Equipment Operator Killed When Tree Trunk Crashes Through Window of Excavator
FACE Investigation # 98 NJ-018-01
DATE: September 23, 1998
SUMMARY
On February 18, 1998, a 30 year-old department of public works employee died when he was struck by a section of a tree trunk that crashed through the window of the excavator he was operating. A three-man crew was attempting to clear debris out of their path in order to reach a stream. As the operator lifted the tree off the ground, it slipped off the excavator bucket, broke through the front windshield, and pushed against the hand controls. Since the cab of the excavator was rotated, the track control levers essentially worked in reverse. The tree trunk pushed against the controls, causing the excavator to move forward against the trunk. The victim was pushed from the operator’s seat into the rear window. Face investigators concluded that, in order to prevent similar incidents, the following safety guidelines should be followed:
- Recommendation # 1: The manufacturer’s instructions should be followed when using the excavator to lift heavy objects.
- Recommendation # 2: The employer should conduct a job hazard analysis; policies and training should be implemented based upon the findings of the evaluation.
INTRODUCTION
This fatal work-related injury was reported to the NJDHSS FACE staff on February 18, 1998 by the county medical examiner. The employer was contacted and consented to participate in the FACE project. A site visit was conducted on February 26. The employee’s supervisors, their insurance company representative, and the county risk manager were interviewed. The incident site and the excavator were observed. The victim’s co-workers were interviewed on March 4. Further information was received from the medical examiner, police reports, NIOSH, and the NJ Department of Labor, Office of Public Employees’ Safety.
The employer was a unionized county department of public works (DPW) that employed 107 workers and covered 21 municipalities over 102 square miles. The DPW had four divisions, one of which was mosquito control, employing 15 workers, including clericals. During the winter, the mosquito control staff visited areas throughout the county that were known sites of mosquito breeding to clear debris or obstructions and prevent stagnation of water. They removed debris, logs, and other obstructions to water flow and, when necessary, they dredged slow-moving streams.
The DPW used on-the-job training of equipment operators in which supervisors and senior employees, all state-certified operators, taught inexperienced workers the use of the equipment. They started with the basics of maintenance and progressed to machine operations. Workers could be promoted and paid as equipment operators but were not certified until they passed a performance-oriented state certification exam. The exam was given by the state civil service. Operator’s manuals were kept in the machines where they were accessible to operators and other workers.
The DPW had an organized safety program, including what they called an “active safety team.” The team was made up of supervisors, workers, and office staff that represented each of the divisions of the DPW. They met monthly to discuss safety-related issues, review accident reports, and make recommendations for prevention. The safety team implemented suggestions of the accident review committee, a panel of workers that reviewed all accident reports and made suggestions to the active safety team. All workers were given a copy of the DPW safety manual which they were expected to carry in the same bag as their personal protective equipment.
The deceased, a state-certified equipment operator, worked for the DPW for eight years, five years as a laborer and three as an equipment operator. He was considered a very good worker and had been promoted over other workers with more seniority. He was married and served as a volunteer firefighter.
INVESTIGATION
The site of this incident was a dead end dirt road along private property on which a home once stood, now burned down. The area was partially wooded. The ground, bare in places, was covered with shrubs, vegetation, and broken tree limbs. A stream flowed through the back of the property. The crew’s assignment was to clear the stream which was blocked by a fallen tree.
The four man crew reported to work at the county DPW complex at 7:30 a.m.. They were given their assignments by a supervisor, readied their equipment, and put the mini excavator on a trailer to transport it to their work site. They arrived at the incident site between 8:45 and 9 a.m.. The weather that day was misty and overcast. The ground was muddy because it had rained the night before.
The crew consisted of a site supervisor, one equipment operator (the victim), a heavy equipment operator, and a provisional equipment operator (one who had not yet passed the certification examination). A supervisor had made a visit to the site prior to the incident. The mosquito control staff had been at the site several times in past years, including when the house was still standing.
At the site, they moved the excavator off the trailer and started work. The excavator was a mini hydraulic excavator, used in small streams and congested areas. The machine weighed 14,000 pounds, had a 55 horse power diesel engine, and was equipped with a dozer blade on the front. The excavator’s overall height was 8 feet 5 inches (from ground to the top of the cab). The operator’s cab was surrounded with windows made of safety glass. Mounted on steel tracks, the cab with the arm and boom was able to rotate 360 degrees. One control stick controlled each track. Pushing simultaneously on both control sticks caused the machine to move forward, front meaning oriented toward the dozer blade. Pulling on both sticks caused it to go in reverse, in the direction away from the dozer blade. When the cab was rotated, the controls essentially worked in reverse: pushing caused reverse motion while pulling caused the machine to travel forward. Other controls maneuvered the boom, arm, bucket, and dozer blade.
