically, change management is a particularly difficult area of communication. Research estimates that somewhere between 28% and 93% of all change implementations fail. While some researchers claim that many of these estimates are inflated, change management failure is still a significant gap that has persisted for more than 50 years. Furthermore, these failures have been primarily attributed to a general lack of systems thinking [78].
Gap Definition
Communication. Instances where information or expectations are not transferred.
Examples
Change Management. Change management continues to be a concern across the mining industry. Many stakeholders have expressed concerns and uncertainty with the best way to update policies and procedures as well as implement new technologies [6]. Specifically, for new technologies, mine operators discussed concerns about lack of vendor support. This has led to problems of preventative and reactive maintenance. For example, mine personnel and OEM technicians may not be fully aware of the calibration routines for CXS (e.g., radar). Additionally, a lack of skilled technicians to service the equipment has led to an increase in downtime and the use of non-standard equipment. Medium and small mine operators also discussed the fact that limited capital resources mean that the rollout of new technology is often long and is drawn out over several years. During this transition time, operators are asked to run a mixed set of vehicles (e.g., different makes and models of haul trucks) which can pose a significant hazard in itself. Similarly, medium and small mine operators typically do not have the resources to devote to a complete change management plan, whereas large operations can contract with third-party consultants (e.g., Sedna) if they do not have the personnel or skill set in-house.
Interdepartmental Communication. Another concern observed by NIOSH researchers at mine sites was a lack of communication between departments. For example, maintenance workers failed to communicate with haul truck operators about when specific maintenance issues were addressed on the vehicles they were operating. Barriers to this communication included limited personnel, shift timing, lack of perceived value, and mismatches in expectations. This lack of communication was observed in many forms including verbal, written, monitoring, and reporting. As a result of the lack of communication, operators were over- or under-reporting issues on their pre-shift inspections and ignoring vehicle maintenance warnings. As these examples demonstrate, complacency and habituation pose a potentially substantial hazard. Lack of pre-shift inspections was also identified in 10 of the 91 fatal accidents reviewed by NIOSH researchers for this report, and failure to follow maintenance procedures (e.g., lock-out-tag-out) was identified in 14 of the 91 fatal accidents.
NIOSH's Strength
NIOSH is well positioned to investigate communication failures as it has significant expertise in organizational systems, cognitive psychology, and training. A holistic and multidisciplinary approach to this persistent problem has the potential to significantly impact the mining industry because these types of problems are so ubiquitous. Mining companies often do not have the resources or expertise to devote to these problems. Therefore, an evaluation of the business case and development of best practices could support medium and small businesses that may be at a comparative disadvantage. This work heavily focuses on implementation and integration as well as feedback within the human-centered design cycle. The following are two specific suggestions where NIOSH could provide support:
- Intervention Research: Change Management for the Implementation of New Technologies. (Priority) In an effort to develop and demonstrate best practices in change management, researchers should explore current guidance, develop an intervention, evaluate the intervention, and produce a recommendations document. This work would be best suited to explore long-term rollout including maintenance. CXS may provide a good proof of concept for this work assuming technology readiness. (Action Item 5)
- Intervention Research: Pre-shift Inspection and Maintenance Activity Relationship. Researchers should explore the relationships between pre-shift competency, monitoring, and reporting with actual maintenance activities. This work would also explore the following questions: How effective are current pre-shift inspections? What can be done to improve the action and prioritization of follow-up maintenance activities as a result of reported concerns? What can be done to ensure proper maintenance is completed? How can operator-maintenance communication be improved? What best practices can be learned from those operators that are doing this well? How are these issues different for contractors? (Action Item 6)
Workforce
Recruiting, maintaining, and developing the workforce is also a significant concern for mining organizations. These concerns are separate from those about the workers themselves, which also play a large role and will be discussed in a later section. Understanding how the workforce is built and structured is critical for organizational effectiveness and cultural health. Studies have shown that positive attitudes and beliefs drive organizational effectiveness [79]. Therefore, not surprisingly, organizational restructuring, such as converting employees to contractors, is believed to reduce trust and safety culture [80]. The increased use of contractors also reduces the mining organization’s level of control.
Another feature of the workforce that has potential for organizational impact is the division and location of workers. While studies of office workers have shown that remote workers have similar perceptions of organizational culture [81], it is unclear how this translates into a physical and hazardous mining environment with teleoperators or remote dispatch personnel. Further study is needed to understand how remote work is specifically impacted in the mining domain.
Gap Definition
Workforce. Aspects of the workforce composition that lead to gaps in communication, expectations, or inclusion.
Examples
Contractors. As the mining industry more heavily relies on contractors and contracting companies to supplement and support the workforce, there has been greater concern about how to deal with health and safety issues. Studies suggest that, in general, contractors have a lower commitment to safety and lower accident reporting rate [80]. This may be due to lower communication and less training. Stakeholders have expressed these same concerns to NIOSH researchers. Despite efforts to provide and mandate training, the perception of additional risk is still present. These beliefs are supported by the fatality data cited earlier in that 34 of the 91 fatal accidents specifically mention a contracting company. While it remains unclear if this is a causal factor, a focused analysis could yield further insight. More information is needed to fully understand this problem.
Remote Operation. Another concern brought up by stakeholders is remote operation. Several mine sites previously had, currently have, or are planning to have remote control centers for teleoperation and dispatch management. These operations would be located in more metropolitan areas that are significantly removed from the mine. Technological advances are making this possible in order to attract more qualified workers as well as improve the quality of life of current employees (e.g., less commute time, more shift overlap). However, it is unclear how this change would affect operator situational awareness and connection to the mine and other workers. Many positions at the mine site cannot (e.g., maintenance) or will not (e.g., not enough business case) be automated. Therefore, this divide is likely to continue to exist for the foreseeable future. A better understanding of the implications of these moves can help to improve remote operation designs and maintain and improve the safety of all workers, both on-site and off.
