Youth Landscaper Pinned Underneath Front End Loader
January 25, 2002
Nebraska FACE Investigation 01NE026
SUMMARY:
A 16-year-old landscaper was killed when the front end loader he was operating overturned pinning him underneath. The victim and his supervisor had just completed trimming and removing some trees from a residential property. They were returning equipment back to their storage yard. The supervisor, driving a dump truck, left a few minutes before the victim. The victim was supposed to follow the supervisor with the front end loader, but for unknown reasons, went in the opposite direction. Several blocks from the job site he started down an inclined roadway, veered slightly to the right side striking a concrete curb, which caused the loader to turn sharply to the left. The victim attempted to correct the loader by turning the steering wheel, but the loader did a three-quarter roll. The victim was pinned under the driver’s side front drive wheel. He was pronounced dead at the scene. There was no rollover protective structure (ROPS) on the loader.
The Nebraska Workforce Development, Department of Labor’s Investigator concluded that to prevent future similar occurrences:
- Employers should ensure all safety devices, such as ROPS and seat belts are installed and maintained on all applicable equipment.
- Employers should ensure that all equipment has an established maintenance program as recommended by the manufacturer.
- Employers should ensure that all employees are provided written, verbal and hands-on training for each piece of equipment they will work with prior to operating such.
- Employers and/or supervisors should ensure that task specific verbal and/or written guidance is provided to all employees to ensure they are knowledgeable of their task responsibilities.
- Employers should understand and follow all applicable federal and state laws pertaining to child labor requirements.
PROGRAM OBJECTIVE:
The goal of the Fatality Assessment and Control Evaluation (FACE) workplace investigation is to prevent work-related deaths or injuries in the future by a study of the working environment, the worker, the task the worker was performing, the tools the worker was using, and the role of management in controlling how these factors interact.
This report is generated and distributed solely for the purpose of providing current, relevant education to employers, their employees and the community on methods to prevent occupational fatalities and injuries.
INTRODUCTION:
On July 17, 2001 at approximately 11:30 a.m., a 16-year-old landscaper died after the front end loader he was operating tipped over, pinning him under the operator’s side front drive wheel. The Nebraska Department of Labor was notified of the fatality the same day by the Occupational Safety and Health Administration (OSHA). The Nebraska FACE Investigator met with the investigating OSHA Compliance Officer (COSHA), company officials and employees, and county and local law enforcement personnel at the mishap location on July 18, 2001. On July 27, 2001 and January 8, 2002 the FACE investigator again met with the COSHA to review incident site photos and to discuss particular facts of the mishap.
The employer is a landscaping company that works primarily on residential areas. They have been in business as a registered landscaping company since May 6, 2001 when the employer bought out another landscaping company (including the equipment involved in the mishap). The employer had previously performed this service for two years with employees, and as a tree planter for five years before that by himself. At the time of the mishap there were five employees. The company does not have a written safety program. Tailgate talks were sometimes conducted, but none were documented. Any training given to employees was done verbally and “hands-on” with no documentation. The employer has no previous history of fatalities.
INVESTIGATION:
Victim: The victim was a 16-year-old male. He had been employed by this company since early May, only approximately one and a half months prior to the mishap. He was hired to perform “gopher” type duties, such as clean up, etc. He was assigned to the tree crew. This normally consisted of the victim and a supervisor.
Training: No pre-job formal training on the mishap equipment could be established. Upon hire, the victim was given the same “hands-on” training as the other employees. This consisted of the supervisor showing the victim the control levers (see photos #7 & #8), then allowing the victim to practice moving logs around in the yard. The victim had operated the loader on several other occasions as witnessed and stated by the owner, supervisor and other employees interviewed. The supervisor had worked for the equipment’s prior owner for five years, but stated he had not had any formal training operating the equipment either. All employees, except the employee most recently hired two weeks before the mishap, had received this same “hands-on” training. There was no equipment manual available.
Equipment: The equipment involved in the incident was a Massey Ferguson MF 11 Front Wheel Drive Loader (see photos #5 & #6). It is powered by a Perkins A4-238 four cylinder diesel engine that supplies power via the transmission and torque converter to the front wheels.
