Injuries and Amputations Resulting from Work with Mechanical Power Presses
March 1987
DHHS (NIOSH) Publication Number 87-107
Current Intelligence Bulletin 49
Foreword
Current Intelligence Bulletins (CIB’s) are issued by the National Institute for Occupational Safety and Health (NIOSH), Centers for Disease Control, Atlanta, Georgia, to disseminate new scientific information about occupational hazards. A CIB may draw attention to a hazard previously unrecognized or may report new data suggesting that a known hazard is either more or less dangerous than was previously thought.
CIB’s are prepared by the staff of the Division of Standards Development and Technology Transfer, NIOSH (Robert A. Taft Laboratories, 4676 Columbia Parkway, Cincinnati , Ohio 45226). They are distributed to representatives of academia, industry, organized labor, public health agencies, and public interest groups as well as to Federal agencies, such as the Department of Labor, that have responsibilities for protecting the health and safety of workers. This CIB was prepared in conjunction with the staff of the Division of Safety Research, National Institute for Occupational Safety and Health, 944 Chestnut Ridge Road, Morgantown, West Virginia 26505. Our intention is for anyone with the need to know to have ready access to the information contained in these documents; we welcome suggestions concerning their content, style, and distribution.
Data from the Bureau of Census for 1980 show that there are about 151,000 mechanical press operators in the United States. Data from the Bureau of Labor Statistics (BLS) indicate that about 10% (2,000 per year) of all reported amputations (20,000 per year) occur among power press operators, including those who operate mechanical power presses. There are existing OSHA regulations (29 CFR 1910.217) governing the operation of mechanical power presses. However, data describing injury rates and operator hand speeds indicate that these existing regulations are not effective in providing adequate protection for all power press operators, especially young male operators. It is also important to note that there may be other reasons for these injuries, such as inadequate training of employers and workers.
NIOSH recommends that manufacturers of mechanical power presses disseminate the information in this CIB to their customers, and that employers make it available to their workers. NIOSH also recommends that professional and trade associations and unions inform their members of the potential hazards of mechanical power presses, and that appropriate engineering controls and work practices be used to minimize injuries to workers. Readers seeking more detailed information on the studies referenced in this bulletin are urged to consult the original publications.
This CIB describes how hand- or foot-activated power presses operate and how injuries occur during their operation. To help reduce the risk of injury among mechanical power press operators, this document also presents recommendations for safe operating practices that supplement those prescribed in the standards promulgated by the Occupational Safety and Health Administration (29 CFR 1910.217).
[signature]
Donald Millar, M.D., D.T.P.H. (Lond.)
Assistant Surgeon General
Director, National Institute for
Occupational Safety and Health
Centers for Disease Control
Abstract
In 1980, there were an estimated 151,000 operators of mechanical power presses. The existing standard promulgated by the Occupational Safety and Health Administration (OSHA) for mechanical power presses (29 CFR* 1910.217) provides requirements for press construction and operation. However, power press operators continue to be at risk of injury. Data from the Bureau of Labor Statistics (BLS) indicate that about 20,000 amputations occur each year. Between 1,600 and 2,000 (10%) of these amputations have occurred among power press operators. In addition, recent statistics compiled by OSHA indicate that approximately 49% of the injuries on mechanical power presses result in an amputation. Furthermore, National Institute for Occupational Safety and Health (NIOSH) research (based on injury frequency and severity data, operator hand speeds, compensation paid, and extent of worker exposure) indicated that young male operators appear to be at greater risk than other operators and mechanical power presses are the metalworking machines most in need of research to improve safety. NIOSH is therefore publishing this Current Intelligence Bulletin (CIB) with recommendations for the safe use of mechanical power presses, specifically those operated by foot or dual palm-button controls. Adherence to these recommendations should reduce the risk of injury among mechanical power press operators.
Background
Some amputations involving power presses occur when the operator places a hand into the working zone (or point of operation) of the press after the press operation is initiated. Most prevention activities involve the placement of guards to prevent operators from placing their hands into the working zone of the press. Guarding an industrial machine is an important safety action that should not be neglected. However, because the shape of the part to be stamped may require reaching near the hazard point, or because guarding alone is not always adequate, employers and manufacturers of presses should also examine how the press is controlled as a way of preventing amputations.