NIOSH's Strength
As a neutral, third-party observer, NIOSH is well-positioned to tackle the difficult and ubiquitous concerns around contractors and surveillance. NIOSH has had success in the past at assessing the mining population [82, 83] and would be able to leverage that statistical expertise here. NIOSH may also be able to help through the development or facilitation of contractor training. Based on the above concerns and strengths, below are some suggested specific actions NIOSH can take:
- Surveillance Research: Haul Truck Usage. As a basic exploration into the use and integration of haul trucks, NIOSH researchers should develop a method to survey and possibility track the use of haul trucks across the mining industry. There is currently a lack of baseline statistics on the number, type, size, etc., of haul trucks in use within the U.S. mining industry. This surveillance activity should also explore whether and how these operations involve remote control or dispatch centers. (Action Item 7)
- Surveillance Research: Contractor Population. In order to gain a better understanding of the use of contractors in the mining industry and whether they are used to perform specialized tasks, supplement full-time employment, or operate customer trucks entering a mine site, more information is needed. NIOSH researchers could potentially cooperate with traditional surveillance organizations (e.g., MSHA, BLS) to identify more robust ways to track and categorize this type of worker. (Action Item 8)
- Intervention Research: Contractor Training. NIOSH researchers should work to collate and disseminate existing materials and develop and evaluate training plans for mine operators to support contractors on their sites. This work would not only provide a proof of concept, but it would consider the best ways to facilitate organizational communication from the mine site and its effects on contractor behavior such as personal safety, risk assessment, and incident reporting. (Action Item 9)
Workers
Individual workers at a mine site that make decisions or take actions that can affect their own or the health and safety health of others
The heart of any mining operation is the people. Mineworkers are the ones making decisions and taking action to get things done. As with the other levels of the system, mineworkers overlap and intertwine with all parts of the system, responding to the standards and regulations, changing organizational processes, and driving technology. Individual factors, capabilities, and limitations modulate these effects. For instance, NIOSH researchers estimated that, in 2008, mineworkers on average were 43.3 years old with 12.9 years of mining experience [82]. However, as the mining industry overall continues to grow, analysts predict that there will be insufficient skilled labor to satisfy demand over the next 20 years. This will likely result in a workforce made up of very young and very senior workers [72]. As the senior workers begin to retire and the next generation enters the workforce, the mining industry will lose experience and knowledge before it can be replaced, and the type of workers will begin to shift as new emerging technologies make advances in implementation.
Other influences on worker shortages are related to the requirements of what could be termed the “mining lifestyle.” Currently, fewer qualified workers are willing to take on jobs with long hours and that are far away from any major metropolitan area. However, the workers that do come tend to be young and inexperienced. This can make it difficult to handle the mining lifestyle. Many mining towns run 24 hours a day to accommodate shift work. Plus, mining jobs typically pay well, giving these young workers a significant amount of disposable income that they are not used to. These challenges can lead to worker fatigue and recreational use of drugs and alcohol, often resulting in a high turnover rate [72].
Mining systems must be designed for and with the mineworkers in order to be effective. The mining industry began recognizing the importance of human factors in general in the 1960s [84]. Early work included targeting specific issues, such as training, lifting, and cab design. More recently, human factors have begun to be considered in the design process. Approaches such as human-centered design focus on the mineworkers, their actual tasks, and the context of the mine site to make products more usable with fewer compatibility issues and unintended consequences [85]. Understanding of the human factor and the mining system is imperative to the success of these methods, because context and interactions lead to emergent and embedded properties that could otherwise be missed without a holistic understanding [86]. However, human- and system-based approaches have not been widely adopted in the mining industry [85, 41].
Human-Centered Design
One of the most ubiquitous problems facing mineworkers is the lack of consideration of both the users and the system in the intervention design process. Examples include the continuous mining machine remote, which led to the unintended consequence of increased striking, crushing, and pinning accidents [87]; the continuous personal dust monitor being too large for mineworkers to sit down with [88]; and underground proximity detection systems that were so difficult to work around that mineworkers disabled them [24]. More work is needed to ensure that these types of considerations are being made with the development and implementation of health and safety interventions.
Gap Definition
Human-Centered Design. Human-machine-environment interactions where human-task mismatches exist.
Examples
Communication and Intent. It is important for humans working around autonomous vehicles, or any automated system, to be informed and understand what the automated system is currently doing and what the system will do next. Without some form of direct communication, accidents can occur. One such example occurred at BHP’s Jimblebar mine site in 2014. An autonomous haul truck was about to turn right at an unmarked intersection according to its programmed route and collided with a manned water truck whose operator was unaware of the haul truck’s route. The autonomous haul truck was not able to stop in time to avoid the collision. Though the water truck operator had the ability to monitor the autonomous haul truck’s path, the operator was not aware that it intended to turn and was not aware that the location where the accident occurred was an intersection [89]. A greater understanding of the mine site context (e.g., traffic controls in place) and what information mineworkers need to know (e.g., intent) could have prevented this accident.
Despite segregation efforts, it is highly unlikely that humans and autonomous systems will ever run in complete isolation. Human-centered design approaches can help eliminate and mitigate these problems before they lead to accidents.
Task Incompatibilities. Human-centered design methodologies can also help address capability limitations to avoid errors in fully manual truck operation. For example, based on an analysis by NIOSH researchers of the 91 haul-truck-related fatal accidents studied for this report—focusing on the initiating event, event outcome, hazards present, and possible preventative and mitigative controls—a large number of these accidents involved a failure to stop the vehicle despite there being some combination of brakes available to the operator [44]. Therefore, technically the vehicle was not out of compliance. Unfortunately, in a loss of control event, operators have limited time to correct or take evasive actions. The current design of haul trucks gives operators several options for braking to be able to more nimbly control the vehicle during normal operations. However, this is not practical in an emergency, as loss of control was the most common initiating event in the haul truck fatal accidents (33 of 91) studied by NIOSH researchers for this report. A better understanding of operators’ abilities to regain control may reveal design modifications that could mitigate this problem.
End User Implementation. Human-centered design also has the potential to aid in intervention implementation. One example is fatigue monitoring systems. As currently designed, most systems require a person to monitor the operators and intervene when necessary. However, it is critical to understand who this person should be and how they should communicate with the operators. Is it appropriate to confront or accuse an operator on an open channel where everyone can hear? What if something personal is contributing to the operator’s distraction? How will operators respond to this information (or accusation)? Also, on the monitoring end, how many operators can one person monitor? How quickly do those who are monitoring operators need to intervene from a safety standpoint? It is vitally important that designers and implementors understand their population and end goals in order to build a usable, reliable, accepted system. Another example is seat belts. Despite years of work, mineworkers continue to fail to wear seat belts. In at least 29 of the 91 fatal accidents, mineworkers did not wear their seat belt and, in 37 of the 91 accidents, a seat belt interlock may have reduced the severity of the accident. Why aren’t seat belts being used?
