Mining Topic: Proximity Detection
What is the health and safety problem?
Mine workers perform tasks and control machinery in challenging conditions, often in close proximity to moving machines. At surface mines, large equipment often has limited visibility, making it difficult to see smaller vehicles and pedestrians. In underground mines, confined spaces, remote controlled equipment, and limited visibility due to dust, poor lighting, and the machinery itself make proximity a challenge.
A recent increase in accidents involving remote controlled continuous mining machines has brought this issue to the forefront for the NIOSH Mining Program.
What is the extent of the problem?
More than 40% of the most serious injuries (fatalities and permanent disabilities, 2000–2007) in the mining industry involve accidents classified as struck-by or caught-in machinery and powered haulage equipment. For surface mining, collisions and driving over an unseen edge contributed to 3 to 4 fatalities per year between 2000 and 2007. For underground coal mining, pinning and striking hazards involving continuous mining machines resulted in 37 fatalities since 1984. Striking and pinning accidents involving shuttle cars and scoops underground also resulted in 16 fatalities between 2000 and 2010.
MSHA has proposed new rules that would require proximity detection systems on continuous mining machines. Find out more at MSHA’s Proximity Detection/Collision Warning Single Source Page.
How is the NIOSH Mining program addressing this problem?
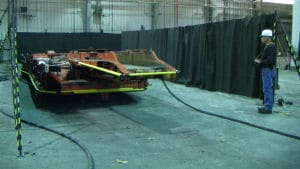
Researchers evaluate the Intelligent Proximity Detection system installed on a continuous mining machine in a simulated mine environment.
NIOSH has developed specific research goals for preventing injuries involving powered machinery, and proximity detection is currently the primary research focus in this area. Acting as an impartial third party, NIOSH has evaluated commercially available proximity detection systems for both underground and surface mining. Based on these findings, recommendations for testing and implementing systems have been introduced and improvements are being developed.
Surface mining: NIOSH developed new proximity detection systems through research partnerships, including radar-based technology and one of the first GPS-based systems for mining equipment.
Underground mining: NIOSH is developing a prototype intelligent proximity detection system that continuously monitors mine workers’ positions in relation to machines and established safety zones. Specific machine functions are disabled to prevent unsafe movement toward mine worker while allowing functions that do not put the worker at risk to remain operational.
What are the significant findings?
- After extensive field evaluations, NIOSH made recommendations for the evaluation and implementation of proximity detection systems in surface mines.
- NIOSH investigated the standing positions and visual attention locations for continuous mining machine operators, as well as safe operating speeds for mining machines.
- NIOSH has also developed sophisticated mathematical models of the magnetic fields used in proximity detection systems.
Based on these background studies, the Intelligent Proximity Detection (iPD) system was designed to provide situational protection based on the position of a mine worker relative to the machine. The iPD system has been shown to accurately track the position of mine worker and disable potentially hazardous machine motions.
What are the next steps?
NIOSH will focus on developing and testing of the iPD system to provide improved protection around continuous mining machines while minimizing false and nuisance alarms.
- An Active Proximity Warning System for Surface and Underground Mining Applications
- Effect of Operator Position on the Incidence of Continuous Mining Machine/Worker Collisions
- Engineering Considerations and Selection Criteria for Proximity Warning Systems for Mining Operations
- An Environmentally Robust Proximity Warning System for Hazardous Areas
- HASARD - An Electromagnetic-Based Proximity Warning System
- Innovative Safety Interventions: Feasibility of Using Intelligent Video for Machinery Applications
- Intelligent Proximity Detection to Improve Miner Safety
- Operating Speed Assessments of Underground Mining Equipment
- Proximity Detection With Selective Machine Shutdown
- Proximity Detection Zones: Designs to Prevent Fatalities Around Continuous Mining Machines
- Proximity Detection: A Continuing Research Imperative
- Recommendations for Evaluating & Implementing Proximity Warning Systems on Surface Mining Equipment
- Test Results of Collision Warning Systems for Surface Mining Dump Trucks
- Test Results of Collision Warning Systems on Off-Highway Dump Trucks: Phase 2