Lineman Killed After Being Struck by a Car in Washington State
![]() |
![]() |
Investigation: #00WA04001
Release Date: December 30, 2003
SUMMARY
On July 25, 2000, a 33 -year old male journeyman lineman died, and a co-worker was injured, after they were struck by a car that drove through a utility construction work zone that was beside the road. The utility lineman (the fatal victim) and the injured co-worker were working with a team of county public utility workers to frame and install a new power pole near an intersection of two county roads. The driver of the intruding vehicle drove past the work zone signage and flagger into the work site. After traveling past the flagger station, the intruding vehicle crossed the opposing traffic lane and shoulder of the road and headed straight into the work zone. The injured co-worker was struck and thrown about 10 to 15 feet onto the grass in the work area. The worker who died struck the hood and windshield and was thrown over the top of the intruding vehicle striking his head on the asphalt pavement of the intersecting road. A witness, who was stopped at one of the flagger stations, immediately called 911 for emergency assistance. Both victims were treated on site and transported to a local emergency room. The fatal victim was airlifted to a trauma center later that day and died of his injuries 10 days later.
To prevent future similar occurrences, the Washington State Fatality Assessment & Control Evaluation (FACE) investigative team concluded that power and utility companies and similar operations working along highway and road construction work zones, should follow these guidelines:
- Employers should use positive protective barriers to shield workers from intruding vehicles.
- Use an audible warning/alarm system to alert workers of a work zone intrusion or other emergency.
- Use portable rumble strips/speed bumps on roadways to warn motorists of highway construction work zones.
- Use law enforcement vehicles and personnel to help alert vehicle traffic to highway work zones.
- Develop and utilize both “Traffic Control Plans” and “Internal Traffic Safety Plans” for each highway and road work zone project.
- All highway and road construction projects must meet or exceed MUTCD guidelines and must follow all State, County and Municipality requirements for traffic control, set up, and application.
INTRODUCTION
On August 8, 2000, the Washington State FACE Program was notified by the Washington Industrial Safety Health Act* (WISHA) Services Division of the death of a 33-year-old journeyman lineman.
The Washington FACE Principle Investigator and the Field Investigator met with the regional WISHA representative who was investigating the case. After reviewing the case with WISHA, the WA FACE team traveled with the WISHA representative to the incident site. The WISHA representative helped pinpoint the incident location, the utility construction site details and defined the position of the people and equipment involved in the incident. The Washington FACE Field Investigator also met with the safety representative of the public utility whose employees were involved in this incident.
The incident site was located at the “T” intersection of two rural county roads (Figure 1 roads A and B). Both roads were two-lane asphalt-surfaced arterials with moderate traffic flow. Figure 1 shows the road layout with respect to the work zone, the incident site, and the travel path of the intruding vehicle. Flaggers were located west (flagger #1) and east (flagger #2) of the work site along road A. Flagger #2 was positioned along road A and would help direct traffic that would be traveling north and south on road B. Both flaggers were certified, as required by the state. All the utility vehicles had their flashing warning beacons on. A backhoe was also being used in the work area to help in the installation, set up, and positioning of the power pole.
The county public utility had a very active and better than average safety program in place, based on the review by the FACE Field Investigator. The county utility had a full-time safety and health person. (The safety person was not at the site at the time of the incident.) The company also had a health and safety committee that met on a monthly basis. Job site crew and supervisors met prior to the start of each workday to discuss the work to be done that day and related safety issues. The county utility had been in existence for over 78 years and had approximately 650 employees working for them in the county.
The fatal victim, at the time of the incident, was working as part of a six-person crew on the utility pole installation project. He had worked for the utility company for a little over four and a half years and was a journeyman lineman. On the afternoon of July 25, 2000, the fatal victim was struck and killed and a second utility employee injured by an intruding motor vehicle that drove through the work zone. The driver of the intruding vehicle was charged with “driving under the influence” and vehicular homicide.
INVESTIGATION
On July 25, 2000, a Tuesday morning, a county public utilities work crew began work preparing to frame and install electric power poles along a section of a rural county road, in central Washington State. The work crew started their shift at approximately 7:00 AM that morning. The crew consisted of two journeyman linemen (the fatal victim and the injured co-worker), one apprentice lineman, two flaggers and one line foreman. The line foreman held a brief safety meeting and project work plan review at the beginning of the shift.