NIOSH's Strength
NIOSH is well suited to study questions related to human-centered design, having human factors and engineering expertise coupled with human-centered design researchers and experts. Furthermore, mining manufacturers often lack this skill set and have expressed interest in working with NIOSH researchers on such issues in the past. NIOSH also has a good track record of working directly with mine operators on the implementation side, which is critical to a successful holistic solution. As part of the human-centered design approach, NIOSH would aim to support intervention development throughout the entire product life cycle with an emphasis on early development. Given these strengths and industry concerns, the following are specific suggestions where NIOSH can support the mining industry:
- Intervention Research: Autonomous Haul Truck Intention Communication. How should autonomous vehicles communicate intent? What information do manned vehicles need to interact and work around autonomous vehicles? What is the best way to approach an autonomous vehicle? Overall, autonomous vehicle communication is unreliable at mines. NIOSH researchers should begin to explore this space and benchmark against the automotive industry as well. (Action Item 10)
- Intervention Research: Evaluation of Haul-Truck-Related Technical Solutions. NIOSH researchers should systematically evaluate tasks and technological solutions for human-machine interface mismatches. Currently, there is a lack of understanding as to what the gaps are and how they may be addressed. The Situation Awareness-Oriented Design process [46] is a good human-centered design approach that could facilitate this research. (Action Item 11)
Situational Awareness
Situational awareness has continually been identified as a key research area for the mining industry [13, 90]. As part of human-centered design, mineworkers must have the right information at the right time and know what to do with it. Not surprisingly, this is not a problem isolated to haul trucks. Researchers have identified issues across the mining industry [91, 90] as well as other industries [92]. All systems must work together so that mineworkers at all levels maintain the appropriate level of understanding in order to make good decisions and take the best action.
Gap Definition
Situational Awareness. Processes or interventions that limit or do not provide sufficient information or understanding.
Examples
Collision Warning Systems. From a controls perspective, it is better to inform than to warn. Information gives operators more time to assess the situation and dynamically respond, whereas automation is much better at performing narrow, repetitive actions more quickly than workers. Work has begun in exploring the design of systems predominantly at Level 8: Advisory Controls (warning) [93, 94]. However, the industry has expressed continued concerns about what should be included in Level 7: Operator Awareness CXS as well as the effect of false alarms [6]. Additionally, vehicle collisions accounted for nearly 25% of the haul-truck-related accidents studied by NIOSH researchers for this report.
Fleet Management. Situational awareness is a large concern for dispatch officers and other mineworkers interfacing with fleet management systems. Mine operators are currently asking these individuals to monitor several systems at once (e.g., operations, maintenance, fatigue management), and it is not always clear if they are receiving the right information in a timely fashion and in a format that they can process. Stakeholders that NIOSH researchers spoke to expressed their concerns about inflexible software that is hard to manage. Additionally, improved monitoring and reporting systems were identified as possible mitigating controls for over 48% of the haul-truck-related fatal accidents studied.
Illumination. Though lighting is not typically thought of as a surface mining problem, the reality is that many operations run both day and night. In fact, illumination was identified as an issue in over one-fourth of the haul-truck-related fatal accidents studied. Furthermore, operators also identified this as a concern, specifically with technology such as backup cameras that do not operate in low-light conditions. Illumination concerns can also be compounded by inclement weather and shift rotations, where operators are exposed to situations they are not experienced with or used to seeing. Under these stressors, an operator’s situational awareness can severely decrease.
NIOSH's Strength
Situational awareness is an area that NIOSH is well positioned to investigate. NIOSH has expertise in human factors, simulation, and illumination well beyond the general industry. Additionally, the immaturity of the mining industry in this area leaves significant room for improvement. Work related to situational awareness typically falls into the areas of understanding the needs and use of an intervention as well as testing and validation in the human-centered design process. Situational awareness work also applies to controls at all levels. Below are two suggested areas where NIOSH researchers could have a significant impact:
- Intervention Research: Haul Truck Driver Assist. Understanding how much information that operators should be provided by preventative driver assist technologies (e.g., collision warning, edge of roadway) is still unclear. While some research is ongoing elsewhere [93, 94], NIOSH has skills in simulation and laboratory facilities (e.g., the VISLab at the Pittsburgh site) that make it the ideal organization to explore what haul truck operators need to know about driver assist technologies. NIOSH researchers should explore different levels, timing, and presentations of environmental, machine, and operator information. (Action Item 12)
- Intervention Research: Haul Truck Illumination. As in previous work that has been done with the underground roof bolter, NIOSH researchers should explore what type of lighting could best enhance surface operations. The haul truck would be a potentially effective proof of concept for other mobile equipment. This work could also be enhanced by recent illumination software updates and NIOSH’s simulation expertise. (Action Item 13)
Trust
Trust is an abstract concept that has been defined by many researchers and in many domains. Across these definitions, trust has three common features: It is subjective, it is related to specific expectations, and it is influenced by system performance [95]. Mineworkers must have an appropriate level of trust related to haul trucks, as too much or too little can lead to misuse and disuse of safety critical systems [96]. Trust is an integration gap related to haul truck health and safety and the mining industry in general.
Gap Definition
Trust. Instances where lack of trust (e.g., between people, technology, organization) leads to increased risk.
Examples
Automation. Probably the most salient example of trust related to haul truck health and safety is automation and its interactions with non-automated equipment and systems. Mineworkers and mine operators have expressed concerns to NIOSH researchers about how well autonomous haul trucks perform and what their impact on the mining process will be. Though trust differs across individuals, it is also an organizational and cultural phenomenon [97]. Therefore, operators need to understand trust across the entire mining system, which is currently uncertain. Additionally, trust in automation also includes remote systems. Operators and workers on the ground have to appropriately trust these systems to avoid over- and under-reliance [96], because there have been instances in the mining industry where these systems have failed [13]. It is unclear how remote operation changes mineworkers’ trust and how the level of trust affects their behaviors.
Failure to Follow Policies and Procedures. Trust can also be a problem between people and groups. Operating a haul truck typically requires trust in fellow drivers as well as loader or shovel operators with whom the operator interacts on a regular basis. Haul truck operators have to trust in other vehicle operators’ ability to control their vehicles and to follow policies and procedures (e.g., traffic control). However, failure to follow a policy or procedure was the most frequently coded cause of the haul-truck-related fatal accidents studied, occurring in almost 85% of the fatal accidents. Is there an aspect of trust related to these incidents? Are mineworkers fully competent or is the problem in trusting the organization? What is the appropriate level of trust? The motivation behind the behaviors remains unclear and should be explored.