Basic Operating Principles of Mechanical Power Presses
There are three types of power presses: mechanical, hydraulic, and pneumatic. Their control systems may be mechanical or electro-mechanical. Though these three major types of power presses share some common features, the mechanical power press is the most commonly used and is the type of press on which the most research has been conducted. Therefore, this CIB is limited to mechanical power presses.
The two major components of a mechanical power press are a stationary bed and a moving ram. The press shears, punches, forms, or assembles metal or other material by cutting or shaping, using combination dies attached to the ram and bed. The mechanical power press operates on a reciprocating motion principle. The main components for power transmission are the clutch, flywheel, and crankshaft. A motor powers the rotation of the flywheel . A clutch is used to couple the spinning flywheel to the crankshaft. The crankshaft converts the rotary motion of the flywheel to the downward and upward motions of the press ram. A workpiece is fed into the lower die, either automatically or manually, and the machine cycle is initiated. On the downstroke, the ram (with an upper die) moves toward the work area, or point of operation (see Figure 1). When the upper and lower dies press together on the stock material, a re-formed piece is produced. Once the downstroke is completed, the newly formed workpiece can be removed, a new workpiece fed into the die, and the process repeated.
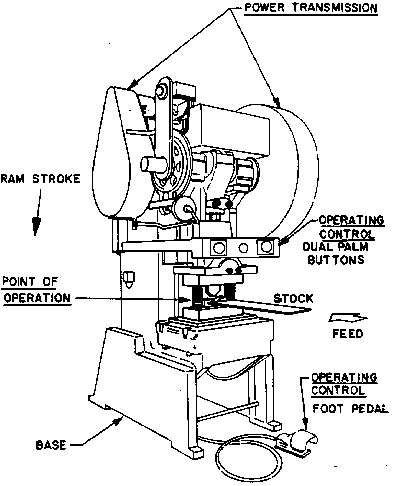
FIGURE 1. MECHANICAL POWER PRESS
Clutches
Two different types of clutches are used on mechanical power presses: full-revolution clutches and part-revolution clutches. There are important differences between these two types of clutches with respect to operator safety.
On presses with a full-revolution clutch, once the clutch is engaged, it remains engaged until the crankshaft has completed a full cycle. The part-revolution clutch differs in that it can be disengaged at any point in the downward cycle; thus stopping for safety reasons before the crankshaft completes the downstroke is possible. Since the full-revolution clutch makes a complete revolution before it disengages, presses equipped with this type of clutch generally pose a greater hazard after a stroke is initiated than presses equipped with a part-revolution clutch.
Foot and Hand Controls
Initiation of the power press stroke can be either automatic or manual. On presses that are manually operated, there are two popular modes for initiating machine motion: foot or dual palm-button (two-hand) controls (see Figures 2 and 3). With foot controls, the press is activated by pressing down on a foot switch or pedal, leaving the hands free during the cycling of the press. Foot controls do not intrinsically separate the operator’s hands from the machine’s point of operation during the operating cycle. Persons operating power presses with foot controls must be protected by safeguarding devices not always directly linked to machine operation. These safeguarding devices (e.g., barriers, gates, pullouts) may have interlocks capable of controlling initiation of the stroke. However, it also may be possible to operate the press with safeguards removed or modified so that they do not function as intended.
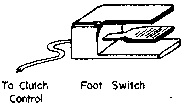
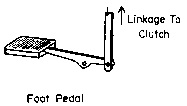
FIGURE 2. FOOT CONTROLS
With dual palm-button controls, once a workpiece is manually positioned in the press, both hands must be removed from the point of operation to depress the palm buttons. Dual palm buttons require both hands to be away from the point of operation when the press cycle is initiated.
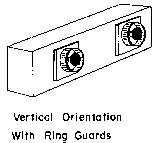
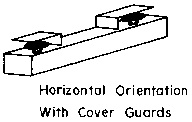
FIGURE 3. DUAL PALM-BUTTON CONTROLS
Operator productivity may be greater with foot switch operation than with dual palm-button operation since the hands are free during the entire period of the press cycle. However, this freedom of hand movement also places operators using foot switches at greater potential risk of sustaining a point-of-operation injury.
