PAINT STORE FIRE KILLS OWNER AND EMPLOYEE
-
FACE 8416
INTRODUCTION
The National Institute for Occupational Safety and Health (NIOSH), Division of Safety Research (DSR), is currently conducting the Fatal Accident Circumstances and Epidemiology (FACE) Study. By scientifically collecting data from a sample of similar fatal accidents, this study will identify and rank factors which increase the risk of fatal injury for selected employees.
On June 11, 1984 a paint store owner and one employee received second and third degree burns over 90% of their bodies while attempting to extinguish a fire in the owner’s store. Both victims were admitted to a local hospital where the employee and the owner died after one day and one week, respectively.
CONTACTS/ACTIVITIES
DSR received notification of this accident on June 25, 1984 from NIOSH’s Region IV Consultant. Subsequent contacts were made with the county fire marshall and coroner who were involved with this case. The elapsed time (site no longer in tack) and characteristics (small business with the owner dead) precluded a formal FACE evaluation. However, the fire marshall agreed to meet with DSR representatives and provide facts and conclusions resulting from his investigation. Therefore, on July 3, 1984, a DSR team consisting of a safety engineer and occupational health nurse met with the fire marshall and two fire department investigators. Information about the scenario of events was ascertained during this meeting and resulted from the fire marshall’s investigation.
SCENARIO OF EVENTS
At about 2 p.m. on the day of the accident, the owner of a paint store and a part-time employee were placing a special delivery of paint in the store’s storage/mixing area. (The owner was getting stock to open a new store.) A full-time employee was in the storage room mixing an order of paint. It is believed that this employee was preparing the paint to a specific color which required adding pigments and thinners to the basic color. A fourth employee, a sales clerk, was tending the customer sales area.
After the owner and part-time employee completed their task, they headed for the customer sales area through the storage/mixing room. As they were walking toward the access door, the owner tripped on a flexible electric cord. This cord was providing electricity to a paddle mixer which was being used by the full-time employee to stir the bucket’s 5 gallons of enamel paint. When the owner tripped on the cord, this caused a problem at its connection point to the motor housing, thereby causing the mixer to stop. As the owner and full-time employee started repairing the damage, two customers (one retired and one off-duty fireman) entered the store. Upon the customer’s request, the full-time employee left his table to assist them. The owner finished the mixer repairs. Shortly after it was repaired and restarted, the motor began sparking. Apparently, several sparks ignited the paint. The owner attempted to extinguish the small fire by blowing it out. When he realized this was not putting the fire out, he and the part-time employee ran into the front of the store in search of an extinguisher. The owner found one and returned to the fire. The extinguisher wouldn’t work, and he yelled to the employees to get the extra fire extinguisher.
While the employees and customers were searching for the extra extinguisher, the retired fireman reported hearing a “whooshing” sound and seeing the storage room and owner engulfed in flame. Upon seeing this, the full-time employee rushed past the firemen to the storage room apparently to aid the owner.
The retired fireman found the extra extinguisher and applied it to the inside of the burning storage area. By this time the two individuals in the burning room had been totally engulfed in flame and exited through the rear door. As this was occurring, the sales clerk was using the store phone to call the fire department. The part-time employee and the other fireman went to an adjoining store to call an ambulance.
The investigation by the local county fire marshall indicated that a thinning/drying agent in the storage room may have been added to the paint. Its vapors, combined with those coming from the four open 5 gallon buckets of paint, could have caused the small fire to “flash” engulfing the rest of the room and the victims. A one-gallon can of paint and a roll of wallpaper were also found inside an open five gallon bucket. It is theorized that in the confusion and panic, one of the victims tripped or bumped into the many stacks of paint cans and caused cans and rolls of wallpaper to fall. When the gallon of paint and roll of wallpaper fell into an open five gallon bucket, the paint flowed out of the bucket and onto the floor. The owner had paint on his hands and feet indicating that he may have tripped and fell into the spilled paint thereby hindering his egress.
GENERAL CONCLUSIONS AND RECOMMENDATIONS
The probable ignition source was the sparks from a ground fault at the flexible motor cord and motor housing of the paint mixer. In the panic and confusion of trying to extinguish the fire, the burning bucket of paint and improperly stacked supplies were probably knocked over causing paint to spill and the fire to spread. The vapors of open thinning solvent containers in the area may have been ignited by the spreading fire.
While there are many factors which contributed to this accident, there are several which seem to be more important due to their amenability to prevention. The first factor appears to be the tripping hazard resulting from the improper placement of the cord and/or mixer. This in itself is an important symptom of the overall safety problems. it is difficult to say whether the manager tripped over the cord because it was stretched across the aisle or because the normal aisle was partially blocked by the new shipment of paint. Whatever the case, electric cords should not be stretched across any walkway. In addition, cords should be short enough so that they do not create a tripping hazard in the work area itself.
The fire was reportedly caused by sparks falling into the paint bucket. proper repair of the paint mixer cord and/or use of a splash shield over the open bucket of paint would have minimized this possibility.
Housekeeping and storage also contributed to the severe outcome of the accident. Placement of the new shipment of paint resulted in boxes of paint being stacked from the floor almost to the ceiling (in some places they were stacked seven containers high) throughout the storage area. This created a potential hazard of falling paint cans as well as creating a congested work area. There was a large amount of yellow paint on the floor. This paint not only contributed to the spread of the fire, but was also a slipping hazard. The owner of the store had paint on his hands and clothing, indicating that he may have fallen into the paint. How this affected his injuries is not known. This spillage of paint was caused (at least in part) by a 1 gallon can of paint and a roll of wallpaper which fell, from shelving into one of the five gallon buckets. Again, this could have been alleviated by improved housekeeping, proper storage of stock items, and procedures which permit only one bucket of paint to be open at a time while mixing.
A major factor was the lack of a fire prevention and fire emergency plan. “Red label” containers were found throughout the storage room. There were no special provisions made for the use and/or storage of these containers. The only source of mechanical ventilation was the bathroom exhaust fan. (This was on when the fire department arrived.) There were no fire extinguisher location markings, and the employees were not familiar with the locations of the fire extinguishers. Furthermore, one of the fire extinguishers was not functional. In addition to the above deficiencies, the fire department was not called until the fire was out of control. A final indicator that there was not adequate fire emergency training was the full-time employee’s response of rushing into the fire to assist his employer. A well thought out fire emergency plan should be developed and practiced for this type of business activity.
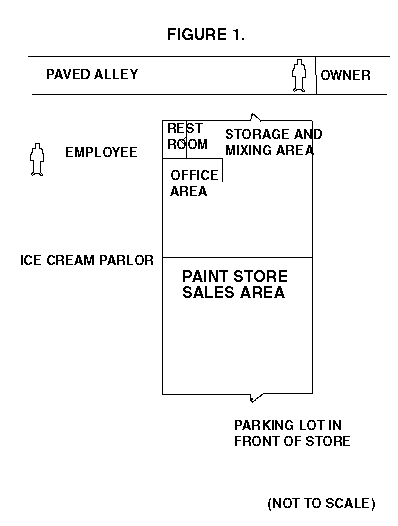