NIOSH's Strength
Again, NIOSH researchers have experience and expertise in exploring trust. Recently, researchers studied mineworkers’ trust of underground mobile proximity detection systems [95]. NIOSH researchers could support the industry by evaluating trust of various technologies and groups as part of ongoing and new research projects. This work aligns well with industry needs and uses assessments as well as implementation, training, and integration support as a part of the human-centered design process. Specifically, as NIOSH begins a new initiative in automation, the following action could be taken:
- Intervention Research: Trust in Emerging Technology. There is currently a large gap in the industry’s understanding of mineworkers’ trust in emerging technology. As a part of its human factors evaluation, NIOSH researchers should explore trust. This would include autonomous haul trucks as well as remote operation. (Action Item 14)
Environment and Technology
Conditions, systems, solutions, and interventions at a mine site that affect the health and safety of workers
The fundamental activity of mining is moving materials from one location to another. Central to this enterprise is mobile equipment and predominantly haul trucks. Integrating haul trucks into the system at the most basic level involves understanding how the mine is designed, how the equipment is designed and used, how the equipment is maintained, and how the equipment interfaces with other aspects of the system. As technology progresses, this level of the system becomes more complex. However, to be effective, solutions must be integrated with the higher system levels.
Mine planning and design begin long before the first shovel of dirt is excavated and continue beyond the life of the operation. The environmental conditions and geology at a site heavily dictate how the mine will look, operate, and change over time. However, these engineering decisions require a significant level of understanding of operations, maintenance, and monitoring that is not always communicated. NIOSH’s analysis of the haul-truck-related fatal accidents revealed that a significant number of incidents were related to environmental conditions (48%) (e.g., rain, snow, time of day), roadway and stockpile design (59%) (e.g., steep slope, sharp curve), and traffic controls (13%) (e.g., intersection, changing traffic patterns). Furthermore, these low-level controls such as Level 1: Site Requirements and Level 2: Segregation Controls are being emphasized across the industry as a critical base that is required before the application of any technology [6].
Though mining technology is often thought to lag behind that of consumer development, the mining industry is currently experiencing steady growth. Technologies such as autonomous vehicles and big data analytics are rapidly emerging [11]. However, based on mine site visits and discussion with vendors, these technologies seem to be typically only accessible to large mining operations and are not being well integrated into overall mining systems. Autonomous systems in the U.S. are being run in isolation, separate from the main operation; suffering from data communication challenges; and requiring highly tailored solutions. Additionally, the mining market is small and segmented, which further reduces its buying power. The U.S. mining market size in 2019, including oil and gas, is estimated at $569 billion dollars [98], which is still only one-fourth the size of the construction industry [99] in the United States. However, considering the international context, the top 40 global mining companies represent the vast majority of the market, with a market share of $683 billion dollars [100]. This top-heavy market can make it especially difficult for medium-sized and small mining companies because of the dynamic and highly variable environments. Small mines often do not have the capital to purchase the latest technology or the resources to implement the solutions. Therefore, mining companies can, in effect, end up being the research and development labs for the technology, as was demonstrated with underground mobile haulage proximity detection systems [71]. Similarly, sector segregation can also lead to decreased adoption and demand. Despite common high-level requirement similarities, environmental differences such as infrastructure design can limit transfer.
Infrastructure
As a part of the basic composition of a mine site, infrastructure is a critical example of an integration gap. Infrastructure components such as data and voice communication networks may be overlooked or taken for granted. However, these play a huge role in the operation and success of any intervention. Overall, in this area, more work needs to be done in terms of communication, development, and training.
Gap Definition
Infrastructure. Systems, networks, or installations where support, maintenance, or investment gaps exist.
Roadway Infrastructure. Roads are a vital part of the mining process, especially in operations that employ mobile haulage such as haul trucks. It is important that the roads are designed for their intended purpose, well maintained, and modified as conditions or situations dictate. Roadway hazards (e.g., slope, grade, width, condition) were identified in 57% (52 of 91) of the haul-truck-related fatal accidents studied by NIOSH researchers for this report. Mine operators and mineworkers also brought up this issue in situations where haulage routes or traffic patterns were changed before roadways were updated. For example, the delayed widening of a roadway forced an atypical one-way traffic pattern that not only increased exposure but changed communication and focus. Good roadway maintenance is also critically important for the health of the operators and the machines. Previous accident analyses have identified voids in the roadway as one of the top causes of injuries [19], and mechanical failures were present in 34% of the haul-truck-related fatal accidents studied.
Communication Infrastructure. Whether it is a wireless network for an autonomous fleet, radio communication for traffic control, or wired power usage reporting, a reliable communication network is critical to a safe mining operation. The use of haul trucks requires mobility, which in turn drives the need for wireless communications. Implementation of increasing levels of haul truck automation drives the need for ubiquitous (i.e., area) coverage and continuous (i.e., uninterrupted) wireless service. Unlike wired systems where the connection is either present or absent, wireless systems are probabilistic by nature and many factors affect their performance. While wireless system design is a well-developed field, the mining industry currently lacks understanding of the design considerations and the expertise to design and operate wireless systems. Therefore, the industry could benefit from an objective comparison of the relative performance, cost, complexity, and logistic support requirements of the competing wireless solutions (e.g., Wi-Fi and long-term evolution (LTE) systems).
Another concern related to wireless communication is reliability. The reliability of the wireless system is dependent on the reliability of all the components (i.e., wireless links, backhaul links, core network), the system redundancy, and how the various components of the system can fail. It is desirable that any component failures happen in a manner that does not result in injury or loss of life or property. To ensure this, the probability of such failure must be considered on a holistic systems basis. Methods to achieve this are defined in IEC 61511 “Functional safety—Safety instrumented systems for the process industry sector” and other standards. However, these principles have not been adapted for the mining industry.
Maintenance. As discussed above, maintenance of any system is critical for its continued use, especially with limited capital and resources. Maintenance was an issue in over one-third of the haul-truck-related fatal accidents studied by NIOSH researchers for this report, and maintenance was also an issue that many of the mineworkers and mine operators brought up during site visit discussions. Stakeholders suggested that most mines are constantly in a state of reactive maintenance and are understaffed. It was also brought up on several occasions that the upcoming workforce lacks a willingness “to get their hands dirty” and does not have the right skills or technical understanding of haul truck electronics. Stakeholders further indicated that the new technology is more complex and introduces new problems. This also compounds the maintenance problem by requiring workers to learn new skills or forcing the mine operators to contract out some maintenance tasks.
Maintenance can be particularly challenging for contractors. Depending on the work arrangement, they may not have the needed space or workers to maintain their vehicles. Over one-fourth of the haul-truck-related accidents specifically cited involvement of contractors. Many of these incidents involved trucks that were upwards of 20 or 30 years old, and the contractors lacked any maintenance plan or activity.