Forward or reverse motion is selected by depressing the appropriate throttle pedal. These two pedals are located on the floor, upper right hand corner beside one another (see photo #7). Each has a molded arrow to indicate which direction they operate. The operator presses the left pedal for reverse and the right pedal for forward. Either pedal operates the fuel pump before it engages the appropriate set of clutches.
It has full power steering on the left side rear wheel only, the other wheel is moved by a connecting tie rod.
Brakes: The loader is fitted with a dual brake system on the front axle (drive wheels), having a pair of hydraulically operated disc brakes for normal use and a pair of mechanically operated wheel drum brakes for parking. Each disc brake is a fully enclosed, six plate, oil immersed unit operated by hydraulic fluid drawn from a reservoir situated at the floor level on the operator’s left hand side. Each drum brake is a 14″ x 2″, two shoe, double acting, floating cam unit and is mechanically operated by a foot pedal. When depressed, this hydraulically operates the fully enclosed disc brakes. The foot pedal is located to the left side of the throttle pedals (see photo #7). The parking brake pedal is located on the left hand side of the operator’s seat (see photos #7 & #8).
The gear shift lever is situated at the lower left hand side of the operator (see photos #7 & #8). It operates a range of two gears. It moves down for the first gear and up for the second gear. When the lever is in the central position it is in neutral. Note: pictures taken immediately after the mishap indicated this lever was in second gear. The dual range selector lever is situated at the lower left hand side of the operator, next to the gear shift lever (see photo #8). The lever moves up for high range and down for low range. When the lever is in the central position it is in neutral. Note: pictures taken immediately after the mishap indicated this lever was in the high range. The overall dimensions for the loader are approximately 87″ high without a cab, 183″ long with bucket and 82″ wide.
Wheels/Tires: The front drive wheels are larger than the rear-steer wheels (see photos #5 & #6). The loader was originally equipped with 17.50 x 25 tires on the front and 9.00 x 20 tires on the rear. Due to the condition of the tires the investigator could not make out the sizes presently used. The front tires (drive) were worn down considerably (see photos #9 & #10). The rear tires (steering) had very little tread remaining. Both rear tires had chunks missing from the sides of the tread area (see photos #12 & #14). On the left rear tire there were 2 of 8 lug nuts missing (see photo #11). The lug bolts were rusty, indicating they had been gone for some time. The right rear tire was worn at an angle starting approximately in the middle of the tread area, sloping to the outside (see photos #6 & #14). Out of 8 lugs, one lug bolt and an additional lug nut were gone (see photo #13). Again, the bolt and empty hole were rusted over.
The investigator was able to make contact with an equipment service company that formerly sold and serviced this type of unit. They were able to provide an Operator’s Manual for this machine, and also using the serial number determine within a six-month window the date of manufacture, between late 1971 and early 1972. All units manufactured did come with either a full cab or a four point bar system that served as a Rollover Protective System (ROPS). Holes on the main body of the loader did indicate that this had been removed prior to the present owner purchasing it. As of the incident date there was no established and/or documented routine maintenance program for this specific piece of equipment.
Analysis/Synopsis: On the morning of the accident the victim and his supervisor were assigned the task of removing several trees from a residential yard. They met at the company’s storage yard to gather the necessary tools and equipment. The victim drove the front end loader, while the supervisor drove a 1978 C65 dump truck. The route they took (1.4 miles) to the job site went by the company owner’s house, and was the route they intended to return on. They arrived at the job site at approximately 10:00 and proceeded to remove the trees. At approximately 11:20 the supervisor told the victim to finish raking up the leaves, then bring the front end loader back to the storage yard. The supervisor left the job site and stopped en-route at the owner’s house to pick up some more equipment. After approximately 15 minutes the owner mentioned that the victim should have driven by, so the supervisor went back to the job site. When he didn’t find the victim, he returned to the storage yard.
After raking up the remaining leaves the victim drove the loader in the opposite direction from which they had arrived. After traveling 1.09 miles, the street makes an abrupt right hand turn before going down a hill. The supervisor stated that the victim may have went in that direction to see some of his friends that live near the top of the hill but that could not be confirmed. The hill has an approximate 10 degree grade for approximately 200 feet. It is a two lane asphalt road and was dry at the time. When the victim was approximately 140 feet down the hill, for reasons unknown, the loader veered to the right, causing the front right drive wheel to strike the concrete curbing. Rubber skid and drag marks indicate that the loader then turned sharply to the left and began to roll over. A witness that was at the bottom of the hill said the loader was going “very fast” and that it appeared almost as if it was going to make a U-turn. The witness said as the loader began to roll the victim was “really turning the wheel”. The loader continued to make a ¾ roll, landing on its side . It is not known if the victim was thrown from the loader.
