Mesures Techniques de Prévention: Guide de Bonnes Pratiques Prévention de l’exposition professionnelle à la silice cristalline alvéolaire lors du rabotage des enrobés routiers
Mars 2015
DHHS (NIOSH) Publication n° 2015–105
Recommandations pour la prévention de l’exposition aux poussières sur les raboteuses d’enrobés
Les présentes recommandations, applicables aux raboteuses d’enrobés d’un mètre de largeur ou plus, sont le fruit d’une collaboration entre syndicats, professionnels du secteur et institutions. Les constructeurs participants se sont associés au projet de recherche du Partenariat pour réduire les expositions à la silice cristalline alvéolaire et améliorer les conditions de travail dans la construction routière. Les recommandations ci-après sont issues de cette démarche collaborative ; on présentera d’abord les recommandations en matière de ventilation, puis les recommandations relatives à la suppression des poussières par pulvérisation d’eau.
Recommandations relatives à la ventilation sur les raboteuses d’enrobés
Le NIOSH recommande l’utilisation de systèmes de ventilation pour prévenir l’exposition professionnelle à la silice cristalline alvéolaire lors du rabotage d’enrobés routiers. Ces systèmes, associés à la pulvérisation d’eau mise en œuvre pour refroidir les dents de fraisage, permettent de ramener les expositions en deçà de la valeur limite d’exposition de 0,05 mg/m3 recommandée par le NIOSH (valeur REL [NIOSH 2013b,c]).
Les mesures de ventilation conçues pour réduire les expositions à la silice cristalline alvéolaire sur les raboteuses d’enrobés routiers doivent être évaluées dans un environnement contrôlé (atelier ou entrepôt), dans lequel leur efficacité peut être mesurée par des tests au fumigène ou au gaz traceur. Le test au fumigène doit être utilisé comme test qualitatif pour visualiser les schémas d’écoulement de l’air autour du carter du tambour et des convoyeurs de la raboteuse ; il constitue une aide à la préparation des tests au gaz traceur. Le test au gaz traceur doit être utilisé pour la mesure quantitative du débit d’air et de l’efficacité de captage du système de ventilation conçu pour limiter l’émission de silice cristalline alvéolaire dans la zone respiratoire des opérateurs. Les méthodes d’essai au gaz traceur et au fumigène permettant d’évaluer en laboratoire l’efficacité des mesures de ventilation sur les raboteuses d’enrobés sont présentées à l’Annexe A.
Lors de la conception des systèmes de ventilation sur les raboteuses, les principaux aspects à prendre en compte sont les suivants :
- degré d’encoffrement du tambour de fraisage et des convoyeurs
- conception du système de captage (hotte, conduits…)
- débit d’air requis
- robustesse et bruit du système de captage
- mesures de prévention du colmatage du système de captage
Le carter du tambour et les convoyeurs de la raboteuse doivent être conçus pour assurer un encoffrement maximal autour du tambour de fraisage et des bandes transporteuses. La conception idéale serait un tambour de fraisage et des convoyeurs encoffrés à 100%, avec une ouverture unique au sommet du convoyeur secondaire (au point de déversement de l’enrobé recyclé dans le camion benne).
L’élimination des ouvertures dans la conception de ces encoffrements contribue à maintenir la pression d’air négative nécessaire au confinement des poussières de silice. Les études réalisées par le Partenariat ont montré que si le carter du tambour et les convoyeurs sont bien encoffrés, la réduction de l’exposition professionnelle aux poussières n’exige qu’un débit d’extraction d’air de 900 acfm (actual cubic feet per minute, 1530 m3/h) dans la zone du convoyeur primaire et du carter du tambour. Une série d’études par gaz traceur ont permis d’établir l’efficacité de ce débit minimal de 900 acfm (1530 m3/h) [NIOSH 2011c ; 2012 ; 2013a].
Le maintien d’une pression d’air négative dans une enceinte close est une technique couramment utilisée, en ventilation, pour éviter qu’un contaminant ne s’échappe vers les zones environnantes. Pour confiner les poussières de silice, il est important de maintenir une pression d’air négative dans le carter du tambour de la raboteuse. Les nombreuses buses de pulvérisation d’eau au sein du carter du tambour peuvent créer une pression d’air positive dans le carter. En l’absence d’aspiration, l’air chargé de poussières peut s’échapper par les interstices du carter du tambour et polluer les zones voisines, en particulier la zone respiratoire des opérateurs proches de la raboteuse. La rotation du tambour et les enrobés en mouvement génèrent en outre des flux d’air qui peuvent transporter les poussières à l’extérieur. Il importe donc que la surface totale des ouvertures par lesquelles des fuites peuvent se produire depuis le carter du tambour soit aussi faible que possible, tout en restant compatible avec le processus. La ventilation doit extraire suffisamment d’air pour éviter toute pression positive, et établir une différence de pression négative entre le carter du tambour et l’air environnant. L’ouvrage Industrial Ventilation: A Manual of Recommended Practice for Design (Ventilation industrielle : recommandations de conception) préconise une pression différentielle négative de 1,0 ± 0,5 mm CE (10 Pa) comme critère de performance pour le confinement de la plupart des procédés industriels [ACGIH 2013b].
