Mining Publication: Design and Analysis of a New Method to Test Mine Seals
Original creation date: October 2009
Authors: RK Zipf, KM Mohamed, GW McMahon
NIOSHTIC2 Number: 20037613
Proceedings of the 80th Shock and Vibration Symposium (DoD), San Diego, California, October 25-29, 2009. Virginia: The Shock & Vibration Information Analysis Center, 2009; :1-17
The final rule for mine seals issued in 2008 increased the seal design strength and specified new requirements for the engineering and construction of mine seals. New seal designs must resist a design pressure-time curve, remain elastic to withstand repeat overpressures, have adequate anchorage to the surrounding strata, and consider roof-to-floor convergence. Historic requirements for seal design only required a seal to survive a 20-psi test explosion at the National Institute for Occupational Safety and Health (NIOSH) Lake Lynn Experimental Mine (LLEM) without any visible structural damage and within certain leakage bounds. The explosion test methods used in the past to judge the adequacy of seal design did not consider many factors important for seal designs that meet the new standards. New seal testing is needed to consider: 1) Seal construction material 2) Foundation conditions 3) Hitching conditions 4) Roof-to-floor convergence Researchers designed and are building a seal test fixture for use in NIOSH's Mine Roof Simulator (MRS), which is a large biaxial loading frame capable of applying a vertical load up to 3,000,000 lb and a lateral load up to 1,600,000 lb. The fixture uses the vertical loading capability of the MRS to simulate roof-to-floor convergence and its shear loading capability to apply a load to the face of a seal test specimen, which is set in foundation blocks to simulate roof and floor conditions. The seal test fixture consists of two opposing triangular frames that apply a 4-point bending and shear load to the test seal face. NIOSH researchers performed simple analytic and finite element method analyses of each structural member and obtained excellent agreement. At maximum design load of 900,000 lb, the lowest safety factor is 1.15 which is acceptable for a testing fixture. The seal testing program will examine four factors above affecting seal performance. The seal test specimen permits four failure modes: (1) bending and tensile failure through the seal structure, (2) shear failure through the seal foundation, (3) shear failure along the seal-foundation interface, and (4) shear failure through the seal. Researchers from the U.S. Army Corps of Engineers (USACE) and NIOSH are working to create a new software version of the Wall Analysis Code specifically for Mine Seals (WAC-MS) for application to mine seal design and analysis. Successful completion of the testing matrix will provide validation data for the resistance functions in WAC-MS and for other numerical design tools used for mine seals.
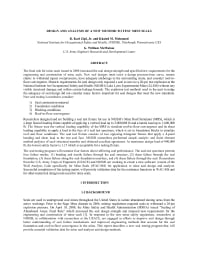
NIOSHTIC2 Number: 20037613
Proceedings of the 80th Shock and Vibration Symposium (DoD), San Diego, California, October 25-29, 2009. Virginia: The Shock & Vibration Information Analysis Center, 2009; :1-17
- Analysis of Multiple Seam Stability
- Application of Physical Modelling and Particle Flow Analysis to Evaluate Ore-pass Design
- Comparison of Methods: Dynamic Versus Hydrostatic Testing of Mine Ventilation Seals
- Determination of Sound Exposures (DOSES): Software Manual and Implementation Guide
- Explosion Pressure Design Criteria for New Seals in U.S. Coal Mines
- Explosion Prevention
- Progress Toward Improved Engineering of Seals and Sealed Areas of Coal Mines
- Strengthening an Existing 20-PSI Mine Seal with PPG's Polyurea Coated Retrofit
- Structural Analysis and Design of Seals for Coal Mine Safety
- Task Analysis
- Technology News 536 - NIOSH Develops New Software to Analyze and Reduce Noise Exposure