At the end of their safety meeting/work briefing, the flaggers were sent out to the work sites to prepare and set up the highway warning signs prior to the utility work team’s arrival. The line foreman and the remainder of the crew went to a nearby county utility facility to pick up materials and a trailer to take to the work site. They planned to complete the first pole installation in the morning and then the second installation (the fatal site) in the afternoon.
At the incident site, it was identified by WISHA and the Sheriff’s Department that construction work signs and other traffic control devices had been set up to meet Manual on Uniform Traffic Control Devices (MUTCD)1 guidelines as well as the Washington State Department of Transportation guidelines2. The site layout is shown in Figures 1 and 2.
The flaggers were equipped with two-way radios but the victims did not have radios. All the employees wore appropriate vests and hard hats for protection and visibility. The area where the workers were struck was about 45 feet from road A. With the work vehicles positioned along the roadway, the workers’ visibility of highway vehicle traffic was limited. Because the curve in road A west of the site was gradual in nature (Photograph 1), the flagger was easily visible to the motorist as the vehicles were at the apex of the curve and traveling toward the work zone. The speed limit for road A was posted at 40 mph and the weather that afternoon was clear and dry with temperatures in the mid to high 80’s (°F).
At approximately 2:00 PM, the utility crew was in the middle of setting up to attach the frame onto the new power pole. At that time, a mid-size passenger vehicle (1977 Oldsmobile Cutlass 4-door sedan) was traveling east on road A.
Flagger #1 saw the vehicle approaching at approximately 30-35 mph. The flagger, using his stop sign paddle, signaled the motorist to stop. The flagger noted that it appeared that the motorist was not responding to his stop sign. The flagger then began waving the stop paddle very emphatically in rapid motion to get the motorist’s attention, which did not work. The flagger then jabbed the stop paddle into the traffic lane trying to get the driver’s attention.
The driver still did not stop or slow down. After passing the flagger’s station, the driver swerved his vehicle into the opposing lane, left the roadway just in front of a utility truck, crossed a 2 ft deep drainage ditch and entered the work area off of the roadway (Photographs 2 and 3). He then struck and crushed a telephone box and part of the new telephone pole that was being prepared for installation. The pole was suspended from one end by a backhoe and was in the process of having its frame attached by the victims. The vehicle struck the pole at a slight angle, drove under the elevated section of the pole, struck a portion of the frame that was being installed and continued without a reduction of speed (per witnesses) toward the victims. One flagger had yelled “CAR!, CAR!” and the other yelled, “LOOK OUT!” to try to warn the linemen, but neither warning were effective.
The fatal victim was struck by the left front of the vehicle, then hit the windshield and was thrown over the top of the vehicle as it exited the work zone. The victim landed and struck his head on the asphalt of the southbound lane of road B. The injured co-worker was struck almost simultaneously by the intruding vehicle and was thrown about 10 to 15 feet to the left of the vehicle, landing on his back near the backhoe being used by the utility crew. After striking the two victims, the vehicle followed the path shown in Figure 1 and finally came to a stop after striking a large rock. Witnesses indicated that it appeared that at no point did the operator of the vehicle attempt to slow down or stop until his final impact with the rock.
A witness/motorist who had stopped at the direction of flagger #1 called 911 and requested medical assistance. First-aid assistance was given to the two victims by members of the utility work crew while waiting for medical emergency personnel. When the medical emergency team arrived, they found that one of the injured linemen had minor injuries consisting of bruises to his legs. He was transported to the hospital, treated and released. The second victim was in critical condition with multiple severe injuries, and was transported to a local hospital then airlifted to a trauma center later that day and placed on life support. This victim died from his injuries 10 days later on August 4, 2000.
CAUSE OF DEATH
The medical examiner listed the cause of death as cerebral contusions due to, or as a consequence of blunt force injury of the head.
RECOMMENDATIONS/DISCUSSION
Recommendation #1: Employers should use positive protective barriers to shield workers from intruding vehicles.