Les systèmes de ventilation conçus pour réduire les expositions aux poussières dans des locaux industriels ou sur un équipement se composent généralement d’une hotte, d’un ventilateur, d’un conduit et d’un collecteur de poussières [ACGIH 2013b]. Si le système de ventilation mis en œuvre sur une raboteuse ne comporte pas de collecteur de poussières, les poussières doivent être évacuées vers le haut à vitesse élevée, et la sortie doit être proche du sommet du convoyeur secondaire ou à un autre emplacement distant des opérateurs. Les raboteuses sans collecteur de poussières doivent en outre être conçues pour permettre à l’opérateur d’inactiver temporairement la ventilation quand l’engin progresse face au vent. Cependant, la ventilation doit être remise en marche automatiquement après un arrêt de plus de 60 minutes. Les systèmes de pulvérisation d’eau assurant le refroidissement des dents de fraisage doivent rester en service quelle que soit l’orientation du vent.
La ventilation doit être conçue pour une vitesse minimale de transport dans le conduit permettant d’éviter que les poussières ne se déposent et ne fassent obstacle à l’écoulement. La vitesse minimale recommandée par l’American Conference of Governmental Industrial Hygienists (ACGIH) est de 4 500 ft/min (23m/s) pour les poussières lourdes ou humides [ACGIH 2013b].
Une vitesse de transport appropriée dans le conduit peut ne pas suffire pour éviter le colmatage. Il importe également de prévoir une transition progressive des vitesses d’air entre le conduit et la sortie de la hotte, pour que des particules de grandes dimensions ne puissent pas pénétrer dans le conduit, le colmater ou endommager le ventilateur. Le ventilateur peut faire passer l’air extrait du carter du tambour ou du convoyeur primaire à travers une hotte ou une chambre d’abattage humide de telle sorte que la vitesse de l’air augmente progressivement en amont du conduit. La ventilation doit être conçue pour assurer au minimum la prévention de l’exposition aux particules de silice de taille alvéolaire. Il peut être prudent de prévoir également le captage des particules de poussière inhalables jusqu’à 100 µm de diamètre. Les particules de moins de 10 µm peuvent pénétrer dans la région des poumons où s’effectuent les échanges gazeux, et provoquer une silicose et un cancer [Plog 2002].
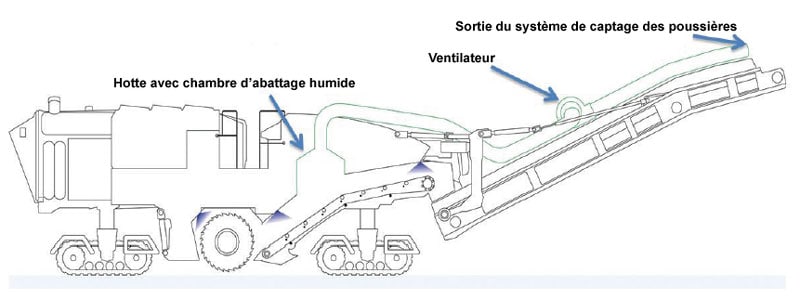
Figure 2. Hotte et chambre d’abattage humide sur une raboteuse (illustration NIOSH)
Les spécialistes des aérosols ont élaboré une feuille de calcul qui permet de calculer les vitesses de sédimentation en fonction de la taille des particules de poussières et de divers autres facteurs [Baron et Willeke 2001]. Les constructeurs de raboteuses doivent utiliser les informations sur la vitesse de sédimentation des particules pour concevoir un système assurant une transition progressive de la vitesse de l’air, qui évite la pénétration des particules de grandes dimensions dans le conduit. Il est notamment possible d’orienter une hotte ou une chambre d’abattage humide de telle sorte que l’air soit extrait à la verticale du carter du tambour ou du convoyeur. La figure 2 montre une chambre d’abattage humide carrée conçue pour recueillir les particules de plus grande taille grâce à une augmentation progressive de la vitesse de l’air, avant que les poussières ne pénètrent dans le conduit.