Standards
Existing OSHA Standards for Foot-Controlled Power Presses
The following is a summary of OSHA standards for mechanical power presses using foot controls (29 CFR 1910.217).
- OSHA 1910.217(b)(3)(i) – Manually-fed mechanical power presses shall incorporate a single-stroke (or anti-repeat) feature that allows the clutch to engage and the press to cycle only once each time the foot control is depressed.
- OSHA 1910.217(b)(4)(i) – A guard shall be used to protect the foot pedal against accidental operation from failing or moving objects or from another person accidentally stepping on the control.
- OSHA 1910.217(b)(4)(ii) – A pad with a nonslip contact area shall be firmly attached to the foot pedal.
- OSHA 1910.217(b)(4)(iii) – The pedal return spring(s) shall be of the compression type, operating on a rod or guided within a hole or tube, or designed to prevent interleaving of spring coils in the event of breakage. A double compression spring (one spring inside another with each spring wound in the opposite direction) is one way to meet this requirement.
Existing OSHA Standards for Dual Palm-Button Controlled Power Presses
The following is a summary of OSHA standards for mechanical power presses using dual palm-button controls (29 CFR 1910.217).
- OSHA 1910.217(b)(7)(v)(c) – Mechanical power presses shall incorporate a single-stroke (or anti-repeat) feature that allows the clutch to engage and the press to cycle only once each time the dual palm buttons are depressed.
- OSHA 1910.217(b)(7)(v)(a) – Dual palm buttons shall incorporate an anti-tie-down feature. This feature allows the buttons to be wired so that they must both be depressed and released for each cycle of the press. This eliminates the possibility that operators will “tie-down” one of the palm buttons, permitting the use of only one button to cycle the press.
- OSHA 1910.217(b)(7)(v)(a) – Both palm buttons shall have guards to prevent unintended operation and separation between buttons to prevent “bridging” of the palm buttons by operators–i.e., activating the press without using both hands.
- OSHA 1910.217(c)(3)(vii)(c) – To reduce the “after-reach” hazard, a minimum safety distance between the point of operation and the dual palm buttons shall be maintained on mechanical power presses based on the following formula:
Formula |
---|
D = 1.6 m/sec X T (sec), or |
D = 63 in./sec X T (sec) |
The safety distance, D, is the minimum safe distance between the point of operation and the palm button. The 1.6-m/sec (63-in./sec) value is a hand-speed constant that represents the typical speed at which workers can perform a hand movement toward the point of operation. The hazard time, T, represents the time required to eliminate the point-of-operation hazard on the press. On presses with part-revolution clutches, the hazard time is defined as the stopping time of the press ram. On presses with full-revolution clutches (1910.217(c)(3) (viii)), the hazard time is defined as the maximum possible time required for the ram to complete one downstroke.
- OSHA 1910.217(e)(1)(i) – The safety distance shall be maintained for each die used on the press; it should be checked periodically and at each new die set-up to ensure that operators are adequately protected. The most accurate method of measuring the hazard time on power presses equipped with part-revolution clutches is through the use of a stop-time meter. This device accurately measures the time that it takes the ram to stop after the palm buttons of a press have been released–i.e., after the stop signal has been initiated.
- OSHA 1910-217(e)(1)(ii) – On presses with part-revolution clutches, the clutch/brake mechanism shall be checked periodical ly for wear and adjustment. Dangerously worn or maladjusted brakes shall be replaced or repaired before further use of the press. Brake monitors, which are devices that monitor the stopping performance of the brake, shall be installed as required.
Hazards of Power Press Operation
Bureau of Labor Statistics (BLS) data indicate that of approximately 20,000 annual occupational amputations, between 1,600 and 2,000 (10%) occur among power press operators (McCaffrey 1981; BLS 1982). Injury statistics compiled by OSHA for the years 1975 through 1983 indicate that 49% of the injuries from mechanical power presses resulted in an amputation (OSHA 1975-1983). Of the 2,908 mechanical power press injuries reported to OSHA (OSHA 1975-1983), foot-controlled power presses were used in approximately 62% or 1,801 of the injuries, and hand-activated presses were used in approximately 30% or 876 of the injuries.
