Florist Pinned Between Bucket of an Industrial Truck and Semi Trailer in Wisconsin
Wisconsin FACE 99WI076
SUMMARY:
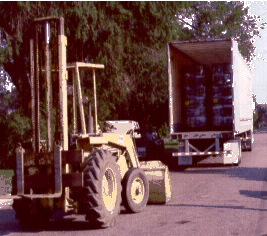
A 36-year-old male florist (the victim) died after being pinned between the bucket of a bucket loader/forklift truck (loader) and the back of a semi trailer. The florist was co-owner of the retail floral shop on the street where the incident occurred. The loader was operated by an employee of an excavating company which was contracted to provide forklift services at the floral shop site. At the time of the incident, the victim was standing in front of the trailer, directing the operator of the loader to move a few inches closer to the trailer so the end of a chain could be attached to the bucket. The loader lurched 3-4 feet forward, pinning the victim against the trailer. After several unsuccessful attempts to move the loader into reverse, the loader operator backed away and the victim fell to the ground. The operator called for help, and emergency services were summoned. EMS responders and police arrived, and the victim was taken to the hospital by ambulance, where he died. The FACE investigator concluded that, to prevent similar occurrences, employers should:
- develop service contracts only with companies that have established histories of experience, expertise and safety in the activity to be performed.
- ensure that companies that provide forklift services at the employer’s worksite establish and enforce a powered industrial truck safety program, including industrial truck inspection and maintenanceand operator training.
In addition, individuals who work near industrial trucks should:
- stand away from the pathway of an industrial truck
and, manufacturers of industrial trucks should:
- consider standardizing the location and function of pedals, levers, gauges, and other control devices and indicators.
INTRODUCTION:
On September 1, 1999, a 36-year-old male floral shop owner died after he was pinned between a loader bucket and the back of a semi- trailer. The Wisconsin FACE field investigator learned of the incident from the Division of Workers’ Compensation in the Department of Workforce Development on November 30, 1999. On May 2, 1999, the field investigator met and interviewed officials who had information about the case. The victim’s family members declined to be interviewed at that time. The FACE investigator also obtained the death certificate and the coroner and police reports.
The victim and his brother were co-owners of a retail floral shop which had been in business for about 25 years. Eleven employees worked for the floral business. An excavating company owned the industrial truck and employed the operator that were also involved in the incident. This company employed about 15 people, and was located in the same city as the floral business. The semi-truck was driven by a Canadian long-distance trucker who was not involved in the incident.
No information was available about the safety program or training at the florist shop or trucking company. The written safety and health program at the excavating company did not provide specific policies and procedures about the safe operation of powered industrial trucks. By policy, equipment operators were responsible for maintaining or ensuring the maintenance of the equipment they used. The responsibility included adjusting brakes, checking tires, cleaning radiators, checking hoist seals and cables, adjusting tracks, keeping the equipment clean, greased, oiled and filled with fuel and coolant. The industrial truck driver had worked at the company for about ten years, and received training through the union and from on-the-job experience with backhoes, loaders, and bulldozers. He had not received formal training in the operation of a powered industrial truck, nor evaluation of his competency to operate the company’s vehicle.
INVESTIGATION:
About six weeks before the incident, the floral shop owners had requested the excavating company to provide equipment and assistance with cleaning up debris around the greenhouse and other tasks. A specific request was made for a date when a semi-truck load of peat was scheduled to be delivered to the floral shop. In previous years, the shop employees had manually unloaded the pallets of peat. This year, the owners decided to unload by using a forklift to remove 21 pallets (2100 lbs. apiece) from the truck bed. The gasoline-powered industrial truck that was specified by the excavating company to be delivered to the floral shop was more than 40 years old, and had been purchased about one year before the incident. It had large, pneumatic tires on the rear with wide-set smaller tires on the front. A forklift column was mounted on the back and the front was equipped with a bucket loader. The company intended to use it primarily for their own yard work, and did not maintain records of any maintenance performed on the machine. They did maintain records of the comprehensive inspection and maintenance activities for the excavating machines used in the business.
At about 6:15 on the morning of the incident, the operator arrived at the company yard and was assigned to work at the floral shop. The yard man started the loader for the operator and loaded it onto a trailer for transport to the floral shop. He did not notice any problems with the machine’s operation. The operator rode with a company truck driver who drove the trailer to the floral shop, where the truck driver unloaded the loader. The truck driver had operated the loader on at least six previous occasions, and knew the loader brakes did not work well. It is unknown if he told the operator about the brakes. After unloading the loader, the driver turned the machine off and returned to the excavating company. The victim and the operator did some work around the greenhouse until the semi-truck arrived.
