Operator Dies After Being Crushed Inside A Side-loading Waste-Hauling Truck
MN FACE Investigation 96MN08001
DATE: February 24, 1997
SUMMARY
A 29-year-old truck driver died of injuries he sustained when the compactor plate (platen) component of the side-loading waste-hauling truck he was cleaning engaged and crushed him. The truck was running at the time of the incident and the controls that operated the platen were in the automatic mode. The victim was leaning inside the sump area of the truck when the platen engaged. When the platen returned to its resting position it crushed the victim. The victim’s coworkers performed cardiopulmonary resuscitation on him and placed a 911 call to emergency rescue personnel who arrived and pronounced the victim dead. MN FACE investigators concluded that, in order to reduce the likelihood of similar occurrences, the following guidelines should be followed:
- employers should ensure that workers perform maintenance on equipment only when it is not operating; and
- employers should design, develop, and implement a comprehensive safety program.
INTRODUCTION
On November 12, 1996, MN FACE investigators were notified of a work-related fatal incident that occurred on November 12, 1996. An interview with the employer’s director of safety was conducted by a MN FACE investigator on January 31, 1997. During MN FACE investigations, incident information is obtained from a variety of sources such as law enforcement agencies, county coroners and medical examiners, employers, coworkers and family members.
The victim worked for a waste-hauling company that has been in business for 11 years and employs 100 workers. The employer has a safety program and a safety director who dedicates 100% of his work time to health and safety. The victim had worked for the company for 20 months.
INVESTIGATION
The victim operated a side-loading waste-hauling truck that was used for the collection of garbage from residential and commercial sites. Garbage is deposited into a hopper area that is located in the mid-section of the truck. When the hopper is full, a hydraulically controlled platen or ram compacts garbage into the truck’s holding area. The truck has a selectable switch that the operator uses to select either an automatic or a manual mode for compaction of garbage into the holding area or removal of garbage from the truck.
The manual mode is used to fully extend the platen and expel garbage from the holding area at a disposal site (Figure 1). It may also be used when the holding area is nearing full capacity because it allows the platen to compact garbage deeper into the holding area. After the operator selects the manual mode, a manual control lever is pulled to activate the hydraulic system that moves the platen. In the automatic mode, the operator pushes a “platen cycle” button, which causes hydraulic cylinders to push the platen to compact garbage into the holding area of the truck. The platen then returns to its resting position (Figure 2) after completing the compaction process and allows the operator to refill the hopper. When the automatic mode is selected during routine operation, pneumatic “air” pressure prevents operation of the manual control lever. However, before adequate air pressure is established when the trucks are started each day, the manual control lever can be operated even when the system is in the automatic mode.
On the day of the incident, the victim was working in the yard of the business where the waste-hauling trucks were parked. He started the truck’s engine before he began cleaning and preparing it for the days rounds. The truck’s hydraulic and pneumatic systems were driven by a “live” power-take-off shaft when the engine was running and could only be shut down by stopping the engine. The compaction unit was in the automatic mode, however, because the truck was cold and had not yet built up adequate air pressure, the victim was able to operate the manual control lever and move the platen to the fully extended position. With the platen fully extended the victim was able to access the sump area of the truck through an opening that was 36-40 inches wide. He leaned over into the hopper and began to remove garbage from the sump area while the truck was running. Since the selectable switch was in the automatic compaction mode, when adequate air pressure developed in the system as the truck was running, the system’s pneumatic cylinders activated and in turn operated the hydraulic control valves. The platen returned to its resting position in approximately three seconds and crushed the victim. A coworker pushed the emergency stop button which allowed him to move the platen away from the victim and remove the victim from the truck. A 911 call was placed to emergency rescue personnel. The victim’s coworkers performed cardiopulmonary resuscitation until emergency rescue workers responded several minutes after being called and pronounced him dead.
CAUSE OF DEATH
The cause of death listed on the death certificate was transected aorta. The toxicology findings screened positive for a drug.
RECOMMENDATIONS/DISCUSSION
Recommendation #1: Employers should ensure that workers perform maintenance on equipment only when it is not operating.
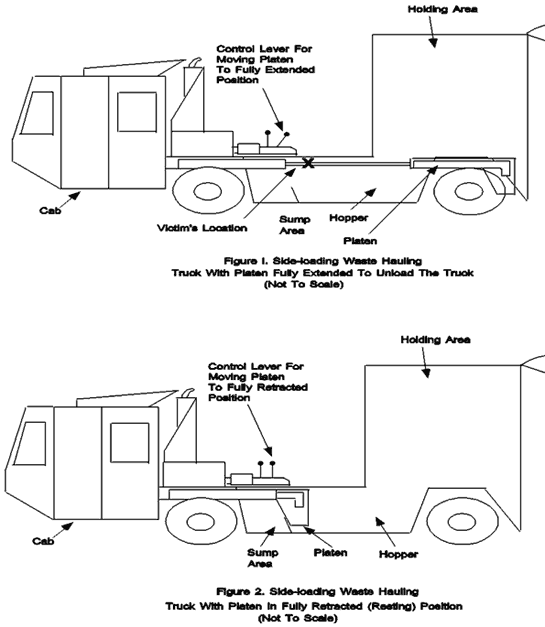
Discussion: The victim was cleaning the sump area of the waste-hauling truck while the engine was running when the platen engaged. The platen engaged because the controls that operated the compaction unit were left in the automatic mode and the truck was running. The low air pressure in the truck, due to it not being warmed up, allowed the victim to fully extend the platen while the compaction unit was in the automatic mode. In the automatic mode the platen automatically returns to its resting position after compacting garbage into the holding area. If the compaction unit is placed in the manual mode and the truck is shut off, there is no residual pressure left in the hydraulic cylinders that would cause the platen to return to its resting position from the fully extended position. If the controls that operated the platen had been in the manual mode, and the truck and been shut off, the platen would not have returned to its resting position and this fatality would have been prevented. Although the truck engine could have been stopped in this case, some equipment may need to be operating during maintenance activities. In those cases, employers should ensure that the equipment is placed in the proper mode of operation before maintenance is performed.
Recommendation #2: Employers should design, develop, and implement a comprehensive safety program.
Discussion: Employers should ensure that all employees are trained to recognize and avoid hazardous work conditions. A comprehensive safety program should address all aspects of safety related to specific tasks that employees are required to perform. OSHA Standard 1926.21(b)(2) requires employers to “instruct each employee in the recognition and avoidance of unsafe conditions and the regulations applicable to his work environment to control or eliminate any hazards or other exposure to illness or injury.” Safety rules, regulations, and procedures should include the recognition and elimination of hazards associated with tasks performed by employees.
REFERENCES
1. Office of the Federal Register: Code of Federal Regulations, Labor, 29 CFR part 1926.21 (b)(2), U.S. Department of Labor, Occupational Safety and Health Administration, Washington, D.C., July 1, 1994.
To contact Minnesota State FACE program personnel regarding State-based FACE reports, please use information listed on the Contact Sheet on the NIOSH FACE web site Please contact In-house FACE program personnel regarding In-house FACE reports and to gain assistance when State-FACE program personnel cannot be reached.