The witness ran to the scene and attempted to help the victim. When she saw that the victim was pinned, she ran to an adjoining house to call for assistance. The residents were in the back yard and had heard the noise from the wreck and called 911. Local law enforcement personnel arrived within a minute and found the victim trapped under the loader’s front left drive wheel. The loader was still running. The kill switch was located and the machine was shut off. Rescue personnel arrived within two minutes but were not able to find any life signs. The County Attorney pronounced the victim dead at the scene.
CAUSE OF DEATH:
Compression asphyxia
RECOMMENDATIONS/DISCUSSION:
Recommendation #1: Employers should ensure all safety devices, such as ROPS and seat belts are installed and maintained on all applicable equipment.
Discussion: The equipment involved in the accident had been purchased a few weeks before from another landscaping company, along with other pieces of equipment. When the mishap equipment was bought, it did not have the factory-equipped cab or four-point bar systems that served as rollover protection (ROPS). It is unknown when they were removed. If the ROPS and seat belt restraint system had still been in place and utilized, it is unlikely the victim would have been crushed.
Recommendation #2: Employers should establish regularly scheduled maintenance programs for all pieces of equipment.
Discussion: Since its purchase, no maintenance schedule had been established on this piece of equipment. No Owners Manual was received during purchase, which specifically lists the maintenance requirements for each equipment component including brakes and tires. The poor condition of the rear steer tires may have contributed to the loss of control experienced by the victim, allowing the equipment to veer to the right.
Recommendation #3: Employers should ensure that all employees are provided written, verbal and hands-on training by a competent person1 for each piece of equipment they will work with prior to operating such.
Discussion: All employees should be trained on all equipment they are expected to utilize in performance of their tasks. Training should consist of written, verbal and hands-on task evaluation. The company did not have a copy of the Owners Manual for training/maintenance use. These manuals are available from the equipment distributors and can be used as part of the training program. There is a section that covers operating the equipment on hills and slopes. It is very specific on throttle placement and pedal control.
Recommendation #4: Employers and/or supervisors should ensure that task specific verbal and/or written guidance is provided to all employees to ensure they are knowledgeable of their task responsibilities.
Discussion: Verbal instruction was given to the victim on the incident day pertaining to the job task, but not on which route to return on. The route used to access the work site does not have a hill with that much slope. If the employer and/or supervisor had been specific concerning the return route of travel, the incident may not have occurred.
Recommendation #5: Employers should understand and follow all applicable federal and state laws pertaining to child labor requirements.
Discussion: The Fair Labor Standards Act (FLSA) sets wage, hour, and employment standards that affect most workers in the United States, including youth. The standards affecting young workers vary for different age groups and for farm and non-farm work. In nonagricultural occupations, if you are 16 or 17-years-old, you may work in any occupation except those declared hazardous by the Secretary of Labor. There are 17 Hazardous Occupations Orders for non-farm work. Therefore, a 16-year-old youth may not be employed at a job that involves:
#2. Driving a motor vehicle
#7. Power-driven hoisting apparatus.
(Fair Labor Standards Act, Hazardous Occupations Orders, WH-1330, Revised September 1991)
ATTACHMENTS:
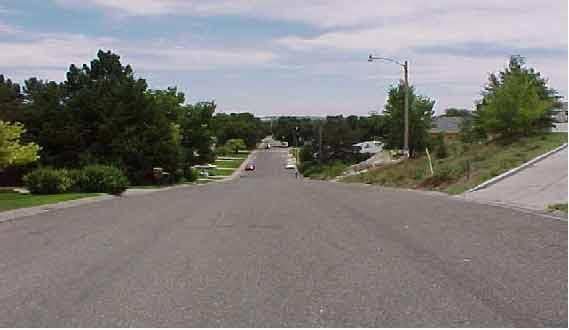
Photo #1: Looking south down the hill.