On poorly safeguarded presses, foot switches can be inadvertently activated while the workers’ hands are at the point of operation, resulting in an injury. A study conducted by NIOSH researchers (Trump and Etherton 1986) indicated that there is a critical cycling rate above which the frequency of inadvertent actuation errors increases dramatically as the cycling rate increases. For the simulated tasks in this study, this critical cycling rate was 17.5 strokes/min. These results indicated that jobs on foot-activated presses should be evaluated to identify their critical cycling rate, and steps should be taken to reduce the hazard of inadvertent actuation due to exceeding that critical cycling rate. Trump and Etherton concluded that at operational speeds in excess of a critical cycling rate “. . . operators performing repetitive tasks begin gradually to lose effective control over their foot movements.”
Trump and Etherton (1985) also concluded that two factors interact to cause inadvertent machine activation. First, “unmediated hand movements” are made in response to workpiece and machine problems. In other words, the operator may attempt to correct the placement of a workpiece after the downstroke of the press has been initiated. Second, out-of-sequence foot movements may be caused by loss of operator balance or by a breaking of the normal task rhythm.
Safeguards used on foot-controlled mechanical power presses include pullout and restraint devices. These consist of attachments to the wrists that pull the hands away from or hold them outside the danger point. Barrier guards or gates that prevent entry into the working zone of the press during the downstroke are also used. On presses equipped with part-revolution clutches, another safeguard used is the presence-sensing device. These devices initiate a stop signal if the effective sensing field is penetrated. The two most common types of presence-sensing devices are photoelectric and radiofrequency (capacitance).
The safety theory supporting the use of dual palm buttons can be defeated if operators are able to place their hands into the point of operation after the press cycle has been initiated–i.e., reach between the dies while they are closing. One way this may occur is when dual palm buttons are located so close to the machine dies that workers can place their hands into the working zone of the press before the ram has completed the downstroke. This type of movement is commonly called the after-reach hazard. NIOSH researchers have demonstrated that the physical location and orientation of dual palm buttons in relation to the point of operation as well as the operator’s hand speed have a significant effect on an operator’s ability to “after-reach” (Pizatella and Moll 1987; Horton et al. 1986). Present OSHA standards do not account for differences in hand speed as a result of palm-button location and orientation, and some press operators may be capable of attaining hand speeds in excess of the current OSHA hand-speed constant of 1.6 m/sec (63 in./sec) (Pizatella and Moll 1987). Table 1 lists the mean, standard deviations, and ranges of hand speeds of a sample of power press operators working on a press simulator controlled by dual palm buttons. The data in Table 1 were obtained at two palm-button locations: waist level and shoulder level, both with vertical orientation.
Several significant points are demonstrated by the data in Table 1 . The results of this study (analyzed by an analysis of variance procedure) generally indicate that as a group, male workers have faster hand speed than female workers (P<0.01). Also, based on Duncan’s Multiple Range Test, younger workers (under age 31) have faster hand speed than older workers (P<0.01). Further, 28% of all subjects, 40% of males and 12% of females, exceeded the OSHA standard of 1.6 m/sec (63 in./sec). Of males under 31, 79% exceeded the OSHA standard. The fastest hand speed measured was 3.6 m/sec (142 in./sec)–more than twice the hand speed specified in the OSHA standard. Finally, locating the palm buttons at shoulder level did not significantly alter the operator’s ability to exceed the 1.6-m/sec (63-in./sec) standard. Thus, based on these data, compliance with the current OSHA hand-speed standard may not be providing adequate protection for all power press operators.
Since this study identified young male press operators as having hand speeds faster than other press operators, an analysis of epidemiologic data should indicate that young male press operators have a larger amputation rate. To examine this possibility, NIOSH investigators undertook an analysis of injury data from State workers’ compensation agencies (Jensen and Sinkule, in press). Injury data from 29 states were used to compare amputation injury incidence rates (IR) for power press operators to identify any differences due to gender and age. While this analysis indicated that gender did not significantly affect the IR, there were differences in the IR based on age. The IR for young male press operators was compared to the IR of all other press operators. The IR for young male press operators was 1.91 cases/1,000 press operators while the IR for all other press operators was 1.58. Data from the state of Ohio were analyzed separately because of some recordkeeping differences. The Ohio data demonstrated a more dramatic difference in the IR among press operators. The IR for young male press operators in Ohio was 4.09 cases/1,000 press operators as compared to an IR of 1.41 for all other press operators. Although data analysis is not definitive in establishing that young male press operators are at a greater risk of injury, the differences in IR are in a direction consistent with the premise that young male press operators are not being adequately protected with present safeguarding mechanisms.
