Mining Topic: Manual Materials Handling
What is the health and safety problem?
Manual material handling (MMH) is the process of routinely moving and handling objects by carrying, holding, lifting, pulling, pushing, and stooping. MMH is performed by many types of workers in surface and underground mining including maintenance workers, electricians, mechanics, laborers, and some equipment operators. Workspace constraints, common in underground mining, and inadequate workstation design, in many plants and shops, contribute to injury risk for workers performing MMH tasks.
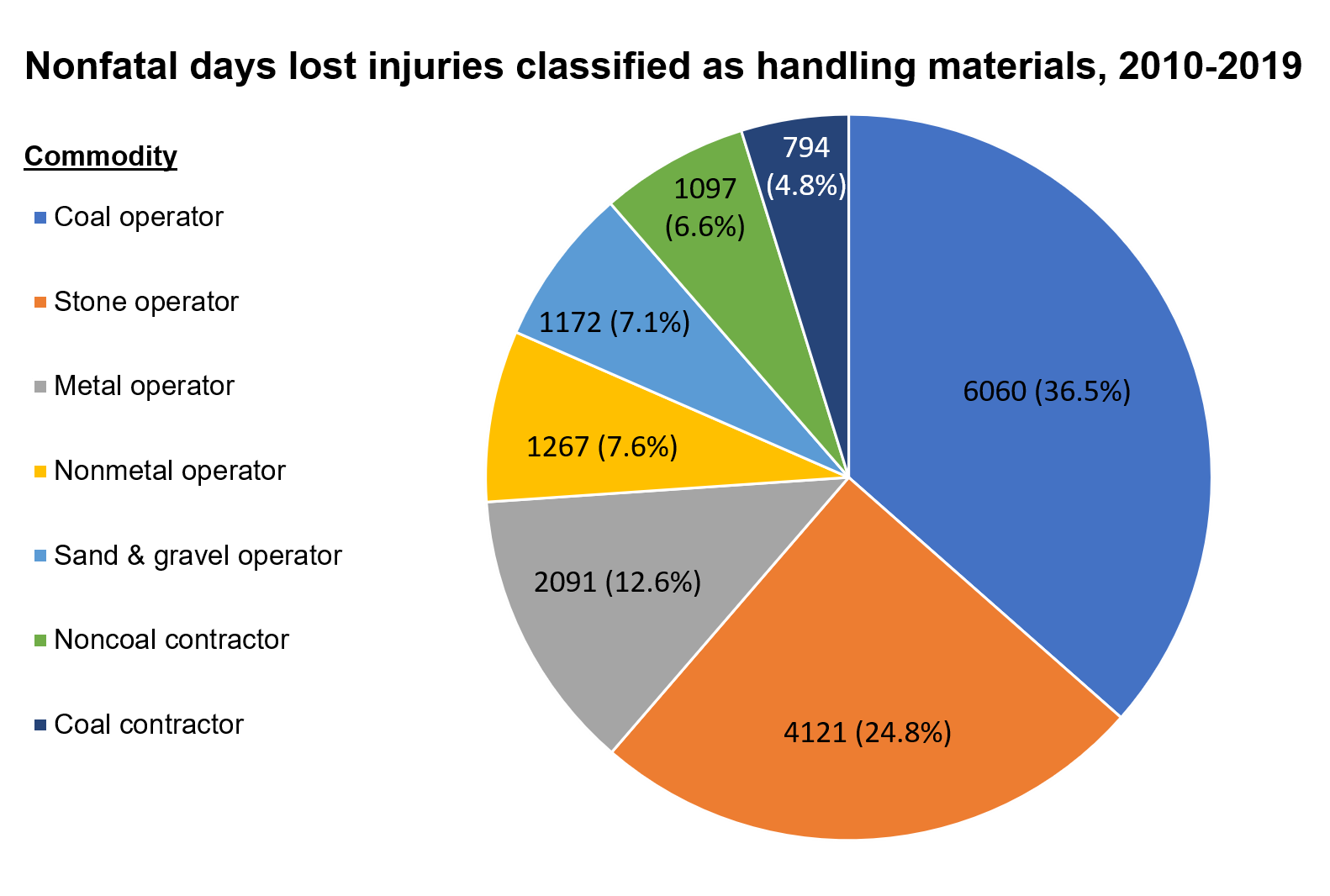
Figure 1. Nonfatal days lost injuries relative to commodity - coal and noncoal mining operations. (Click for larger image.)
What is the extent of the problem?
