A 61-year-old Salesman Dies After Falling 10 Feet From an Operator-up High Lift Truck
Investigation: # 00-MA-70-01
Release Date: June 3, 2002
SUMMARY
On December 29, 2000, a 61-year-old male salesman was fatally injured in a 10-foot fall from an operator-up high lift truck (order picker) in a warehouse. The victim and a co-worker were working together as one of seven teams performing year-end product inventory. The victim, standing on a platform raised by an order picker, was writing down product type and quantity while the co-worker, standing in the operator’s area of the order picker, was counting product. The victim fell with the platform’s guardrail system when it became detached from the platform. A call was placed and emergency assistance arrived within minutes and transported the victim to a hospital were he was pronounced dead. The Massachusetts FACE Program concluded that to prevent similar occurrences in the future, employers should:
- perform a hazard analysis before introducing new equipment into the workplace
- provide health and safety training to employees before allowing them to perform unfamiliar warehouse tasks
- develop, implement, and enforce a comprehensive health and safety program that includes, but is not limited to, health and safety requirements for year-end inventory
INTRODUCTION
On December 29, 2000, the Massachusetts FACE Program was notified by a local fire department through the 24-hour Occupational Fatality Hotline, that on the same day a 61-year-old male was fatally injured when he fell from an order picker at a warehouse. An investigation was initiated and on February 28, 2001, the Massachusetts FACE Program Director traveled to the company’s facility where the employer was interviewed. The police report, death certificate, OSHA fatality/catastrophe report, and photographs were obtained during the course of the investigation.
The employer, a distributor of mainly food service disposable paper products, had been in business 49 years at the time of the incident. The company employed about 70 people. At the time of the incident, approximately 50 employees were on site and, of these employees, about half were inside the warehouse working with the victim. Twenty-one employees held the same job title, salesman, as the victim. The company’s health and safety program, developed approximately eight years prior to the incident, had not been updated or enforced for several years. There was no specific company representative responsible for health and safety.
The victim had been employed by the company for approximately 22 months at the time of his death and had over 30 years of experience as a salesman. He had received no job training at this company for either his usual sales responsibilities, or for the year-end inventory.
INVESTIGATION
The father of the two current owners had founded the company in the early 1950’s. The company sold food service disposable paper products, such as paper cups and containers and janitorial supplies, such as glass cleaner and other cleaning agents. These products were purchased in bulk and resold to the company’s clients in smaller quantities. The company had relocated to the incident site 90 days prior to the fatality. This location consisted of a warehouse area that was approximately 80,000 square feet and adjacent office space.
The company’s 21 salesmen traveled to clients’ facilities to get product orders. In addition, the salesmen attempted to sell new products and recruit new customers while out on the road. The company employed eight warehouse workers, four of whom worked the first shift, shelving the received bulk product. The remaining four warehouse employees worked the second shift and put orders together for the next day’s deliveries. In addition, the company also employed approximately 20 drivers who delivered product to customers.
The company’s bulk product was stored inside the warehouse on metal shelving. Each shelving section was approximately 10 feet long, 5 feet deep and 20 feet high. The sections contained three shelves, the bottom shelf was 5 feet from the floor level, the middle shelf was 10 feet from the floor level, and the top shelf was 20 feet from the floor level (Figure 1). The company had owned powered industrial trucks to store and retrieve the product to and from the shelves. These trucks consisted of one electric operator-up high lift truck (order picker) (Figure 2), three reach trucks and 10 pallet jacks. The order picker had been purchased used 13 years ago and was approximately 20 years old.
The annual inventory, the task being performed during the incident, was usually conducted at the end of the calendar year. Salesmen were required to help warehouse workers with this task which typically was scheduled on a Friday morning for three or four hours. In past years, the company had rented scissor lifts to accomplish this inventory task. This year, days prior to the inventory task, a company that was moving out of a warehouse in the same complex had given the victim’s company five platforms, which were going to be junked, that could be raised on forklift tines.
