Mining Publication: Intelligent Monitoring System for Improved Worker Safety During Plant Operation and Maintenance
Original creation date: March 2019
Authors: D Parks, M McNinch, R Jacksha, H Nickerson, A Miller
Each year hundreds of mine workers are involved in machinery-related accidents. Many of these accidents involve inadequate or improper use of lockout/tagout (LOTO) procedures. To mitigate the occurrence of these accidents, new safety methods are needed. These methods should include the monitoring of access to hazardous areas around operating machinery, improving documentation/monitoring of maintenance activities which require shutdown of the machinery, and preventing of unexpected startup or movement during machine maintenance activities.
Of the hundreds of machinery-related accidents occurring every year in the mining industry, incidents involving stationary machinery at surface mines continue to be among the most frequent (MSHA, 2017). A U.S. National Institute for Occupational Safety and Health (NIOSH) study showed that the majority of fatal accidents involving stationary machinery at surface mines occurred at sand and gravel (38 percent) and stone (26 percent) operations. Of these accidents, entanglement in conveyor components were the most common cause of fatal accidents (48 percent) (Ruff et al., 2011). The same study stated that one-third of these accidents involved improper lockout/tagout (LOTO) procedures as a contributing factor. The U.S. Mine Safety and Health Administration (MSHA) acknowledged this problem, stating in a recent request for information (MSHA, 2018): “Since 2007, there have been 17 fatalities related to working near or around belt conveyors, of which 76 percent were related to miners becoming entangled in belt drives, belt rollers and discharge points. Factors that contribute to entanglement hazards include inadequate or missing guards, inadequate or an insufficient number of crossovers in strategic locations; and/or inappropriate lock out/tag out procedures. Systems that can sense a miner’s presence in hazardous locations; ensure that machine guards are properly secured in place; and/or ensure machines are properly locked out and tagged out during maintenance would reduce fatalities” (MSHA, 2018).
In response to this problem, NIOSH’s Spokane Mining Research Division (SMRD) is exploring the potential application of Internet of Things (IoT) technologies to provide cost-effective intelligent machine monitoring systems for improved worker safety (Zhou et al., 2017; Reyes et al., 2014). SMRD partnered with Central Pre-Mix CRH Co. (Central Pre-Mix) to develop and install a proof-of-concept wireless IoT solution to monitor machinery and conveyors during operation and maintenance. The primary goals of the system were to provide real-time monitoring of access points and facilitate the planning and execution of LOTO procedures.
This article describes the design and field deployment of this system. Field demonstration is a first step toward widespread adoption of intelligent safety monitoring systems and holds promise to reduce accidents related to machine guarding and improper implementation of LOTO procedures.
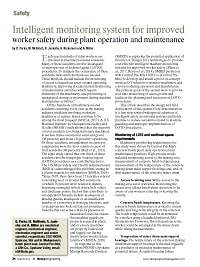
- Developing Random Virtual Human Motions and Risky Work Behaviors for Studying Anthropotechnical Systems
- A General Design and Implementation Procedure for Sensor-Based Electrical Diagnostic Systems for Mining Machinery
- A GPS Based System for Minimizing Jolts to Heavy Equipment Operators
- Intelligent Safety Technology for Mining Machinery
- Machine Injury Prediction by Simulation Using Human Models
- Motion Editing and Reuse Techniques and Their Role in Studying Events Between a Machine and its Operator
- NIOSH Engineer Chosen for Presidential Early Career Award
- Protecting Miners from Electrical Arcing Injury
- Sound Restoration Hearing Protection: Genesis of a Standard Test Method
- Verification and Validation of Roof Bolter Simulation Models for Studying Events Between a Machine and its Operator