The semi-truck driver stayed in the truck cab while the victim, a floral shop employee (co-worker), and the operator prepared to unload the truck. The victim obtained a 16-foot chain to attach to the pallets, while the operator attempted to start the loader. He was unsuccessful after several attempts, then called the excavating company for assistance. The company yard man came to the site, and started the loader for the operator. The co-worker went inside the truck trailer, while the victim stood on the pavement at the back of the truck. The operator moved the bucket close to the end of the truck, and the co-worker attached one end of the chain to a pallet of peat inside the truck. The victim attached the other end of the chain to the bucket, and the operator backed up to pull the pallet to the end of the truck bed. The chain was removed, the operator turned the loader around, and used the forklift to remove the loaded pallet from the truck. They unloaded a second pallet in this manner, and were preparing to unload a third.
The co-worker had attached the chain to a pallet inside the truck, so the victim was ready to attach the chain to the bucket. He was standing in front of the trailer, but the chain didn’t reach the bucket so he motioned to the operator to move forward a few inches. The loader lurched forward, pinning the victim between the bucket and the trailer. After several unsuccessful attempts, the operator backed the loader and the victim fell to the ground. The co-worker went to aid the victim while the operator called for emergency services. A police patrol car was in the neighborhood and responded within five minutes, and EMS services arrived soon after. The victim was transported to the hospital, where he died. An inspection of the loader after the incident revealed that after placing the machine in forward gear, it would take some time before the transmission fluid built enough pressure to move the machine. Then the machine would suddenly lurch forward and full force brake pressure would not stop the machine until it had traveled several feet. Mechanical brake adjustment on this loader can be achieved by tightening a bolt under the loader body.
CAUSE OF DEATH:
The death certificate listed the cause of death as exsanguination from massive internal trauma due to a crushing injury.
RECOMMENDATIONS/DISCUSSION
Recommendation #1: Employers should contract only with companies that have established histories of experience, expertise and safety in the activity to be performed.
Discussion: The florist business requested the services of an excavating company to provide forklift equipment and operator services. This was not the company’s usual work activity, and it was unprepared to provide the services in a manner that ensured safety for all individuals at the worksite. The florist business should have sought a contract with an established forklift service contracting company.
Recommendation #2: Employers should ensure that companies which provide forklift services at the employer’s worksite establish and enforce a powered industrial truck safety program, including industrial truck inspection and maintenance and operator training.
Discussion: The provisions of a contract for forklift services should include provisions for safe equipment and operator training. An effective inspection and maintenance program should detect and correct defects in industrial trucks. If the loader in this incident had been inspected on a regular basis and before each use, the malfunctions of the transmission and brakes might have been discovered and repaired. Also, the operator had not had formal training for industrial truck operation and was inexperienced in operating this loader. He apparently did not know about the machine’s tendency to lurch and not be immediately stopped by full brake pressure. He followed the victim’s directions to move the loader forward a few inches, while the victim was standing in front of the trailer. If the operator had received formal training and been evaluated for his ability to operate the loader, he might have recognized the hazards posed by the faulty machinery and the risk to the victim of standing in front of a stationary object.
ADDITIONAL RECOMMENDATIONS:
Recommendation #3: Employees who work near industrial trucks should never stand in the pathway of an industrial truck.
Discussion: Employees who work where industrial trucks are moving should receive and heed training in the recognition and avoidance of hazards and unsafe work practices in their environment. The victim in this case may have failed to realize the hazard of standing between the bucket and the truck. Hazard recognition and avoidance training may have helped each of the workers realize that before the operator moved the loader, the pedestrian workers should move out of the area where the loader would be driven.
Recommendation #4: Manufacturers should consider standardizing the location and function of pedals, levers, gauges, and other control devices and indicators on powered industrial trucks.
Discussion: The location and function of control devices for steering, brakes, acceleration, and powered equipment attachments are not standardized on industrial trucks. Workers who operate multiple vehicles of more than one model or manufacturer may confuse the action of a device, and create an undesired effect. For example, a worker might mistakenly depress an accelerator pedal while intending to brake a vehicle, if he/she had recently or previously operated a vehicle with controls in different locations.
REFERENCES
- Code of Federal Regulations 29 CFR 1910.178, 1999 edition. U.S. Government Printing Office, Office of the Federal Register, Washington, D.C.
FATAL ASSESSMENT AND CONTROL EVALUATION (FACE) PROGRAM
FACE 99WI076
Staff members of the FACE Project of the Wisconsin Division of Health, Bureau of Public Health, do FACE investigations when a work-related fatal machine-related, youth worker or road construction work-zone death is reported. The goal of these investigations is to prevent fatal work injuries in the future by studying: the working environment, the worker, the task the worker was performing, the tools the worker was using, the energy exchange resulting in fatal injury and the role of management in controlling how these factors interact.
To contact Wisconsin State FACE program personnel regarding State-based FACE reports, please use information listed on the Contact Sheet on the NIOSH FACE web site. Please contact In-house FACE program personnel regarding In-house FACE reports and to gain assistance when State-FACE program personnel cannot be reached.