All five platforms appeared to be “homemade”. The platform involved in the fatality consisted of a wooden pallet measuring 51½ inches long by 44 inches wide by 4½ inches thick. The pallet deck was comprised of three strips of plywood 16 inches wide and ½ inch thick (Figure 3). The platform guardrail system was three sided. The back section of the platform was unguarded, except for a chain gate that appeared nonfunctional. The guardrail system consisted of three horizontal rails: The bottom rail was a flat thin piece of metal 4 inches wide and located 4 inches above the pallet deck. The middle rail was metal tubing with an external diameter of 1¼ inches located 44 inches above the pallet deck. The top rail was made of the same metal tubing as the middle rail and was located 52 inches above the pallet deck (Figure 4). Two L-shaped pieces of metal tubing were designed to slide under the deck of the pallet, in the same slots for the forklift tines. These L-shaped pieces of metal tubing connected the guardrail system to the pallet (Figure 5). In addition, eyebolt type hardware was used to help fasten the guardrail system to the pallet. The threaded section of the eyebolt was screwed into the pallet deck. The eye section of the eyebolt was bent slightly open allowing the bottom section of the guardrail system to slide into the eyebolt and re-bent closed (Figure 6).
On the day of the incident, the company was using the newly acquired platforms in combination with their powered industrial trucks to accomplish the year-end inventory task. The only way of fastening the platforms to the company’s powered industrial trucks were to slid the powered industrial truck’s tines into the platform pallet slots.
Approximately seven teams of employees were performing the year-end inventory; each team consisted of two or three workers. A team of two had been assigned to the order picker; one employee counted the boxes of product stored on the shelves while the second employee, the victim, wrote down the product number and quantity. The victim’s team member, who was counting the product, was also located inside the order picker operator’s area operating the order picker. The order picker operator area is fixed to the height of the order picker tines, therefore as the order picker tines are raised or lowered so is the operator area.
The victim and the crewmember started at the far end of the warehouse and had two rows of shelves to inventory (the shelves on either side of one aisle). Once a product was inventoried, a round sticker was placed on one of the outer boxes indicating that that product had been counted. It was reported that on approximately the 13th section, the victim, who had been standing on the floor, decided that in order to hear his coworker better he would stand on the platform. This would locate the two team members at the same height because the platform was connected to the order picker tines (previously described) which is fixed with the height of the order picker operator’s area.
At the time of the incident, the victim was standing on the platform deck, which was raised to the second shelf, 10 feet from the floor level. The victim’s team member was standing up in the metal storage rack when he heard a cracking sound. He jumped back to the operators area turned around and saw the victim and the guardrail system fall to the concrete floor below. Evidence indicates that the victim leaned against the already unstable guardrail system and that the weight of the victim’s body caused the guardrail system to tip pulling the eyebolts from the pallet. This caused the guardrail to become unattached from the platform.
Employees assisted the victim while a call was placed for emergency assistance. The local police and fire department responded to the call and the victim was transported to a hospital where he was pronounced dead.
CAUSE OF DEATH
The medical examiner listed the cause of death as multiple traumatic injuries.
RECOMMENDATIONS/DISCUSSION
Recommendation #1: Employers should perform a hazard analysis before introducing new equipment into the workplace.
Discussion: In this case, the platforms, which were going to be junked, were given to the company, and being used several days later without being evaluated. A hazard analysis should be performed before any borrowed, new, or rented equipment is incorporated into tasks. A hazard analysis should include, but not be limited to an inspection of the equipment condition, compatibility with other equipment with which it will be used, how the equipment is going to be used to complete the tasks, proper use of the equipment and in addition, contacting the equipment manufacturer. Since the platform was “homemade” Massachusetts FACE contacted the order picker manufacturer and asked about using platforms with order pickers. The manufacturer’s response was that “order pickers are not designed for this type of application”.