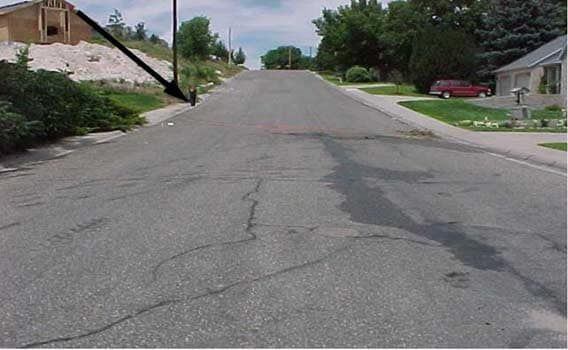
Photo #2: Looking north up the hill. Arrow indicates where equipment struck the cement curb.
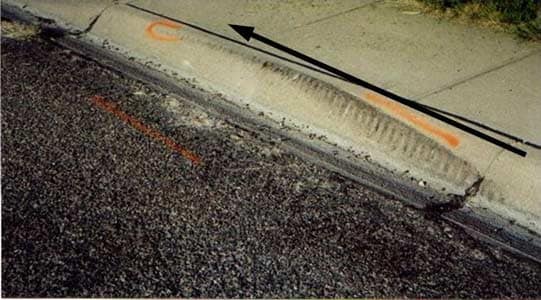
Photo #3: These are skid marks left when the machine veered to the right, striking the concrete curb. Arrow notes direction of equipment travel.
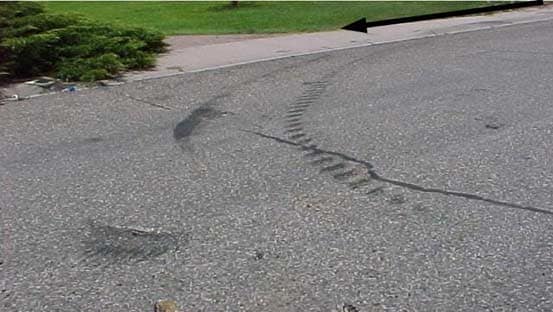
Photo #4. Tire skid marks left after equipment contacted concrete curve and veered to the left, before completeing a ¾ roll. Arrow notes direction of equipment travel.
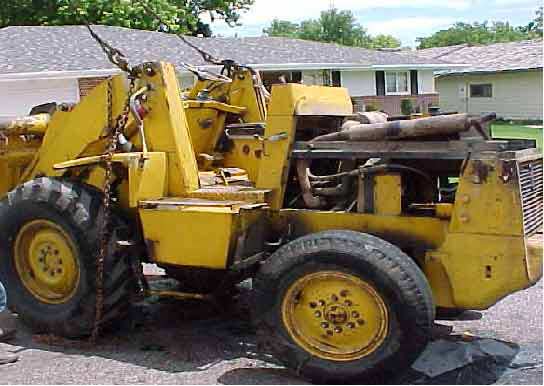
Photo #5: Left side view of equipment.
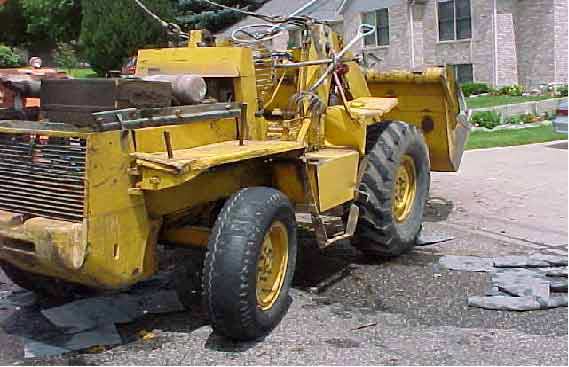
Photo #6: Right side view of equipment.
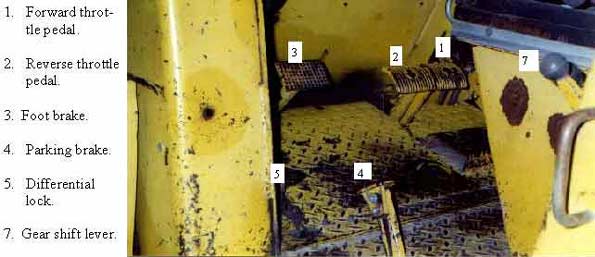
Photo #7: Interior view of forward/reverse throttles, foot brake, parking brake and differential lock.