Handling materials is the leading cause of nonfatal days lost (NFDL) injuries in mining accounting for approximately 1660 injuries per year between 2010 and 2019. A breakdown of these injuries is illustrated in Figures 1 and 2 according to: commodity – coal and noncoal mining operations, and mine worker activity. Surface mining accounts for 65% of the total NFDL’s compared to underground mining at 35%. The highest percentage of NFDLs occurs in the coal industry (36.5%), followed by stone (24.8%), metal (12.6%), nonmetal (7.6%), and sand & gravel (7.1%).
Sprains or strains (49.1%, 816 injuries per year) are the leading type of NFDL injuries in mining for material handling with fracture, chip (13.8%, 2292 injuries per year) second, and cut, laceration, puncture (11%, 1829 injuries per year) third. Among sprains or strains, the back (45.7%) and shoulders (21%) are the most frequently injured body parts. Nevertheless, the median number of days lost for a shoulder sprain or strain (35 days) is more than 8 times that for a back sprain or strain (4 days). Traditional workplace safety practices target the back and may neglect the impact of shoulder injuries, which are known to have an increased prevalence in older populations and require significant healing time.
The following MMH activities were the primary sources of NFDL injuries: handling supplies or material load and unload (45%); machine maintenance/repair (24.3%); handling coal, rock, waste or ore (5.3%); move power cable (4.5%); hand load; hand shoveling/mucking (3.8%); get on or off equipment machines, etc. (3.0%); and moving equipment (1.7%). The top five sources of MMH injury include: metal not elsewhere classified (pipe, wire, nails, manhole covers) (17.8%); metal covers and guards (14.8%); broken rock, coal, ore, waste (9%); belt conveyors (4.6 %); conductors, electric cables and trolley poles (4.6 %).
What are the major risk factors?
Ergonomic risk factors exist in the workplace as a result of a reactive ergonomics process. These risk factors relate to work activities that make it more difficult to maintain the musculoskeletal system in a healthy balance and increase the likelihood of developing a musculoskeletal disorder (MSD). Major ergonomic risk factors are:
- Highly repetitive tasks – High levels of task repetition, when combined with other risks factors such high force and/or awkward postures, can contribute to developing MSDs.
- Forceful exertions – Numerous work tasks impose loads of high force on the human body. High force demands require increased muscle effort that leads to increasing fatigue and the potential for developing MSDs. General guidance is to not lift objects greater than 40 lbs.
- Repetitive/sustained awkward postures – Awkward postures stress the joints and overload the muscles and tendons around the joint through excessive force. The body’s joints are most efficient when they work close to the mid-range motion of the joint. Injury risk increases when joints work beyond this mid-range repetitively or during sustained intervals without adequate recovery time.
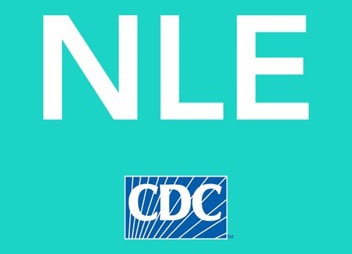
Figure 3. The NIOSH Lifting Equation mobile app, NLE Calc, calculates the overall risk index for single and multiple manual lifting tasks.
How is the NIOSH Mining program addressing this problem?
One of the tenets of injury prevention is education and resources. The NIOSH Mining Program has created several training packages to educate mine workers on ergonomic risk factors as they relate to mining workplace practices (see Figure 3 and section below on Relevant Resources). Additionally, the NIOSH Mining Program also promotes the use of mechanical assist devices to reduce the necessary force application as well as lift tables (Figure 4) and workstation redesign to promote improved posture when lifting. Further, we presently have an intramural project focusing on hand and finger injuries and the application of exoskeletons to mining. Stay tuned to this website for future updates.
What are the significant findings?
Research studies have been conducted to examine the impact of manual materials handling when in restricted postures, when working in workstations of varying heights, and when performing repetitive stacking tasks. Posture is a significant factor in manual materials handling. Even moderate weights can cause an increased risk for injury when lifted incorrectly. Posture can be influenced by several factors which can be personal as well as environmental. Restricted vertical heights require workers to stoop, squat, or kneel which reduces lifting capacity. Stacking on pallets located at floor level requires workers to fully flex their back. Stacking on pallets exceeding shoulder level requires shoulder flexion to access higher areas. Non-adjustable workstations may also require awkward postures for some workers.
