Painter/Boat Operator and Acquaintance Drowned --South Carolina
FACE 9223
SUMMARY
A 31-year-old painter/boat operator (victim #1), and his 31-year-old acquaintance (victim #2), drowned when the work boat they were aboard sank. At the time of the incident, victim #1 was employed as a work boat operator, shuttling fuel from the pier at the river’s edge to a work barge anchored in the river channel, about 200 feet from the pier. Victim #2 had been invited aboard by victim #1 (without employer authorization) to accompany him until he completed his shift at 12 a.m. At some time between 10:30 p.m. and 12 a.m., fuel had been delivered to the work barge anchored in the river. Although unwitnessed, evidence suggests that the work boat had returned to the pier and once again departed towards the river channel. The work boat apparently became caught in a strong ebb tide (i.e., the flowing back of the tide as the water returns to the sea), which caused it to collide with a barge docked at the pier. The collision capsized and sank the work boat. Both victims were tossed into the river and drowned. Neither victim had been wearing a lifejacket. NIOSH investigators concluded that, in order to prevent future similar occurrences, employers should:
- evaluate their current safety program and incorporate specific training procedures emphasizing the importance of recognizing and avoiding hazards in the workplace, and encourage workers to actively participate in workplace safety by following established work procedures with particular emphasis on wearing lifejackets
- conduct a jobsite survey to identify potential hazards, implement appropriate control measures, and provide subsequent training to employees that specifically addresses all identified site hazards
- routinely conduct scheduled and unscheduled jobsite safety inspections.
INTRODUCTION
On May 13, 1992, a 31-year-old painter/boat operator, and his 31-year-old acquaintance, drowned when the work boat they were aboard sank. On June 10, 1992, officials of the South Carolina Occupational Safety and Health Administration (SCOSHA) notified the Division of Safety Research (DSR) of the fatality, and requested technical assistance. On July 31, 1992, a DSR safety specialist traveled to the incident site to conduct an investigation. The incident was reviewed with the project superintendent, union shop steward, and the SCOSHA compliance officer assigned to the case. Photographs of the incident site were taken, and copies of the medical examiner and police reports were obtained.
The employer in this incident was a bridge painting contractor who had been in operation for 34 years. The contractor employed 250 workers, of whom approximately 200 were painters/boat operators. The employer had a written safety policy and comprehensive safety program which included hazard communication training sessions and provisions for disciplinary actions for violation of safety rules. The safety program was administered by the project superintendent. The project superintendent and the three jobsite foreman were responsible for jobsite safety. The victim was hired through the local union hall and had worked for the employer for 2 months prior to the incident. This was the first fatality the company had experienced.
INVESTIGATION
The painting company had been sub-contracted to sandblast and paint a 700-foot-long bridge across a river. Work had been in progress since December 1990, and was approximately 80% completed. Twenty-six workers were assigned to this jobsite.
On the day of the incident, 26 workers–3 foremen, 5 iron- workers, 5 riggers, and 13 painters/boat operators, including victim #1–arrived at the jobsite for the 8 a.m. to 4 p.m. daylight shift. The workers on the daylight shift were assigned various sandblasting and painting tasks on the steel bridge structure which was several hundred feet above the river’s surface. Victim #1’s task was to operate the boat which shuttled fuel from the pier at the river’s edge to the work barge anchored about 200 feet into the river channel. Lighting and compressed air for the jobsite were being supplied by generators and air compressors on the 30-foot long barge. After working the daylight shift, victim #1 requested overtime to continue shuttling fuel on the afternoon shift. The request was granted and victim #1 continued his assigned duties.
At approximately 10 p.m., victim #1 telephoned an acquaintance and asked him to come to the jobsite and accompany him until the end of his shift. The acquaintance, victim #2, arrived about 10:30 p.m. and boarded the work boat with victim #1 without employer authorization. Sometime between 10:30 p.m. and 12 a.m., the two men shuttled a load of diesel fuel from the pier to the work barge. The fuel was contained in a 500-gallon drum on a small work barge, which was being pushed by the work boat. After unloading the fuel, they returned to the pier and moored the small work barge. Apparently, they then piloted the work boat back into the channel, where it was caught by a strong ebb tide. The tide pulled the boat into a barge which was moored at the pier. The boat struck a metal plate on the barge, and the boat capsized and sank (Figure). Although approved lifejackets were available on the work boat, they were not being worn by the victims and both drowned. Autopsy reports indicated that both victims were under the influence of alcohol at the time of the incident.
CAUSE OF DEATH
The medical examiner’s reports listed the cause of death as asphyxiation due to drowning.
RECOMMENDATIONS/DISCUSSION
Recommendation #1: Employers should evaluate their current safety program and incorporate specific training procedures emphasizing the importance of recognizing and avoiding hazards in the workplace, and encourage workers to actively participate in workplace safety by following established work procedures with particular emphasis on wearing lifejackets.
Discussion: Although the company had a written safety program, there were no provisions for recognizing and avoiding hazards in the workplace, such as tides and currents. The safety program should be evaluated and specific training procedures incorporated, with particular emphasis on the importance of recognizing and avoiding potential work place hazards, such as tides and currents. For these procedures to be effective, they must be clearly communicated and fully understood by the affected employees and supervisors. In this instance, neither victim wore an approved lifejacket or buoyant work vest in violation of established company safety rules, and victim #2 had not been authorized by the employer to be aboard the work boat. Employers must instruct workers of their responsibility to participate in making the workplace safer, and ensure that all workers understand the role they play in the prevention of occupational injury.
Note: Since this incident, the company has updated the safety program to include, but not be limited to, training sessions in the hazards of tides and currents.
Recommendation #2: Before starting any work, employers should conduct a jobsite survey to identify potential hazards, implement appropriate control measures, and provide subsequent training to employees that specifically addresses all identified site hazards.
Discussion: Employers should conduct a jobsite survey to identify potential hazards prior to beginning work. The jobsite in this incident contained at least three identifiable hazards: a) strong ebb tides, b) work to be performed in proximity to a barge docked at the pier, and c) work near water. Once potential hazards are identified, appropriate control measures should be implemented and workers provided with training in the control measures to be taken. Control measures for this jobsite include wearing an approved lifejacket or buoyant work vest, and maintaining a minimum distance between the work boat and docked barge in the presence of strong ebb tides.
Recommendation #3: Employers should routinely conduct scheduled and unscheduled jobsite safety inspections.
Discussion: Scheduled and unscheduled safety inspections should be conducted by competent individuals. No matter how comprehensive, a safety program cannot be effective unless implemented in the workplace. Even though these inspections do not guarantee the elimination of occupational injury, they do demonstrate the employer’s commitment to the enforcement of an established safety program.
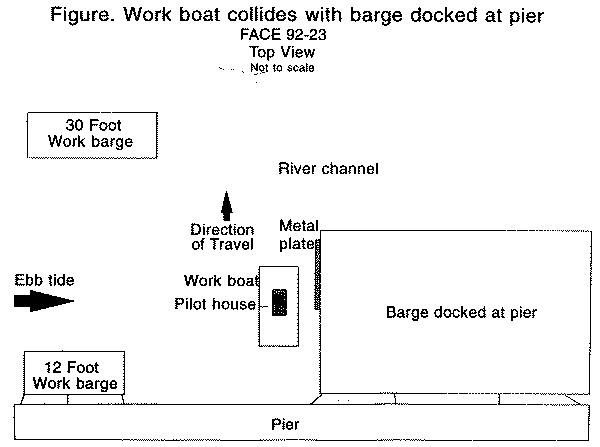