Discussion: The work site was set up to try to meet MUTCD guidelines for a two-lane highway with an intersecting secondary road. The work crew used standard and generally good safety practices and precautions. Even with these standard precautions in place, a vehicle entered the work zone and struck two workers, injuring one and killing the other.
The intruding vehicle did not appear to respond to the warning signs, emphatic directions from the flagger, traffic cones, flashing yellow warning beacons on the utility trucks, or the trucks themselves.
To prevent death and serious injury in utility power pole installation, employers should use positive protective barriers to shield workers from intruding vehicles. Cones and other delineating devices can be useful in defining the proper traffic lanes from the work zone, but they provide little to no physical protection to the workers from an intruding vehicle that enters the work zone. This is especially true with an impaired driver, as discussed in this incident report. An impaired driver may not perceive visual delineation devices, but a well designed positive protective barrier can be effective to prevent vehicle intrusion.
Approved barricades, such as the concrete “jersey-type” barricades provide positive protection by helping prevent vehicles from leaving designated traffic lanes and striking workers within the work zones. Using “jersey-type” barriers requires a little more planning and set up time, and employers also need to have the right equipment available to place and remove the barriers, but they can be well worth the time, effort and cost, because of their life saving potential.
There are other types of positive protective barriers available, such as water fillable plastic/composite barriers and barrels (an alternative to the concrete barriers), transportable guard rail systems, and work zone nets.
The utility crew already had equipment at this location that could handle the placement of concrete barriers. The other types of barriers mentioned above are more easily transported to the site without heavy lift equipment and could be filled on-site. The utility’s trucks could also have been situated in a different arrangement to provide a more efficient barrier.
Recommendation #2: Use an audible warning alarm system to alert workers of a work zone intrusion or other emergency.
Discussion: According to the National Research Council, Strategic Highway Research Program,3 many highway/road work zone incidents, injuries and deaths occur when vehicles fail to recognize and follow work zone traffic control mechanisms including traffic management direction by flaggers. Vehicles drive into closed lanes, through work zone tapers and into work zones. These drivers often do not slow down and fail to control their vehicles.
Many workers are killed and injured by intruding vehicles because workers had little warning to alert them of a vehicle entering their workspace. Audible warning alarm systems may alert workers of a work zone intrusion or other emergency. There are many types of these devices. Some can fit on the staff of the stop/slow paddles used by flaggers, while others are automatic work zone intrusion alarms that are strategically placed along the work zone.
The stop/slow paddle device is triggered by the flagger to warn workers of an intruding vehicle or other hazard. One manufacturer indicates that their device is in use in 22 states and is MUTCD compliant. There are also many types of automated intrusion warning devices available that are designed to warn workers when a vehicle has entered a restricted area of the work zone. Examples of these types of warning devices can be found in the National Work Zone Safety Information Clearinghouse.4
In this situation, with the intruding vehicle traveling at between 30-35 mph, it would take approximately 3 seconds to travel from the flagger to the work zone. If an adequate warning system had been in place, there may have been time to warn the workers and have them take evasive action and not be struck by the vehicle.
Recommendation #3: Use portable rumble strips/speed bumps on roadways to warn motorists of highway construction work zones.
Discussion: In order to enhance the ability of drivers to recognize the need to slow down for work zones we recommend that employers consider the use of portable rumble strips/speed bumps on roadways to warn motorists of highway construction zones. There are a variety of products on the market that can provide not only visual information for a driver to slow down but also audible and tactile input.
One such product that is currently under review by the Federal Highway Administration (FHWA) and the California Department of Transportation (CALTRANS) is the Advanced Traffic Warning System (ATWS).5 These rumble strip mats are lightweight; durable; highly reflective; resistant to water, grease, and snow; and can be folded for ease of transportation. Warning signs should be used in advance of the rumble strips.
Recommendation #4: Use law enforcement vehicles and personnel to help alert vehicle traffic to highway work zones.
Discussion: Motorists may not slow down for a road construction work zone, but they do recognize law enforcement authorities. Drivers will usually slow down as they travel past the work zone as the result of law enforcement presence and potential consequences of not driving through the area cautiously.