In this case, conducting a hazard analysis might have revealed that the guardrail system was not structurally secured to the pallet and that the order picker manufacturer had a warning sticker adhered to the order picker, which stated that it was not to be used for lifting personnel.
Recommendation #2: Employers should provide health and safety training to employees before allowing them to perform unfamiliar warehouse tasks.
Discussion: Ideally, the employer could have altered the inventory schedule and had only trained warehouse employees perform the inventory task or hired a company that specializes in warehouse product inventory. In some instances, when non-warehouse employees are needed to help with warehouse based tasks, with which they are unfamiliar, the employer, should provide health and safety training specific to the warehouse task. In this case, the salesmen were pulled once a year from their regular jobs to help perform the year-end product inventory. This was the only time the victim and other salesmen performed tasks inside the warehouse. Inexperienced in operating powered industrial trucks and other warehouse type equipment and activities, these salesmen were placed in an unfamiliar setting and asked to perform an infrequent task without warehouse specific health and safety training.
In addition, the Occupational Safety and Health Administration (OSHA) requires that all powered industrial truck operators are trained and certified in the proper and safe use of powered industrial trucks (29 CFR 1910.178). Forklifts including operator-up high lift trucks, like the one involved in this incident, are included under the powered industrial truck regulation.
Recommendation #3: Employers should develop, implement, and enforce a comprehensive health and safety program that includes, but is not limited to, health and safety requirements for year-end inventory.
Discussion: Approximately eight years prior to the incident, the employer hired an outside company to develop a health and safety program. At the time of the incident, the health and safety program, which did not include a section on warehouse based year-end inventory, had not been maintained or enforced for many years.
Development, implementation, enforcement and maintenance of a health and safety program should be done with employee input to ensure that employees participate in their own safety. For companies conducting year-end inventory, a health and safety program should include, but not be limited to, specific warehouse based year-end inventory health and safety training requirements. These training requirements should include recognition and avoidance of unsafe conditions, and written procedures for safe work practices and task completion. In this case, specific training for the salesmen should have included powered industrial truck (forklift) training and training on product storage, retrieval, and inventory in a warehouse setting. A summary of OSHA’s draft proposed safety and health program rule has been included at the end of this report.
REFERENCES
- Code of Federal Regulations, 29 CFR 1910.178 Powered Industrial Trucks, Materials Handling and Storage.
- American National Standards Institute, Safety Standard for Low Lift and High Lift Trucks, ANSI B56.1-1993, New York.
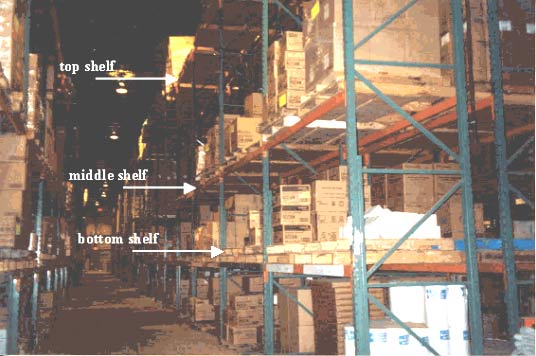
Figure 1 – Warehouse shelving, location where victim fell.
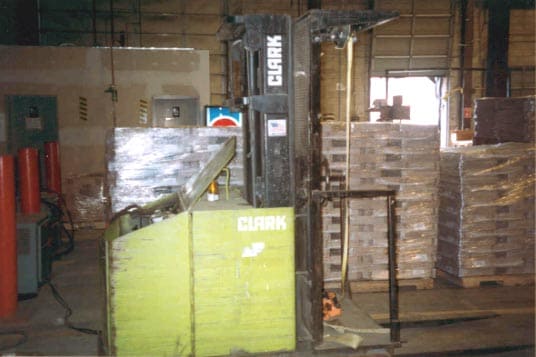
Figure 2 – Operator-up High Lift Truck (Order picker) involved in the incident.