Même avec une chambre d’abattage humide ou une hotte assurant une transition progressive des vitesses d’air, le ventilateur et le conduit doivent être conçus pour supporter un flux d’air chargé de poussières. La robustesse du ventilateur et du conduit doit être évaluée pendant la phase de conception et d’essai du système de ventilation. Il convient de corriger tout défaut de robustesse du ventilateur et du conduit et tout problème de colmatage, avant d’équiper de série toute une flotte de raboteuses.
Recommandations relatives à la pulvérisation d’eau sur les raboteuses d’enrobés
Ces recommandations relatives aux bonnes pratiques en matière de suppression des poussières par pulvérisation d’eau sur les raboteuses d’enrobés s’appuient sur un travail de recherche intensif du Partenariat. Le NIOSH recommande d’utiliser les meilleures techniques disponibles (MTD) pour optimiser la pulvérisation d’eau sur les raboteuses d’enrobés qui ne comportent pas de système de ventilation. La pulvérisation d’eau constitue une méthode efficace et économique de lutte contre les poussières pour un grand nombre d’applications industrielles. Même si l’utilisation de pulvérisateurs d’eau est une technique très simple, il convient d’évaluer une série de facteurs pour identifier la conception la plus efficace dans le cas des raboteuses d’enrobés. La prévention et la suppression des poussières par pulvérisation d’eau sont deux démarches efficaces et facilement applicables lors du rabotage des enrobés routiers. Dans la démarche de prévention, l’eau est pulvérisée sur le revêtement en cours de rabotage afin de prévenir le dégagement/la formation et la mise en suspension des poussières. La suppression des poussières consiste à abattre les poussières présentes dans l’air en pulvérisant de l’eau sur le nuage de poussières et en induisant ainsi la collision, l’agglomération et la chute des particules présentes dans l’air. Une pratique courante et efficace consiste à associer ces deux procédés par voie humide, dans le cadre de la lutte contre les poussières. Toutes les raboteuses d’enrobés routiers étant équipées d’un système de refroidissement à l’eau des dents de fraisage, il est logique d’utiliser également cette eau pour prévenir l’exposition aux poussières alvéolaires.
La principale technique de prévention de l’empoussièrement consiste à humidifier le revêtement routier pendant le rabotage, ce qui augmente le poids des matériaux, des particules fines et des poussières. La mise en suspension des particules de poussière s’en trouve réduite, de même que leur transport par voie aérienne. Les éléments suivants sont déterminants pour une réduction efficace de l’empoussièrement par pulvérisation d’eau : (1) pression et débit d’eau, (2) arrosage approprié, (3) choix judicieux de l’emplacement et de l’orientation des buses, (4) contrôle de la taille des gouttelettes, (5) sélection du meilleur profil de pulvérisation et du meilleur type de buse, (6) maintenance appropriée des buses et de l’équipement de pulvérisation [NIOSH 2010]. Dans la mesure du possible, les réservoirs, pompes, conduites et buses du système de suppression des poussières doivent être fabriqués dans des matériaux anticorrosifs ou résistants à la corrosion. Il faut en outre disposer d’un système de filtration des liquides correctement conçu, en amont de la pulvérisation, afin de limiter la présence de contaminants dans le système et d’éviter le colmatage des buses de pulvérisation. Le document du NIOSH Best Practices for Dust Control in Metal/Nonmetal Mining (Bonnes pratiques de lutte contre l’empoussièrement dans l’extraction de minerais métalliques et non métalliques) fournit des informations plus précises sur la sélection des buses de pulvérisation et les réglages efficaces pour réduire l’empoussièrement sur des engins similaires, équipés de tambours de fraisage, utilisés dans les mines souterraines [NIOSH 2010].
Pendant la phase initiale de retrait du revêtement routier, il est primordial d’assurer une pulvérisation d’eau suffisante pour que les particules de poussière adhèrent aux matériaux retirés. Pour que le système soit efficace, la pulvérisation doit par ailleurs être uniforme. La réduction de l’empoussièrement peut être obtenue en pulvérisant de l’eau sur le matériau en cours de fraisage, ce qui a pour effet de mélanger mécaniquement le fraisat et l’eau et permet un mouillage uniforme [NIOSH 2011d]. La pulvérisation d’eau sert à la fois au refroidissement des dents du tambour de fraisage et à la suppression des poussières. La Figure 3 représente les buses de pulvérisation d’eau sur les dents d’un tambour de fraisage. Par souci d’économie d’eau, il est conseillé d’activer la pulvérisation uniquement lors du rabotage. Il est en outre recommandé d’installer sur chaque engin des débitmètres d’eau et des jauges de pression permettant de contrôler visuellement que le système de pulvérisation d’eau fonctionne dans la plage de valeurs prévue.