Law enforcement officers’ vehicles are one of the most effective visual warnings methods used at highway work zones. Drivers will slow down when they see the flashing lights of a patrol car.6
Recommendation #5: Develop and utilize both “Traffic Control Plans” and “Internal Traffic Safety Plans” for each highway and road work zone project.
Discussion: There are both external and internal hazards that need to be addressed when trying to manage a safe and productive work zone. Therefore, it is recommended that both “Traffic Control Plans” and “Internal Traffic Safety Plans” be developed and utilized for work zone projects.
A “Traffic Control Plan” (TCP) primarily addresses traffic controls to be used to facilitate safe passage of pedestrian and non-construction vehicles through the temporary highway and road construction work areas.
The “Internal Traffic Safety Plan” (ITSP) defines processes and procedures for worker safety within the work zone. The elements of the ITSP should indicate where and how construction equipment, vehicles, and workers on foot interact within the work zone. The plan must also take into consideration the changing aspects of a work site and possible emergency situations such as an intruding vehicle.
A plan of action should be part of the project process that anticipates vehicles intruding into the work space and incorporates protective and preventive measures through the use of positive protection barriers, warning systems, and processes and procedures to make for an injury free and productive work zone project.
It is important that the safety plan be clearly understood by all workers. The plan should define the work areas, hazards, and potential emergency situations relating to the construction work zone. Good planning is important to managing a safe operation.
Recommendation #6: All highway and road construction projects must meet or exceed MUTCD guidelines and must follow all State, County and Municipality requirements for traffic control, set up, and application.
Discussion: At the time of the incident, a new WISHA rule required the work zone to have at least 3 signs prior to the physical location of the flagger. The former requirement was for 2 warning signs (see Figure 2), as used in this work zone. In Washington State, if the Washington Administrative Codes (WAC) have more stringent rules for work zones than the MUTCD, then the WAC requirements take precedence over MUTCD guidelines.
Because of the level of hazards and exposures associated with highway work zones, extra effort needs be taken to ensure the safety of those in the work zone and the traveling public. “Typical Applications” # 10 and # 22, from the MUTCD,1 should have been used for reference in designing traffic control for this work zone.
The signage for the work zone could have been improved by having the following four signs:
- Utility work ahead,
- One lane ahead,
- Flagger ahead, and
- Prepare to stop.
Also more traffic cones or barrels in the down stream and shifting taper could have been used. This would have made the work zone more visible to eastbound traffic. The employer could also have set up “lane separating” channeling devices around the work zone to give the work zone more definition and make it more visible to drivers along the restricted area of the roadway
NOTE: All departures from normal procedures as stated in the MUTCD should be investigated with the appropriate local, state, or federal agency. |
ACKNOWLEDGEMENTS
In conducting the Utility Work Zone Fatality Investigation, the Washington State FACE Investigation Program requested that the contents of this report be reviewed by key representatives from labor and the utility industry, private consultants and Washington State and Federal agencies, prior to it’s publication.
Though we are not able to acknowledge specific individuals for their invaluable input into this document, we would like to recognize the following for their help and support to the FACE process:
- The Employer involved in the incident
- WISHA enforcement
- WISHA policy & technical services staff
- Federal Face Program Management (NIOSH)
- Safety & Health Assessment & Research for Prevention (SHARP)
- Labor
- Utility company
- IBEW/NECA JATC
- Washington State Attorney Generals Office
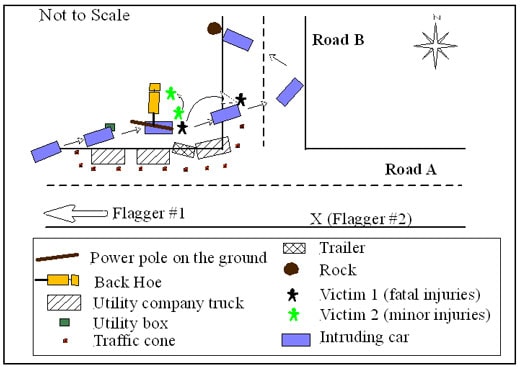
Figure 1. Layout of the incident.