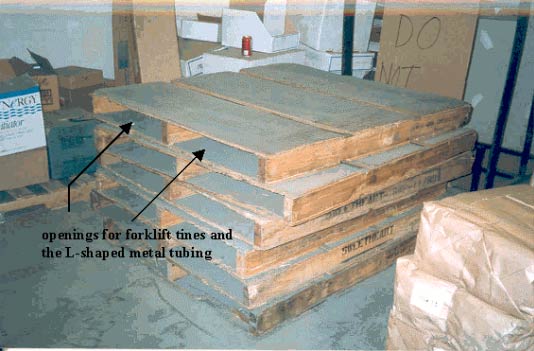
Figure 3 – Same style pallet the guardrail system was connected to.
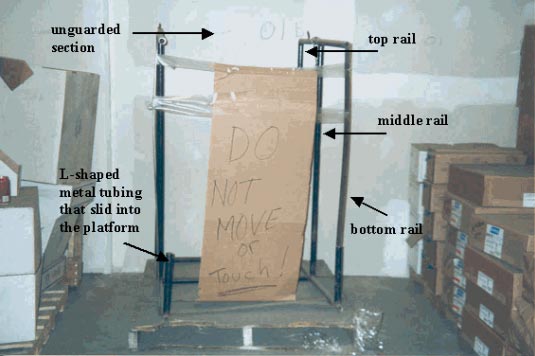
Figure 4 – Guardrail system unattached from the pallet and positioned on one end.
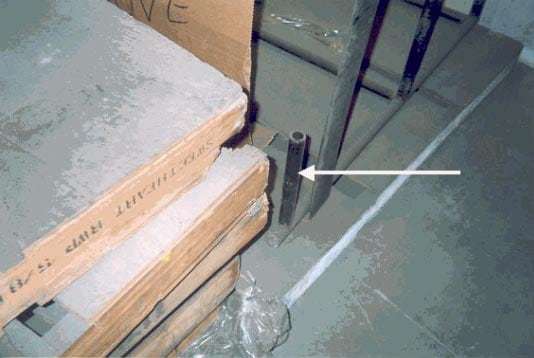
Figure 5 – L-shaped metal tubing that slid into the same opening in the pallet as the order picker tines connecting the guardrail to the pallet.
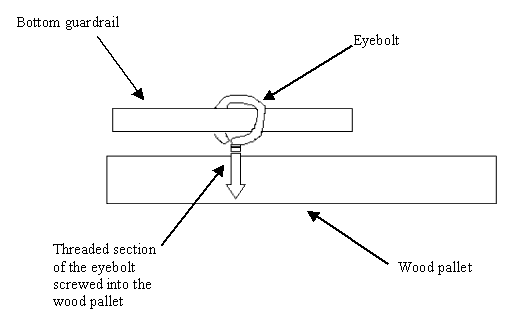
Figure 6 – Diagram of how the eyebolt was used to fasten the guardrail system to the pallet.
The threaded section of the eyebolt was screwed into the wood deck of the pallet. The eye section of the eyebolt had been bent open and the bottom rail of the guardrail system, which is a flat thin piece of metal four inches wide, was slid into the eye. The eye section of the eyebolt was then re-bent closed.
SUMMARY OF OSHA’S DRAFT PROPOSED |
|
Core elements
Basic obligations
Employee participation
Identify and assess hazards to which employees are exposed
Investigate safety and health events in the workplace
|
Safety and health program record keeping
Hazard prevention and control
Information and training
Program evaluation and maintenance
Multi-employer workplaces
|
Date issued November 23, 1998. Full text available on https://www.osha.gov/dsg/topics/safetyhealth/nshp.htmlexternal icon. (Link updated 3/20/2013)
To contact Massachusetts State FACE program personnel regarding State-based FACE reports, please use information listed on the Contact Sheet on the NIOSH FACE web site Please contact In-house FACE program personnel regarding In-house FACE reports and to gain assistance when State-FACE program personnel cannot be reached.