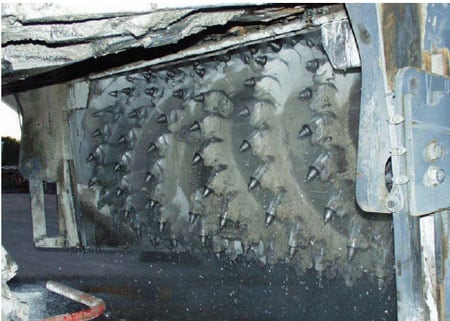
Figure 3. Refroidissement des dents par arrosage du tambour de fraisage. L’eau est ensuite mélangée au fraisat au fur et à mesure du rabotage (photographie NIOSH).
Application de la pulvérisation d’eau – Études de cas
En coopération avec la NAPA, les entreprises utilisatrices et les constructeurs, le NIOSH a évalué l’efficacité des modifications apportées aux systèmes de pulvérisation d’eau sur plusieurs chantiers lors du rabotage de revêtements routiers. Les niveaux de poussières alvéolaires ont été mesurés à plusieurs emplacements autour de la raboteuse, afin d’évaluer les émissions de poussières au niveau du carter de l’outil de fraisage et des zones de transfert du convoyeur primaire. Pour chaque étude de cas, les rapports techniques décrivent la méthode d’échantillonnage utilisée et les conditions spécifiques des tests sur chaque site. Les modifications apportées aux systèmes de pulvérisation d’eau n’ont pas toutes été bénéfiques, mais une réduction mesurable des dégagements de poussières a été obtenue dans bon nombre de configurations. Les études de cas résumées ci-dessous illustrent les modifications apportées et les bénéfices mesurés.
Étude de cas A
Le niveau initial de poussières sur la raboteuse a été déterminé avec le système de pulvérisation d’eau habituellement utilisé. Ce système comportait 18 pulvérisateurs à jet plat (buses) situés derrière le tambour de fraisage, cinq pulvérisateurs à jet plat à l’avant du tambour et plusieurs pulvérisateurs au point de transfert en sortie du convoyeur primaire. La pompe à eau sur la raboteuse était réglable jusqu’à un débit nominal maximal de 15 gallons par minute (gpm) (57 L par minute) à 200 psi (13,78 bar). Cependant, le débit couramment utilisé pendant le rabotage était de 6 gpm(23 L/min) à 35 psi (2,41 bar).
Des ajustements ont été effectués sur la pompe pour augmenter la pression de l’eau de 35 à 70 psi (4,8 bar) avec une augmentation correspondante du débit d’eau de 23 L/min à 45 L/min. La Figure 4 présente le débitmètre de type courant et la jauge de pression qui ont été installés et utilisés pour quantifier les changements apportés à la pulvérisation d’eau pendant les essais. Les mesures provenant de sept points d’échantillonnage des poussières autour de l’engin ont montré une réduction de 50 % des poussières alvéolaires (de 1 mg/m3 à 0,5 mg/m3 de moyenne géométrique), obtenue simplement en ajustant le réglage de la pompe à eau de 35 à 70 psi depuis le poste de commande de l’opérateur, sans aucun changement ni ajout au niveau des buses de pulvérisation existantes [NIOSH 2007a]. Les concentrations de silice cristalline alvéolaire dans les échantillons d’air prélevés dans la zone respiratoire des opérateurs se situaient entre des valeurs inférieures à la limite de détection et 0,170 mg/m3 pendant la durée du test [NIOSH 2007a].
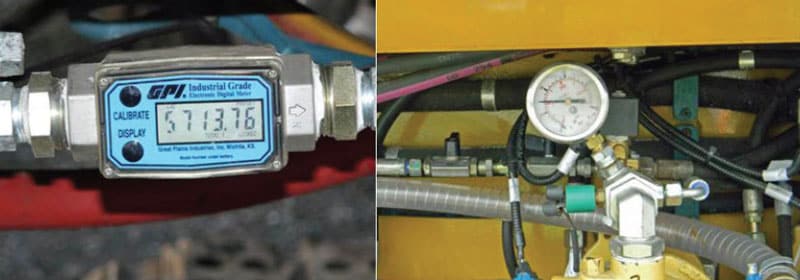
Figure 4. Débitmètre (à gauche) et jauge de pression (à droite) utilisés lors des études sur les engins de rabotage des revêtements (photo NIOSH)
Étude de cas B
Comme dans l’étude de cas A, le débit d’eau sur la raboteuse pouvait être ajusté par l’opérateur par simple modification du débit nominal de la pompe à eau. Dans cette étude, l’augmentation du débit d’eau de 47 L/min à 71 L/min a entraîné une réduction de près de 41% des poussières alvéolaires (de 0,328 mg/m3 à 0,193 mg/m3 de moyenne géométrique) sur 10 points de prélèvement clés autour de l’engin [NIOSH 2009b]. Là encore, ces réductions de poussières ont été obtenues sans apporter de changement au système de pulvérisation d’eau existant, hormis l’augmentation du débit nominal de la pompe à eau.