NIOSH's Strength
In the life cycle of technology and product development, it is essential that response and support be timely. Therefore, because of the length of a typical cycle for a NIOSH Mining Program project, NIOSH is best suited for concept development and implementation—i.e., the early stages of design, validation, implementation, and integration. NIOSH’s strengths lie in its rigor, attention to detail, and objectivity. NIOSH also has mining-specific expertise in ground control, communications and tracking, and training. Based on the identified issues and strengths above, the following actions are suggested:
- Basic/Etiologic and Educational Research: Surface Mine Wireless Communications Networks. (Priority) There is a lack of understanding within the mining industry of how reliable wireless networks are designed and the technology considerations for deploying such networks. Many resources are available to help educate engineers and design wireless networks, but these need to be identified and tailored for use in the mining industry [101]. Before mine sites invest heavily in infrastructure and interventions that are specific to communication protocol, the mining community needs informational resources relative to the pros and cons of the various choices. Specifically, the proliferation of Wi-Fi networks as a low-cost solution for automation in mining should be compared to other more scalable and reliable system choices. Research should look at design criteria used in other industries and adapt that to the mining industry based on differences in fade margins and other operational and site-specific factors that may require measurement and modelling. The results of the comparisons and research should be made available to the industry through webinars or tutorials or other expeditious dissemination methods. (Action Item 15)
- Capacity Building: Engineering Systems Thinking. (Priority) Most academic mining programs currently lack a systems view of the mining process. Most curricula are based on the basics of mine design. However, it is critical that students are better prepared to take a holistic view of their work. Mining engineering programs should include a systems approach that addresses mine design and its impact on other aspects of the mining process, such as equipment. For example, mining engineers need to understand the capabilities of the haulage equipment to ensure that roadways and other base infrastructure can be designed (e.g., grade, curve) and maintained appropriately (e.g., surface, width). As a part of this effort, programs should also include human factors considerations and methodologies such as human-centered design to help fill the other implementation gaps as well (Action Item 16)
- Intervention Research: Roadway and Stockpile Design. Despite many decades of knowledge and emphasis, mine sites continue to operate with unsafe roadways and stockpiles. Therefore, NIOSH should develop training materials to more effectively communicate best practices in this area. This training material would be designed to quickly and efficiently disseminate the combined ground control and equipment design expertise held at NIOSH. (Action Item 17)
Interoperability
As systems become more complex, integration and interconnectivity become more important to ensure that mineworkers receive vital information when and how they need it most. Furthermore, integration is critical to realizing the full benefit of any technology or intervention. In order to achieve this, interoperability is key.
Gap Definition
Interoperability. Systems, networks, or installations where communication and compatibility gaps exist.
Examples
Sensor Integration. CXS and and autonomous haul trucks are prime examples of interoperability gaps. OEMs typically do not share technical details about their products for various reasons, including competition, liability, and resources. However, this practice requires integrators or third-party developers to invest a significant amount of time and resources to reverse engineer equipment outputs and system dynamics [6]. It also introduces other potential points of failure, thus increasing mineworkers’ exposure and risk. Often, integrators choose to keep their systems separate, which can lead to a host of problems including the following:
- Operator overload. Too many screens, conflicting information, competing information.
- Poor integration. Poor cable routing (e.g., across engine compartment), inaccessibility, inaccuracies.
- Misuse/disuse. Lack of trust, lack of usability, redundancy.
Furthermore, systems that are not fully integrated are not able to reach their full benefit. For example, if a CXS is only installed as a vehicle intervention to prevent a collision, mines are missing the opportunity to track and visualize where, when, and why these events are occurring as well as lacking a monitoring system to track machine health and performance [6].
Data Reporting and Monitoring. Interoperability is also important to ensure that information gets used by the intended audience. To demonstrate, during one mine visit, NIOSH researchers learned that the mine had acquired equipment at different times, resulting in the maintenance reporting on the mine’s haul trucks occurring at different rates and using different communication networks (i.e., Wi-Fi and cellular). This inconsistency led to disuse of the system. Both from a purchasing and development standpoint, it is important that mines can unify such systems even if these items are purchased at different times or from different vendors. Legacy systems, mixed fleets, and delayed purchasing are mainstays at mines. Therefore, interoperability and data transfer remain critical gaps.
Data Sharing. Information use and interoperability does not stop between collection and reporting. Interoperability is also critical for higher-level analytics. Machine health information can be just as valuable for operations as it is for maintenance. For example, if Operations was able to track when and where a haul truck hit a pothole or where its wheels slipped, it could be better able to perform roadway maintenance, reducing risk through another preventative control. While there is nothing to stop this information from being communicated through administrative controls, software interoperability would help to reduce human error that can be introduced in the transcription or verbal communication process.
NIOSH's Strength
Interoperability is one of the more intangible integration gaps in the mining industry and is best understood through its implications. NIOSH’s strength in this area relates to the knowledge and scientific skill of its researchers. Researchers are able to use their in-depth subject-specific knowledge to systematically address high-level concerns, in that they can operationalize problems into manageable tasks with tangible outcomes. NIOSH is well positioned to help answer the overarching questions of what needs to be interoperable and to what extent through specific studies. These answers support the concept and design phases of human-centered design. Below are two specific actions that can be taken:
- Intervention Research: Control/Dispatch Operator Interface Design. (Priority) For dispatch operators, autonomous control operators, and haul truck operators, the following questions should be explored in relation to how their work areas should be designed: How much information can one-person monitor? What information should be displayed? Can an operator react rapidly enough to prevent accidents? (Action Item 18)
- Intervention Research: Collision Avoidance and Warning Systems Validation. In an effort to determine the effectiveness of system integration and the level of interoperability required and keeping in mind installation variability, NIOSH researchers should fundamentally characterize and test CXS and other third-party systems to answer the following question: How well do these systems actually perform? Validation would ideally involve real-world and simulation testing to take advantage of the simulation expertise of NIOSH researchers. (Action Item 19)
Analytics
Directly related to interoperability is analytics—i.e., what one does with the data. Analytics are often a gap because many solutions and interventions result in a “data dead end,” meaning nothing is done with the data beyond a superficial purpose, or the results of an intervention are not evaluated. Once again, benefits can be more fully realized with complete integration through an assessment cycle such as Plan-Do-Check-Act [102].
Gap Definition
Analytics. Systems, databases, or processes where gaps in processing, application, or consideration exist.