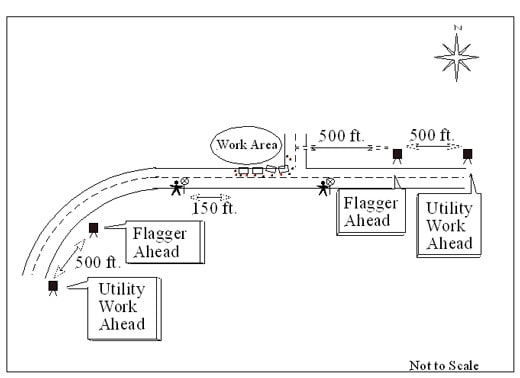
Figure 2. Layout of the work zone.
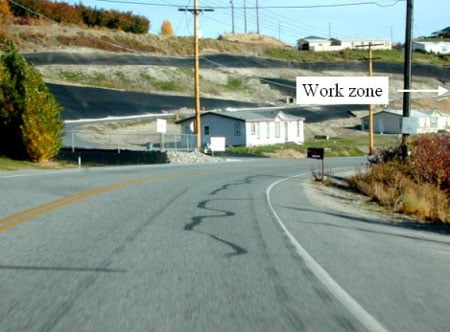
Photograph 1. View approaching the work zone from the south
(direction from which the intruding vehicle approached).
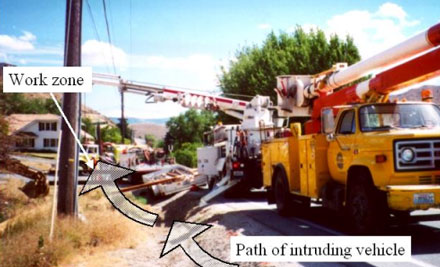
Photograph 2. The work zone.
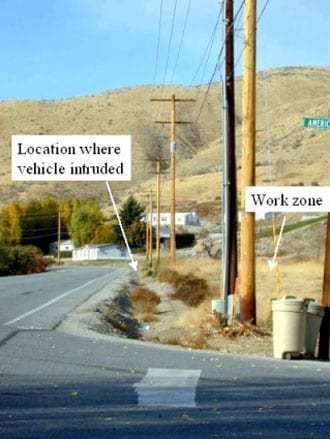
Photograph 3. The location of the work
zone, after the incident.
* The OSHA State Plan program in Washington State.
REFERENCES
- Manual on Uniform Traffic Control Devices (MUTCD) 2000, Millennium Edition, Part 6 Temporary Traffic Control, U.S. Department of Transportation, Federal Highway Administration, Office of Transportation Operations, HOTO, Room 3408, Washington, DC 20590. URL: http://mutcd.fhwa.dot.gov/external icon
- Work Zone Traffic Control Guidelines. M54-44, Washington State Department of Transportation, Field Operations Support Center, May 2000.
- Graham, Jerry L., Hinch, John, Stout, Dale, Lerner, Neil, Maintenance Work Zone Safety. Washington, DC: National Research Council, Strategic Highway Research Program, 1990.
- National Work Zone Safety Information Clearinghouse, http://wzsafety.tamu.edu/external icon
- Frenceschi, C. Tere. Portable Speed Bumps Keeps a Safe Work Zone Around Flaggers. Research & Technology Transporter, U.S. Department of Transportation, Federal Highway Administration, February 2002.
- Effectiveness of Law Enforcement in Reducing Vehicle Speeds in Work Zones. Office of Construction, Construction Programs Section, Minnesota Department of Transportation, January 1999.
OTHER RESOURCES
- Employee Protection in Public Work Areas, Chapter 296- 45-52530 WAC, State of Washington, Department of Labor and Industries.
- Pratt, Stephanie G., Fosbroke, David E., Marsh, Suzanne M. Building Safer Highway Work Zones: Measures to Prevent Worker Injuries From Vehicles and Equipment. Cincinnati, OH. National Institute for Occupational Safety and Health, April 2001.
- Highway Work Zone Safety. Washington State Department of Transportation, January 1994.
To contact Washington State FACE program personnel regarding State-based FACE reports, please use information listed on the Contact Sheet on the NIOSH FACE web site Please contact In-house FACE program personnel regarding In-house FACE reports and to gain assistance when State-FACE program personnel cannot be reached.
Back to Washington FACE reports
Back to NIOSH FACE Web