Étude de cas C
Dans cette étude de cas, le système de pulvérisation d’eau se composait initialement de 16 buses de pulvérisation d’eau au total, situées à l’avant et à l’arrière du carter de fraisage ainsi qu’en sortie du convoyeur primaire. Le débit total d’eau de ces buses était de 85 L/min à 1,38 bar. Dans le système de pulvérisation modifié, 14 buses au total ont été utilisées pour un débit de 81 L/min à 1,38 bar. Dans cette configuration, la quantité d’eau n’a pas augmenté, mais la répartition de l’eau a été modifiée, avec des changements d’emplacement et d’orientation des buses de pulvérisation, ce qui a amélioré l’efficacité du système. Ainsi, des buses ont été placées à l’avant du carter de fraisage pour évacuer l’eau à contre-courant du flux de matières, les pulvérisations en partie frontale haute du carter ont été supprimées et des pulvérisations ont été ajoutées dans la zone de transfert du convoyeur primaire. Les niveaux de poussières alvéolaires mesurés, après modification du système de pulvérisation, à six emplacements clés sur l’engin ont montré une réduction moyenne de l’empoussièrement de près de 43% (de 0,72 mg/m3 à 0,41 mg/m3 de moyenne géométrique) par rapport aux niveaux initiaux [NIOSH 2011d].
Le Partenariat a considéré que la configuration de l’étude de cas C était la plus efficace parmi celles qui ont été évaluées sur un nouvel engin de rabotage d’enrobés, et les schémas techniques correspondants sont présentés aux figures 5 à 7. Cependant, les constructeurs ont toute latitude pour améliorer encore les mesures de réduction de l’empoussièrement par pulvérisation d’eau, si les essais portant sur des solutions techniques nouvelles le justifient.
Études du tambour humide
Outre les différentes configurations des dispositifs de pulvérisation d’eau, le NIOSH et le Partenariat ont évalué la technologie dite « du tambour humide ». Cette méthode consiste à introduire l’eau à l’intérieur du tambour de fraisage et à utiliser la projection d’eau par gravité, à travers des buses, dans le carter du tambour pour prévenir l’émission de poussières dans la zone de fraisage. Les niveaux d’empoussièrement obtenus par cette technique ont été comparés à ceux générés par le système d’origine, composé de dispositifs de pulvérisation situés le long de la partie arrière du tambour de fraisage et dans les zones de transfert du convoyeur primaire et du convoyeur secondaire. La technologie du tambour humide a été évaluée sur deux chantiers de rabotage. Sur le premier, l’utilisation du tambour humide a entraîné une réduction de l’empoussièrement de 32% aux points de prélèvement les plus bas et de 59% au niveau de l’opérateur [NIOSH 2011c]. Sur le second site, les réductions moyennes étaient de 37% aux points d’échantillonnage les plus bas et de 27% au niveau de l’opérateur [NIOSH 2013d]. Cependant, la dispersion des résultats était telle sur le second site que les réductions n’étaient pas statistiquement significatives. Les concentrations de silice cristalline alvéolaire dans les échantillons d’air de la zone respiratoire des personnes exposées se situaient entre 0,028 mg/m3 et 0,085 mg/m3 sur le second site de test du tambour humide [NIOSH 2013d].
Un problème de répartition de l’eau sortant du tambour a été observé avec la technologie du tambour humide. Sur chaussée horizontale, l’eau s’évacuait du tambour de manière uniforme sur toute la largeur de rabotage, mais lorsque la chaussée était en dévers, l’eau s’évacuait du côté le plus bas du tambour de fraisage, tandis que la chaussée du côté haut du tambour restait sèche. L’ajout de déflecteurs à l’intérieur du tambour pourrait permettre d’améliorer les performances de la technologie du tambour humide en assurant une répartition uniforme de l’eau dans toutes les parties du tambour.