Examples
Performance Monitoring. Data dead ends often begin right at the intervention. Many safety interventions, such as CXS, are implemented to protect mineworkers, but the performance is not monitored or assessed. Simple analytics such as a heatmap of stopping incidence locations can help operators to understand and improve the overall mining system [6]. If mine operators review events across machines, they can help refine calibration improvements. If they review events by location, they can help identify mine design improvements. If they review events based on operators, they can help identify training needs. Monitoring and analytics provide added value to collision prevention systems by helping to prevent situations where collisions could occur before they happen. Analytics can help provide a more proactive approach to safety and health, identifying low-level controls (EMESRT levels 1-6) that can be put into place or improved.
Operations Data Review. Another typical data dead end is at the analytics themselves. Many mining safety systems provide aggregate information and trends, but the mine operator may not have the resources to review the information or nothing is done with it. For example, one of the critical issues discussed above is maintenance. Again, mechanical failures were identified in one-third of the haul-truck-related fatal accidents studied, and 22% of the accidents were initiated by mechanical failures. Many fleet management systems include features to send alerts to identify safety-critical leading indicators (e.g., brake pressure). However, many operations lack the personnel to review and act on this data, or the high volume of alerts may get relegated to email to be reviewed later and concerns do not get addressed until there is an actual incident or failure. Ensuring that the analytics volume and communication method fit the resources available at each site is vital to filling the analytics integration gap.
Big Data and Predictive Analytics. Beyond preventing a specific accident, analytics also offer the possibility of being more proactive through predictive analytics and the use of big data. The volume of information available needs to be aggregated, analyzed, and acted upon. As an example, many fleet management systems claim to provide predictive maintenance capabilities. However, these algorithms are still in their infancy and have the potential to be greatly improved. Based on the lack of use throughout the industry, even at large operations, there are still significant gains to be had from completing the assessment loop.
NIOSH's Strength
In support of assessment and evaluation, analytics are an opportunity for NIOSH to help close the integration gap. NIOSH’s expertise in surveillance and statistics lends itself to many logic-based approaches and data exploration. NIOSH researchers also have a strong background in analytics across numerous disciplines. This allows researchers to think beyond traditional methods and possibly discover new emergent trends. Furthermore, the organization is in the process of implementing a new data warehouse, which will increase NIOSH’s ability to handle and manipulate large data sets in a highly secure manner. Overall, this work fits best in the concept, integration, implementation, and feedback stages of human-centered design. Based on the identified issues and strengths, below are two specific actions that can be taken:
- Intervention Research: Data Visualization and Algorithm Design. NIOSH is well positioned to work with numerous manufacturers and organizations to collect a diverse set of data. As an exploratory study, researchers could combine and explore various data sets to determine answers to the following questions: What are the best ways to present this data? Are there any new health and safety insights? Can this data be combined or looked at in a different way to predict health and safety concerns? (Action Item 20)
- Intervention Research: Big Data Intervention Design. Mine operators are not fully aware of the benefits of big data analytics and how these systems could be integrated into organizations. NIOSH researchers could partner with a company to develop and implement an intervention as a proof of concept to answer the question: How can big data analytics improve the safety and health business case for mines? (Action Item 21)
Recommendations and Action Items
Summary
As evident in the breadth of material covered in this report, haul truck health and safety is a complex problem, and NIOSH researchers are currently working on the problem discovery phase. NIOSH is continuing to explore research gaps as well as taking specific action in support of the gaps that have already been identified. Table 5 is a combined list of action items that were primarily identified based on NIOSH researcher site visits and discussions with OEMs and industry experts during 2019, as well as an in-depth analysis of the haul truck related fatal accidents in the U.S. from 2005 to 2018. This list does not include all the gaps identified and is expected to grow through the second phase of this project. Researchers are actively engaging in research activities related to operator decision-making and organizational preparedness as well as technology maturity assessments related to haul truck health and safety.
The action items identified were selected based on NIOSH’s resources and strengths and alignment with the NIOSH Mining Program Strategic Plan [103], to be executed with and in support of additional industry action. Of the action items, researchers identified five priority action items listed in red as work that should be completed first in order to establish a line of research or items that require a long lead time to have an effect. The priority items are also items that the researchers believe should be specifically completed by NIOSH because of its unique position and current skill set. As an independent, government-funded research organization, NIOSH provides unbiased, credible science that considers the perspectives of all stakeholders. NIOSH also employs leading researchers across a wide variety of disciplines, which allows the organization to investigate these issues more deeply, systematically, and holistically. As a part of this overall effort, NIOSH believes that the non-priority items are also important and that NIOSH can and should play a role in addressing these items as well. However, it may not be critical that NIOSH leads these efforts. NIOSH plans to leverage ongoing and future work to identify collaborators and other stakeholders that may be able to help in filling these gaps. NIOSH also plans to reconsider these items as research plans are developed in future years.
Overall, the authors believe that many of the haul-truck-related health and safety concerns identified by this work stem from a lack of systematic development, implementation, and integration of health and safety interventions. A systems approach will be critical for addressing persistent health and safety concerns related to haul truck safety. Table 5 lists the identified action items across each system level and categories that were outlined in Table 1. Table 5 and the following section, Current Efforts, also summarize how NIOSH is currently addressing these issues as well as how it plans to in the future.
Table 5. Action Items - priority items in red bold
System Level | System Category | Action Item | Status | |
---|---|---|---|---|
1 | External | Regulation | Mine Automation and Emerging Technologies Partnership | Ongoing |
2 | External | Standards and Guidelines | Standards Committees | Ongoing |
3 | External | Industry Forum | International Workgroups | Ongoing |
4 | Organizational | Policies and Procedures | Traffic Controls Evaluation | |
5 | Organizational | Communication | Change Management for the Implementation of New Technologies | FY22 Concept |
6 | Organizational | Communication | Pre-shift Inspection and Maintenance Activity Relationship | |
7 | Organizational | Workforce | Haul Truck Usage | |
8 | Organizational | Workforce | Contractor Population | |
9 | Organizational | Workforce | Contractor Training | |
10 | Workers | Human-Centered Design | Autonomous Haul Truck Intention Communication | |
11 | Workers | Human-Centered Design | Evaluation of Haul-Truck-Related Technical Solutions | |
12 | Workers | Situational Awareness | Haul Truck Driver Assist | |
13 | Workers | Situational Awareness | Haul Truck Illumination | |
14 | Workers | Trust | Trust in Automation | |
15 | Environment and Technology | Infrastructure | Surface Mine Wireless Communications Networks | FY21 Pilot |
16 | Environment and Technology | Infrastructure | Engineering Systems Thinking | FY19+ Broad Agency Announcement (BAA) |
17 | Environment and Technology | Infrastructure | Roadway and Stockpile Design | |
18 | Environment and Technology | Interoperability | Control/Dispatch Operator Interface Design | FY22 Concept |
19 | Environment and Technology | Interoperability | Collision Avoidance and Warning Systems Validation | FY21 Project |
20 | Environment and Technology | Analytics | Data Visualization and Algorithm Design | FY20 Project |
21 | Environment and Technology | Analytics | Big Data and Intervention Design | FY20 Project |
Current Efforts
Given the identification of these research gaps related to haul truck health and safety, NIOSH plans to begin new efforts and has also identified current efforts that can support these issues. Table 5 lists the mapping to current NIOSH efforts for each action item, and the efforts are described in further detail below and depicted in the timeline in Table 6.