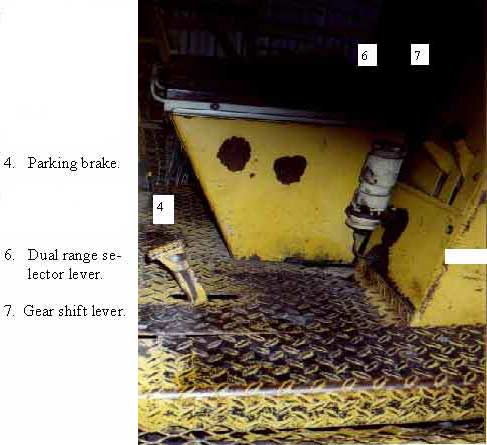
Photo #8: Shows position of dual range selector lever and gear shift lever.
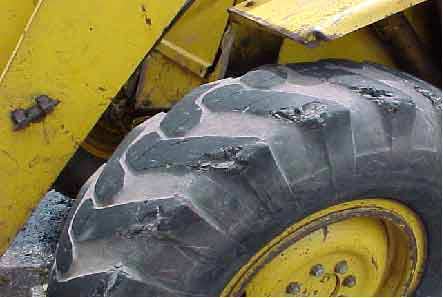
Photo #9: Left front-drive tire. Note missing tread and chunks of rubber.
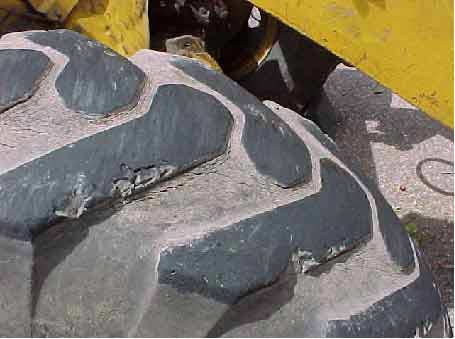
Photo #10: Right front-drive tire. Note missing tread and chunks of rubber.
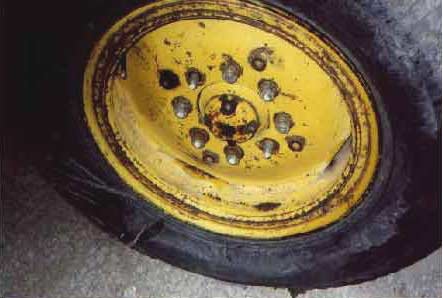
Photo #11: Left rear-steering wheel with two missing lug nuts.

Photo #12: Left rear-steer whieel. Note the large chunk of rubber and most tread missing.
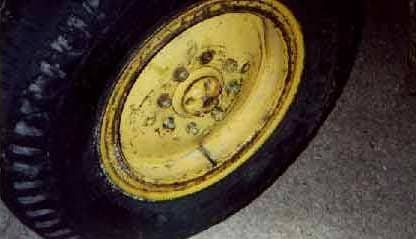
Photo #13: Right rear-steer tire showing missing lug bolt and lug nut.
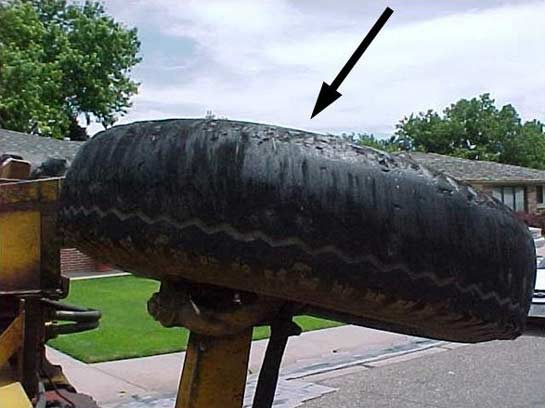
Photo #14: Right rear-steer tire showing missing tread and chunks of rubber missing from outside of tire.
1 – Competent Person – A person who, because of training and experience, is capable of identifying hazardous or dangerous conditions and of training employees to identify such conditions.
To contact Nebraska State FACE program personnel regarding State-based FACE reports, please use information listed on the Contact Sheet on the NIOSH FACE web site. Please contact In-house FACE program personnel regarding In-house FACE reports and to gain assistance when State-FACE program personnel cannot be reached.