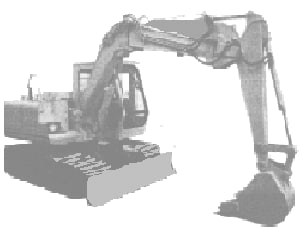
Mini Excavator
FACE Investigation 98NJ-018-01
Although the men planned to clear the stream, they first needed to clear away debris and fallen trees that were in their path. They planned to be at the site all day. After unloading the machine from the trailer, the provisional equipment operator took over the mini excavator. He had problems trying to move the downed trees, due to his inexperience. The site supervisor directed that the victim take over and the provisional operator observe him. A fallen tree, 28 feet long and 12 inches in diameter, was across their path, about 25 feet from the stream. The trunk was lying on the ground, with its upper branches still attached, making it too heavy to move by hand. They had no chain saw to use to cut the tree into smaller sections. The deceased used the excavator bucket to pick up the tree trunk. He cradled it at the junction of the bucket and arm of the machine, with the bucket curled in a loading position. The boom was raised to a position greater than 90 degrees, with the teeth of the bucket approximately level with the base of the boom. The tree trunk was at least 8 feet above the ground. The operator was reportedly lowering the boom to put the tree trunk in a more maneuverable position. When the machine moved, the tree trunk slipped off the bucket. The jagged-edged trunk crashed end-first through the front window, just catching the top of the cab and breaking the glass into the cab. It pushed against the hand controls and the victim. He was pinned against the rear window of the cab. Since the excavator had been rotated, the action of the tree trunk pushing against the controls caused the excavator to move forward, increasing the force of the log against the victim. The operator was forced back and upward; his back pushed out the rear window while his co-workers watched helplessly.
While one colleague called for assistance on their two-way radio at 9:30 a.m., another attempted to shut off the machine. He climbed up on the moving track but was thrown off. He climbed up again and reached into the cab to turn the key in the ignition to the off position. A worker tried, unsuccessfully, to dislodge the 6½ foot long section of the tree trunk that had entered the cab. Police arrived at the scene first, followed by emergency workers. DPW supervisors returned to the site as soon as they heard the call. Approximately fifty people responded to the emergency call. A firefighter used a chain saw to cut the tree trunk during the rescue process. The victim was pronounced dead at the scene shortly after 10 a.m.
A few workers were treated in the local emergency room for emotional shock. Employees were provided with crisis counseling through the employer’s Employee Assistance Program and some individuals were also offered continuing counseling.
CAUSE OF DEATH: The medical examiner determined that death was caused by “positional asphyxiation.”
RECOMMENDATIONS/DISCUSSIONS
Recommendation # 1: The manufacturer’s instructions should be followed when using the excavator to lift heavy objects.
Discussion: It is permissible to lift heavy objects using the excavator if the manufacturer’s instructions are followed. The operator’s manual instructs the operator to check the lifting capacity section of the operator’s manual or the chart posted on the excavator’s window. These inform the operator of how much weight the machine can lift at specific distances from the center of rotation. The operator is instructed to: 1) secure a sling or chain tightly to the load being lifted; 2) fasten the sling or chain to the machine with the bucket curled and arm retracted; and 3) lift the load only as high as necessary.
In situations such as this, the downed tree could be cut into smaller sections using a chain saw. Those sections could have been lifted with slings attached to the excavator bucket. An alternate way would have been to secure the trunk to the excavator by attaching chains or slings near the end of the tree trunk. With the sling/chain attached to the bucket’s lift points, the tree could have been slid or pivoted out of the way.
Recommendation # 2: The employer should conduct a job hazard analysis; policies and training should be implemented based upon the findings of the evaluation.
Discussion: There were several factors that may have influenced this incident: 1) the workers had no chain saw to use to cut the downed tree into manageable sections; 2) they had no slings or chains to use to move heavy items; 3) the tree trunk was held, unsecured, 8 to 10 feet above the ground; and 4) a worker reported breaking the bottom window of the excavator, in the past, from tree limbs. A job hazard analysis should be done to consider and evaluate factors such as these. A job hazard analysis evaluates the tasks that workers must perform and their ability to do them. It also determines existing or potential hazards, and designs procedures on ways to eliminate or avoid the hazards. The hazard analysis can be used in planning work at each site when a pre-work inspection is done by a supervisor.
The employer should include hazard recognition in the employees’ training. Although the employer had a safety program in place, workers should be taught to recognize unsafe tasks, equipment, and work practices. Since training cannot cover every situation in which a worker may find himself, this type of knowledge would be applicable to any usual or unusual situation.
Although workers may be experienced in their trade, periodic re-training and updates on new procedures and equipment are necessary. The DPW has conducted a retraining of all employees who operate excavators. They used videos obtained from the excavator manufacturer and included a question and answer session in the training.
ATTACHMENTS
U.S. Government Printing Office, U.S. Department of Labor, Occupational Safety and Health Administration, Job Hazard Analysis, 1988. OSHA 3071
REFERENCE
Equipment Manufacturers Institute, 10 South Riverside Plaza, Chicago, Illinois 60606, 1992.
U.S. Government Printing Office, U.S. Department of Labor, Occupational Safety and Health Administration, Job Hazard Analysis, 1988. OSHA 3071
FATALITY ASSESSMENT AND CONTROL EVALUATION (FACE) PROJECT
Investigation # 98-NJ-018-01
Staff members of the New Jersey Department of Health and Senior Services, Occupational Disease and Injury Services, perform FACE investigations when there is a report of a work-related fatal fall or machine-related incident. The goal of the FACE Program is to prevent future incidents by studying and identifying the risk factors that contribute to workplace fatalities, by recommending intervention strategies, and by disseminating information to employers and employees. All NJ FACE data are reported to NIOSH for trend analysis on a national basis. All identifiers are removed from the FACE reports and other data to protect the confidentiality of those who participate in the program.
NIOSH funded state-based FACE Programs include: Alaska, California, Iowa, Kentucky, Maryland, Massachusetts, Minnesota, Missouri, Nebraska, New Jersey, Ohio, Oklahoma, Texas, Washington, West Virginia, and Wisconsin.
To contact New Jersey State FACE program personnel regarding State-based FACE reports, please use information listed on the Contact Sheet on the NIOSH FACE web site. Please contact In-house FACE program personnel regarding In-house FACE reports and to gain assistance when State-FACE program personnel cannot be reached.