Mine Automation and Emerging Technologies Partnership (action item 1): As a part of a larger automation and emerging technologies initiative, NIOSH is organizing a Mine Automation and Emerging Technologies partnership. It is anticipated that the first meeting will be held in the fall of 2020. This effort aims to address the following objectives:
- Provide a forum for input on health and safety concerns, research gaps, technologically and economically feasible technical direction, and regulatory considerations
- Provide a forum for review, evaluation and discussion of specific technical and scientific questions
- Provide a forum for the exchange of the scientific findings and technology readiness
- Provide a forum for industry, manufacturers, academia, and others to present their research, system development, testing, and implementation activities and progress
It is NIOSH’s goal to use this partnership to bring together all stakeholders, including regulators, to help foster a joint understanding of the current issues and efforts.
Standards Committees and International Workgroups (action items 2 & 3): In order to better engage with the international community related to haul trucks and vehicle interaction in general, NIOSH researchers are more actively engaging with standards committees and international workgroups. Efforts have been taken to pursue a more active role with both EMESRT and ICMM. For example, NIOSH is currently developing additional content to be hosted on those organizations’ knowledge hubs in order to reach a broader audience for NIOSH’s work. Researchers are also interested in joining the ASTM International F45 standards committee that focuses on developing performance requirements for autonomous vehicles.
Change Management and Interface Design (action items 5 & 18): Following the completion of the ongoing research tasks related to haul truck operator decision-making and technology maturity, NIOSH plans to address some of the questions related to change management and interface design in an FY22 proposal. The specifics of this proposal are still under development, but NIOSH recognizes there is limited research in this area and a critical need for further investigation.
Surface Mine Wireless Communications Networks (action item 15): NIOSH plans to proceed with a pilot project entitled “Wireless Network Performance Requirements for Safety-Critical Systems in Mining – Pilot” to better understand wireless network requirements of safety critical systems such as autonomous haulage in FY21. The goal of this project is to determine relevant performance requirements (e.g., latency, radio link reliability, throughput) to ensure robustness of existing and emerging wireless network technologies as applied to safety-critical systems in the mining industry. Work from this project may inform wireless use and infrastructure development throughout the industry.
Engineering Systems Thinking (action item 16): By definition, system thinking involves more than just haul trucks. As is discussed in this report, there is a lack of systems thinking across all levels and categories from mine design and infrastructure to regulation. Therefore, NIOSH believes that all stakeholders could benefit from increased systems thinking in general. Research suggests that educational programs can be improved to incorporate systems thinking by educating their students how to think more about systems, developing students’ “situational leadership” abilities, and providing more temporal context of systems they are working with [104]. NIOSH is well positioned to begin promoting a systems thinking effort using its capacity building grants. In 2019, NIOSH posted a broad agency announcement (BAA) solicitation related to mining system design [105]. As an active collaborator with these awardees and reviewer of their progress, NIOSH can help encourage and support systems thinking related to these projects. Though the majority of funded programs are not directly related to haul truck health and safety they may have implications and unintended consequences related to haul trucks in the future. Plus, the effort begins to prepare the next generation workforce to employ systems thinking in their work. With NIOSH’s support, researchers and students can begin to think about their work in a systems context, where they can learn and practice these critical thinking skills that change how they approach a problem. For example, one funded project is related to digital technology development. A lack of systems thinking and perhaps interoperability could lead to compatibility problems in the future, just as has been identified with haul trucks in this report. These issues are not unique to mine design and therefore, NIOSH also plans to add systems thinking language to future BAA solicitations to support the development of future environment and technology solutions. Specifically, if funding allows, NIOSH plans to post a solicitation related to ground control capacity building in November of 2020.
Collision Avoidance and Warning Systems Validation (action item 19): To address collision avoidance and warning system validation, NIOSH is developing a three-year project to start in FY21 entitled “Validating Collision Warning and Avoidance System Detection Performance.” The aim of this project is to develop methods for evaluating CXS detection performance for surface mining haul trucks. The results are anticipated to provide the industry with guidance for validating CXS detection performance in support of preventing haul-truck-related accidents at surface mine operations. This work is directed at the environment and technology level of the system but will have consequences affecting all levels.
Big Data Visualization, Algorithms, and Interventions (action items 20 & 21): NIOSH is beginning to address some of the issues related to big data and analytics in the current five-year project (FY20 to FY24), “Validating Organizational Processes to Identify and Mitigate Risks,” which is focused on daily health and safety leading indicators such as near-miss incidents, risk assessments, employee perception surveys, and health and safety knowledge assessments. The objective of this research is to use the daily health and safety leading indicator data to identify trends and predict health and safety outcomes that subsequently can be operationalized and addressed within risk management interventions to prevent fatalities, injuries, and the onset of disease among miners. Researchers are working to provide daily content to a platform that is accessible to mine operators who are utilizing a specific mobile application. Those who are participating and have consented to share de-identified data with NIOSH have access to the content and ability to roll it out to their mineworkers daily. Researchers will then work to analyze the results in order to identify predictive trends for health and safety outcomes. As a subset of this data, researchers can specifically look at indicators related to haul truck health and safety to identify any trends. The second phase of the project will then be devoted to the development and evaluation of organizational interventions to address the critical indicators identified. This work aims to help make big data and analytics more tangible for mines across the industry. Though some organizations are beginning to use this technology, it has not yet been adopted throughout the industry in a practical way.