Table l. Mean after-reach hand speed (m/s)*
by palm-button location, gender, and age†
Gender and age | Waist-level location | Shoulder-level location | Combined | Range | |||||||
---|---|---|---|---|---|---|---|---|---|---|---|
Mean | SD§ | N** | Mean | SD | N | Mean | SD | N | Min. | Max. | |
Male: | |||||||||||
20-30 | 2.09 | 0.70 | 12 | 2.18 | 0.68 | 12 | 2.13 | 0.68 | 24 | 1.01 | 3.63 |
31-40 | 1.01 | 0.44 | 09 | 1.26 | 0.47 | 09 | 1.13 | 0.46 | 18 | 0.53 | 2.21 |
41-50 | 1.18 | 0.48 | 04 | 1.38 | 0.41 | 04 | 1.25 | 0.43 | 08 | 0.72 | 1.86 |
51-60 | 1.11 | 0.38 | 06 | 1.70 | 0.71 | 06 | 1.41 | 0.62 | 12 | 0.56 | 2.97 |
Total | 1.46 | 0.73 | 31 | 1.71 | 0.70 | 31 | 1.58 | 0.72 | 62 | 0.53 | 3.63 |
Female: | |||||||||||
20-30 | 1.13 | 0.63 | 07 | 1.07 | 0.27 | 07 | 1.10 | 0.46 | 14 | 0.38 | 2.15 |
31-40 | 1.23 | 0.35 | 04 | 1.48 | 0.37 | 04 | 1.36 | 0.36 | 08 | 0.81 | 1.86 |
41-50 | 1.07 | 0.74 | 10 | 1.23 | 0.62 | 10 | 1.15 | 0.67 | 20 | 0.49 | 3.06 |
51-60 | 0.66 | 0.20 | 08 | 0.97 | 0.30 | 08 | 0.81 | 0.30 | 16 | 0.48 | 1.41 |
Total | 0.99 | 0.57 | 29 | 1.16 | 0.45 | 29 | 1.07 | 0.52 | 58 | 0.48 | 3.06 |
Combined: | |||||||||||
20-30 | 1.73 | 0.81 | 19 | 1.77 | 0.78 | 19 | 1.75 | 0.78 | 38 | 0.38 | 3.63 |
31-4 | 1.08 | 0.41 | 13 | 1.32 | 0.44 | 13 | 1.20 | 0.44 | 26 | 0.53 | 2.21 |
41-5 | 1.08 | 0.66 | 14 | 1.27 | 0.56 | 14 | 1.18 | 0.60 | 28 | 0.49 | 3.06 |
51-6 | 0.85 | 0.36 | 14 | 1.28 | 0.62 | 14 | 1.07 | 0.54 | 28 | 0.48 | 2.97 |
Aggregate | 1.23 | 0.70 | 60 | 1.45 | 0.65 | 60 | 1.34 | 0.68 | 120 | 0.38 | 3.63 |
* To convert to in./sec, multiply meters by 39.37. [return to table]
† Adapted from Pizatella and Moll (1987). [return to table]
§ Standard deviation. [return to table]
** Number. [return to table]
Thus, to enhance the protection provided to all press operators, emphasis should be placed on ensuring the proper use of existing point-of-operation safeguards and the development of improved safeguards.
Based on these findings, NIOSH concludes that even though there are existing OSHA standards, a significant risk of injury to power press operators remains.
Operators are not always protected by the safeguarding provided because there are wide variations in hand speed among males, females, younger workers, and older workers. In addition to variations in hand speed there are several reasons why existing safeguarding may not provide the desired protection, such as:
- On machines that stamp differently shaped parts, each of which needs a different guard, it may take more time to install the proper safeguarding than it takes to run the job.
- Operators sometimes defeat the purpose of safeguards by removing or overriding them for convenience or increased productivity.
