Welder Dies in Fall from Fork Lift
FACE 8945
INTRODUCTION
The National Institute for Occupational Safety and Health (NIOSH), Division of Safety Research (DSR), performs Fatal Accident Circumstances and Epidemiology (FACE) investigations when a participating state reports an occupational fatality and requests technical assistance. The goal of these evaluations is to prevent fatal work injuries in the future by studying the working environment, the worker, the task the worker was performing, the tools the worker was using, the energy exchange resulting in fatal injury, and the role of management in controlling how these factors interact.
On July 16, 1989, a 47-year-old male welder died as the result of falling approximately 7 feet from a fork truck (commonly referred to as a fork lift or towmotor).
CONTACTS/ACTIVITIES
The county coroner contacted DSR about this fatality and requested technical assistance. On July 27, 1989, a research team consisting of a safety specialist and an epidemiologist discussed this case with state officials, conducted an investigation, met with the company owner, and photographed the site of the incident.
OVERVIEW OF EMPLOYER’S SAFETY PROGRAM
The victim had been employed for 5 years as a welder for a welding and machining services company that has been in operation for 21 years. The company employs 45 workers, including 35 welders. The employer uses written safety rules and procedures and provides on-the-job training. The company owner is also the safety officer. Jobsite foremen are responsible for administering and enforcing the safety program. This fatality is the first in the history of the company.
SYNOPSIS OF EVENTS
On the day of the incident, welding and machining tasks were being performed throughout the plant as usual. The welder (victim) was performing welding tasks assigned to him earlier that morning. A co-worker (fork lift operator) was moving wheel sets (steel axles with steel wheels attached) inside the building where the victim was welding.
The co-worker had just off-loaded a wheel set when he noticed that the fork carriage (assembly to which the forks or other attachments are mounted) was jamming on the mast (upright steel assembly consisting of hydraulic cylinders, inner channels, telescoping outer channels, chains, and guide rollers) (see Figure). The co-worker and victim decided to solve the problem without removing the fork truck from service, a violation of company maintenance procedures.
They backed the fork lift (i.e., a 1979 V225 diesel-powered fork truck with an 11-ton lifting capacity) out of the work area, set the brakes, blocked the wheels, raised the fork carriage up the mast to the point where it jammed, and shut off the engine.
The victim noticed that a wear guard strip, attached to the side of the telescoping channel on the mast, had come loose and was binding against the guide roller. This caused the top of the fork carriage to jam approximately 8 feet from the ground. The victim, carrying a cutting torch, climbed up the carriage and stood on an angled, 6-inch-wide steel support to cut out a section of the wear guard strip as the co-worker observed. The victim then used a pry bar to move the wear guard strip away from the guide roller. As the strip dislodged from the roller guide, the carriage dropped approximately 1 foot.
Due to the jerking motion of the carriage, the victim fell from the angled steel support headfirst onto a concrete pad. The local emergency medical service (EMS) was summoned and arrived approximately 4-5 minutes later. Approximately 35 minutes thereafter, the victim was air-evacuated to the hospital where he died 2 days later.
CAUSE OF DEATH
The medical examiner’s report listed blunt force trauma to the head as cause of death.
RECOMMENDATIONS/DISCUSSION
Recommendation #1: Employers should review, revise where applicable, and enforce current safety programs.
Discussion: Although the company has a written safety program, including maintenance procedures for fork trucks, the procedure was not followed. If the victim and co-worker had informed the jobsite foreman of the fork lift problem, according to procedure, the truck could have been moved to the maintenance shop and repaired according to company maintenance procedures, thereby avoiding the incident. Employers should review, revise where applicable, and enforce the current safety program. The program should be clear and should emphasize the importance of following established operating procedures.
Recommendation #2: Employers should ensure that employees are aware of, and fully understand the risks associated with, failing to comply with established operating procedures.
Discussion: Unscheduled maintenance by unauthorized personnel can and does lead to injury and even death. Apparently the two workers (the victim and co-worker) did not perceive the 8-foot distance as a hazard associated with working on the fork lift, and a fatality resulted. If the standard operating procedure had been followed, this incident may have been avoided. Employers should ensure that all employees are aware of, and fully understand, the risks associated with not complying with established operating procedures.
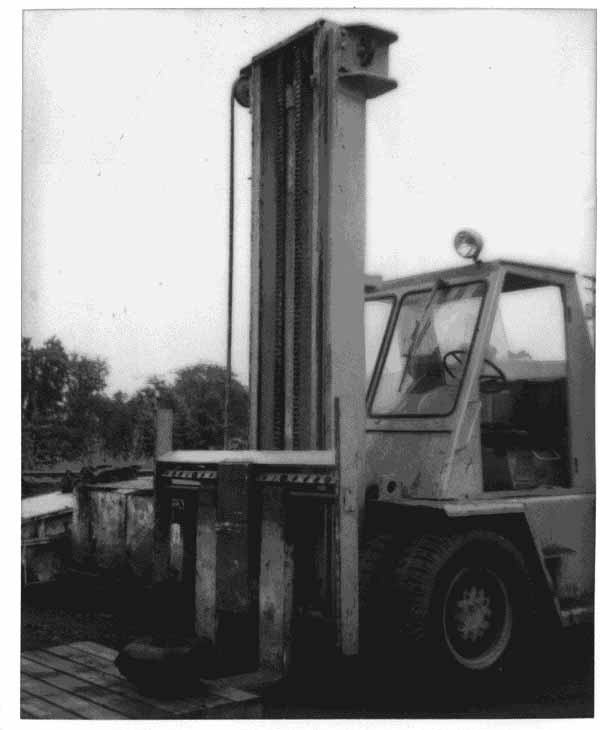
Figure.