Mine Safety and Health Administration (MSHA) data (2011 – 2017) show that injuries related to hands and fingers are predominant in mining. It is important for prevention efforts to identify factors linked to these injuries. Hand and finger injuries occur at an average rate of 6.53 per 1000 full-time employees (Figure 3), which is nearly double the rate of the next highest affected body part, the back. Most hand and finger injuries are associated with cuts/lacerations/punctures (53%) followed by bone fractures/chips (26%). Manual material handling, machine maintenance and repair, and hand tool use were the most common activities associated with hand and finger injuries. Primary sources of hand and finger injury included miscellaneous metal materials (pipe, wire, guarding) and hand tools. MSHA data do not explicitly cover personal protective equipment use. However, a review of the limited injury narratives (where glove use was explicitly documented) revealed that leather gloves were most often worn when an injury occurred. Gloves, when worn, contributed to 20% of the injuries, thus, showing the potential to protect the hands but also put the hands at risk. Performance requirements for gloves used in mining operations still need further study, specifically those offering cut and puncture resistance. Glove design should be studied and improved to ensure that gloves do not create additional hazards when used.
What are the next steps?
We currently have an intramural project focusing on manual material handling specifically related to hand and finger injuries and the application of exoskeletons to mining. Research will continue in this area with the hopes of providing better education on safe workplace practices and workstation design for manual materials handling and ensuring mining companies are aware of devices to improve worker safety when performing these tasks. Additionally, publications are available with recommendations to reduce injury risks associated with manual materials handling.
Relevant Resources
NIOSH
Work Practices Guide for Manual Lifting
This report presents quantitative recommendations regarding the safe load weight, size, location, and frequency of material handling. In addition, engineering guidelines are provided for the design of workplaces where manual materials handling is performed.
Ergonomic guidelines for material handling
This booklet will help you to recognize high-risk MMH work tasks and choose effective solutions for reducing physical demands.
The effects of operator position, pallet orientation, and palletizing condition on low back loads in manual bag palletizing operations
This study evaluates the biomechanical demands of different work layouts when performing manual palletizing of small bags; the biomechanical stresses associated with different stacking techniques are also evaluated.
ErgoMine
ErgoMine is an ergonomics audit tool designed specifically for mining. It includes audits for bagging, haul truck, and maintenance and repair operations at surface mining and processing facilities. Based on your responses to the audit questions, ErgoMine provides recommendations when there is an opportunity for ergonomics improvement.
Simple Solutions for Surface Mine Workers
This booklet is designed to provide examples of solutions and task design ideas that you can use to reduce exposure to risk factors for musculoskeletal disorders and slips, trips, and falls. Although not an exhaustive list, the ideas in this booklet can be used as a foundation for developing similar types of solutions.
A Case Study of Roof Bolting Tasks to Identify Cumulative Trauma Exposure
Roof bolting tasks were analyzed at a mine to identify early warning signs of cumulative trauma. Recommendations to reduce cumulative trauma exposure were provided including job procedures, equipment design, and worker awareness of risk factors.
Ergonomics and Risk Factor Awareness Training for Miners
This training is designed specifically for the mining industry and should increase awareness of risk factors and encourage miners to take action to report and reduce their exposures to risk factors.
Ergonomics: Beyond Compliance
While ergonomics is not a currently regulated field, many mines are realizing that the only way to tackle their most costly injuries, cumulative injuries, is to make the proactive choice to understand those injuries, their root causes and to make workplace changes to prevent them from occurring. Reduction of these injuries not only improves the health and morale of the workers but increases productivity and profit for the companies. Knowledge and reporting of ergonomic risk factors by employees and ergonomics committees is key to these changes and to the reduction of cumulative injuries.
External L5-S1 Joint Moments When Lifting Wire Mesh Screen Used to Prevent Rock Falls in Underground Mines
The study investigated the biomechanical load on the lower back associated with bolting large sheets of wire mesh screen (WMS) to the roof of underground mines.
Inexpensive, Easy to Construct Materials-handling Devices for Underground Mines
This report describes the development and testing of six materials-handling devices including a scoop-mounted lift boom, a swing-arm boom, a heavy component lift-transport, a mine mud cart, a container-work station cart, and timber car.
Solutions to Prevent Materials-Handling Injuries in Underground Coal Mines
This paper describes the development of three mechanical methods – the mobile manipulator, the in-mine hoist, and a cable-handling system – for loading, unloading, moving supplies and materials, and handling trailing cables.
Using Ergonomics to Enhance Safe Production at a Surface Coal Mine - A Case Study with Powder Crews
This article presents a process to identify tasks that workers believed involve the greatest risk factors exposure to MSDs and discusses risk reduction strategies. A case study using this process identifies and ranks routine work tasks which pose risk factors for MSDs at a surface coal mine.
MSHA
Mine Safety and Health Administration, National Mine Health and Safety Academy - Material Handling Safety at Surface Mines, Mills, and Plants: CD-catalog number IG 89, request a copy from MSHA's Academy Library
OSHA
Occupational Safety and Health Administration - Handling Materials
Occupational Safety and Health Administration - Materials Handling and Storing