- Safeguarding is not always adjusted properly. This may be a problem with pullout and restraint devices if workers with different hand sizes and arm lengths work on consecutive shifts at the same machine. In some cases, dual palm buttons may be located too close to the point of operation because use of the existing hand-speed constant leads to erroneous placement of the palm buttons. Also, two-hand controls or presence-sensing devices may be improperly located after dies are changed.
Conclusions
Even though there is an existing OSHA standard that addresses construction and operation of mechanical power presses, injuries and amputations among press operators are still occurring with alarming frequency. In many cases, these injuries occur when the press is inadvertently activated while the operator’s hands are in the operating zone of the press. The results of a recent experiment conducted by NIOSH researchers indicate that the chance for inadvertent press activation (possibly involving injury) may increase as the cycling rate increases (Trump and Etherton 1986).
Injuries occur as a result of “after-reach” among operators who initiate power presses using dual palm buttons. Therefore, attention should be given to the individual operator’s hand speed, keeping in mind that, in general hand speed may be a function of age and gender.
Injuries may also occur as a result of deactivating or overriding safeguards. Under no circumstances should safeguards be deactivated or overridden.
The recommendations contained in this CIB are intended to address these problems and thereby reduce injuries among mechanical power press operators.
Recommendations
The recommendations presented below were compiled from generally accepted safety practices and research; they are intended to supplement existing OSHA standards. Implementation of these recommendations should be considered in any comprehensive safety program for the prevention of injuries among mechanical power press operators. We wish to emphasize that these data from NIOSH studies demonstrate that hand speed may be an inappropriate measure on which to base a safety distance standard for operation of mechanical power presses.
It may be impractical to implement a single hand-speed constant which would protect all workers under all power press set-ups. Implementation of such a hand-speed standard would render dual palm buttons practically useless as a safeguarding device due to the long safety distances which would result.
Additional information pertaining to the design of safeguards for mechanical power press safety can be found in OSHA 1980, ANSI 1982, and Wilco Inc. 1976 and 1976a.
Foot-Controlled Power Presses
- Foot controls should be used with point-of-operation safeguards that cannot be easily bypassed or misadjusted.
- Interlocking safeguards should be considered so that the foot control is inoperable when the safeguards are not functioning.
- An ergonomically correct, sitting work position, if possible, is preferred over a standing position if a foot control is used.
- To reduce strain on the foot, a foot-rest should be provided near the pedal.
- Riding the pedal (keeping the foot on the pedal without actually depressing it) is hazardous, and standard operating procedures should note this unacceptable work practice.
- The rate at which presses are being cycled should be monitored periodically to ensure that operators are not working at a pace that leads to inadvertent pressing of the foot pedal.
Power Presses Controlled with Dual Palm Buttons
- Because full-revolution clutches cannot be stopped once they are activated, they should only be used on presses with short downstrokes or fast cycling rates.
- To reduce musculoskeletal stress to the wrists, arms, and shoulders of press operators, ergonomic job design principles should be considered when locating and/or orienting dual palm buttons in relation to the point of operation.
- Caution must be exercised in evaluating each power press set-up and operation to ensure that an adequate safety distance is maintained at all times. Employers should consider evaluating individual press operators to determine if they are exceeding the current OSHA hand-speed constant. If a worker is identified as being capable of exceeding the hand-speed constant, more positive means of point-of-operation safeguarding should be considered, such as fixed barrier guards.
Recommended Checklists for Safe Operation of Mechanical Power Presses
The checklists presented below are provided as an adjunct to the above recommendations to aid in maintaining safe use of foot and dual palm-button controls for mechanical power presses.
Checklist to be used when foot controls are used:
- Safeguards are in place which will prevent injury if the foot control is inadvertently depressed.
- A guard or cover is over the foot switch to prevent activation by fallen objects.
- The working posture is as nonfatiguing as possible. Seating is provided where possible.
- Presence-sensing devices, if used, are properly maintained and aligned to ensure that the sensing field is effectively safeguarding the point of operation.
- Work rules have been established against riding the foot pedal.
- A check has been made to see if operators inadvertently push the foot switch because they are working at a high cycling rate with the foot control.
- The brake monitor, if required, is operative.
- The foot control must be depressed and released once before the press can be cycled again.