Table 6. Timeline of Current NIOSH Efforts
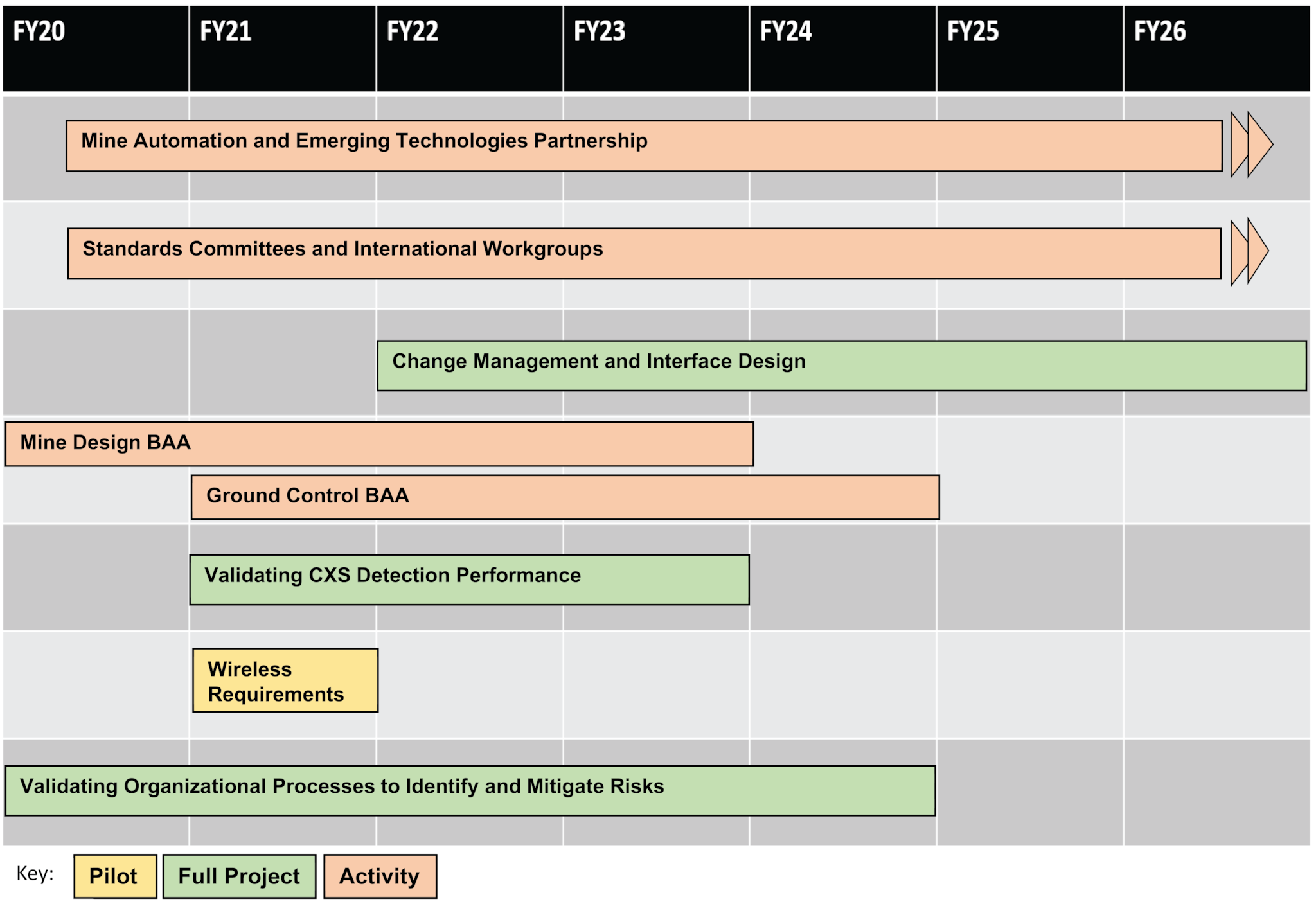
Conclusions
Haul truck health and safety continues to be a large concern in the mining industry. Despite efforts on many fronts to address this problem, haul-truck-related incidents still lead the fatal accident statistics in mining. With automation beginning to expand into the mining market, understanding the cause of these accidents is even more important. Therefore, the aim of this work is to identify and characterize health and safety issues related to haul trucks through a systematic evaluation of previous research, stakeholder needs, accidents and injuries, operators’ perspectives, and administrative and technological interventions.
As this work has progressed, it has become clear that there is a systemic lack of development, implementation, and integration of haul-truck-related safety and health interventions. For example, pre-shift examination policies are only effective if maintenance work is completed and communicated back to the operator to close the loop. Work is being done in isolation or at too low of a level to achieve full benefit. A systems approach that considers the interactive and interdependence of external and internal operational forces should be taken to fully integrate new and previously developed interventions throughout the entire mining system. NIOSH is well positioned to help address many of these concerns. NIOSH can offer the industry specialized research and, specifically, human factors support. The organization is best suited for concept development and implementation as well as supporting industry initiatives. This work spans all levels of the system and is not limited to only technology or equipment design. To this end, researchers have identified 21 action items that begin to address some of these gaps. However, this list is not exhaustive and will continue to grow as the project evolves.
Out of the 21 action items, researchers have identified five that they recommend NIOSH makes a priority and begins acting on:
- Stakeholder Engagement: Mine Automation and Emerging Technologies Partnership
(Action Item 1; External, Regulation) - Intervention Research: Change Management for the Implementation of New Technologies
(Action Item 5; Organization, Communication) - Basic/Etiologic and Educational Research: Surface Mine Wireless Communications Networks
(Action Item 15; Environment and Technology, Infrastructure) - Capacity Building: Engineering Systems Thinking
(Action Item 16; Environment and Technology, Infrastructure) - Intervention Research: Control/Dispatch Operator Interface Design
(Action Item 18; Environment and Technology, Interoperability)
Overall, NIOSH should continue to work with all stakeholders (industry, labor, academia, etc.) to help address their concerns and provide data-driven recommendations and solutions to mitigate haul truck health and safety issues.
References
|
- Acceleration and GPS Data Monitor Truck-Haulage Jolts
- Characteristics of Fugitive Dust Generated from Unpaved Mine Haulage Roads
- Comparison of Whole-Body Vibration Exposures on Older and Newer Haulage Trucks at an Aggregate Stone Quarry Operation
- Mining Haul Truck Cab Noise: An Evaluation of Three Acoustical Environments
- Mining Program Strategic Plan, 2019-2023
- Monitoring Blind Spots: A Major Concern for Haul Trucks
- Safety Analysis of Surface Haulage Accidents
- Surface Haulage Truck Research
- Technology News 468 - Tests of Doppler Radar Technology for Haulage Truck Backup Alarms
- Test Results of Collision Warning Systems for Surface Mining Dump Trucks
- Tying Acceleration and GPS Location Information Together To Create a Mine Management Tool