- Safeguarding devices and procedures are available for die set-up and maintenance to prevent or arrest an inadvertent downstroke of the ram.
- The press is routinely and frequently inspected and properly maintained.
Checklist to be used when dual palm buttons are used:
- The palm buttons are installed to meet at least the OSHA minimum safety distance requirements. Greater distances are recommended based on the operator’s true hand speed.
- The palm buttons are installed to reduce undue operator fatigue.
- The palm buttons are protected against unintended operation and are arranged so that the only probable means of operation is by both hands of a single worker, or by both hands of each operator where more than one operator is being protected by dual palm buttons.
- On presses with part-revolution clutches, the removal of a worker’s hand from any palm button during the downstroke of the ram quickly deactivates the clutch and applies the brake to stop ram motion.
- The brake monitor, if required, is operative.
- All palm buttons must be released before an interrupted stroke can be resumed or the press can be cycled again.
- The palm but tons are fixed in a position so that only a set-up person, supervisor, or safety engineer can move them.
- The position of the palm buttons is arranged to prevent any part of the body from entering the working zone of the press during the downstroke.
- The operation of the press is monitored frequently to ensure that operators are not bypassing or defeating the safety features of the dual palm buttons.
- Safeguarding devices and procedures are available for die set-up and maintenance to prevent or arrest an inadvertent downstroke of the ram.
- Presence-sensing devices, if used, are properly maintained and aligned to ensure that the sensing field is effectively safeguarding the point of operation.
- The press is routinely and frequently inspected and properly maintained.
Note
*Code of Federal Regulations. See CFR in references. [return to text]
References
- ANSI (1982). American national standard for machine tools–mechanical power presses–safety requirements for construction, care, and use. New York, NY: American National Standards Institute, Inc., ANSI B11.1.
- BLS (1982). Work-related hand injuries and upper extremity amputations. Washington, D.C.: Bureau of Labor Statistics, Bulletin 2160.
- Bureau of the Census (1984). 1980 census of the population: detailed population characteristics, Part 51, Table 217. Washington, D.C.: U.S. Department of Commerce.
- CFR (1986). Code of Federal regulations. Washington, DC.: U.S. Government Printing Office, Office of the Federal Register.
- DHEW (1975). Machine guarding – assessment of need. U.S. Department of Health, Education and Welfare, Public Health Service, Center for Disease Control, National Institute for Occupational Safety and Health, DHEW (NIOSH) Publication No. 75-173.
- Horton JT, Pizatelia TJ, Plummer RW (1986). The effect of palm button location on hand speed for power press operations. In: W. Karwowski, ed. Trends in ergonomics/human factors III. North Holland, Amsterdam: Elsevier Sci Pub B.V. Co., pp. 963-969.
- Jensen R, Sinkule E (in press). Press operator amputations: age and gender as risk factors. Journal of Safety Research.
- McCaffrey DP (1981). Work-related amputations by type and prevalence. Monthly Labor Review 3:35-41.
- OSHA (1975-1983). Unpublished report of injuries to mechanical power press operators. Washington, DC: U.S. Department of Labor, Occupational Safety and Health Administration, Office of Mechanical Engineering Safety Standards.
- OSHA (1980). Concepts and techniques of machine safeguarding. Washington, DC: U.S. Department of Labor, Occupational Safety and Health Administration, Office of Training and Education, Publication No. 3067.
- Pizatella TJ, Moll MB (1987). Simulation of the after-reach hazard on power presses using dual palm button actuation. Human Factors 29(l):13-22.
- Trump TR, Etherton JR (1985). Foreseeable errors in the use of foot controls on industrial machines. Applied Ergonomics 16(2):103-111.
- Trump TR, Etherton JR (1986). Machine-cycling errors with foot switches in repetitive tasks: a work station design simulation experiment. Applied Ergonomics 17(3):199-208.
- Wilco, Inc. (1976). Mechanical power press safety engineering guide. Springfield, VA: NIOSH contract report no. 210-75-0042, September 1976, National Technical Information Service, NTIS PB 80195340.
- Wilco, Inc. (1976a). Analysis of and design requirements for mechanical power press safeguarding systems. Springfield, VA: NIOSH contract report no. 210-75-0042, September 1976, National Technical Information Service, NTIS PB 86120557.