A Low Bed Trailer Operator was Crushed During a Surface Compactor Tipover -- Alaska
FACE 97-AK-019
SUMMARY
On June 9, 1997, a low bed trailer operator (the victim) was crushed when a surface compactor he was operating tipped over while being unloaded from a low bed trailer. As the victim backed the compactor down one of the trailer ramps, the machine became unbalanced and began to slide and tip sideways off the trailer bed and ramp. The victim jumped from the operator’s position but was crushed by the rollover protection structure (ROPS). Emergency medical services were notified immediately after the incident. The victim was extracted and transported to the nearest medical center. He died from his injuries later that evening.
Based on the findings of the investigation, to prevent similar occurrences, employers should:
- reinforce safe operation techniques including the function of the rollover protection structure;
- ensure ramps used for loading and unloading equipment are an adequate width and trailers are appropriately positioned and level to minimize risk of rollover (tipover).
INTRODUCTION
At approximately 2:10 PM on June 9, 1997, a 52 year old low bed trailer operator (the victim) was crushed when a surface compactor he was operating tipped over while being unloaded from a tilt bed trailer. On June 10, 1997, Alaska Division of Public Health, Section of Epidemiology contacted the Alaska Department of Labor (AK-DOL). An investigation involving an Injury Prevention Specialist for the Alaska Department of Health and Social Services, Section of Epidemiology ensued on June 13, 1997. The incident was reviewed with AK-DOL and local police department officials. Police and Medical Examiner reports, as well as AK-DOL reports, were requested.
The paving operation in this incident was privately owned and employed 65 employees. The victim was the sole low bed trailer or “low boy” operator. The company had been in business since 1975 but was under new ownership since 1994. The victim had worked for both the current and previous owners. At the time of the incident, the victim was delivering a vibrating surface compactor to a residential work site.
The company had a current safety program which included a written safety policy and daily tailgate meetings. Operation manuals for equipment used by employees were available. This was the first fatality experienced by this company.
INVESTIGATION
The company provided both commercial and residential paving and road work services. The incident occurred at a residential site. Heavy equipment used by the company was normally transported on a low bed (low boy) trailer used exclusively for the transportation of heavy equipment. The victim was employed as the sole low boy operator; his responsibilities included loading and unloading of equipment as well as its transportation to and from work sites.
The terrain at the incident site was relatively level and had been graded in preparation for paving. The weather was cloudy without any noticeable precipitation. The trailer was a Dynaweld low bed trailer with adjustable ramps. In addition, the front of the trailer bed can be lifted to provide an extended, flat loading surface for equipment with minimal ground clearance (e.g., scrapers and pavers). The trailer length was approximately 25 feet. Each ramp was 22 inches wide and could be positioned to provide a minimum gap of approximately 34 inches between the ramps (Figure 1). Ramp height for the bed when tilted was 18 inches. The surfaces of the trailer bed and ramps were dry and clear of any excess rock and soil.
The surface compactor involved in this incident was an Ingersoll-Rand vibrating compactor, model DD-22. The compactor was equipped with a manufacturer-installed ROPS. Total weight of the compactor with ROPS was 8630 pounds. The height from the ground to the top of the ROPS was 97 inches (Figure 2a). The drum width was 39 inches (Figure 2b).
On the day of the incident, the compactor along with a paver were transported simultaneously to the work site via the low bed trailer. The victim, working alone as he normally did during the performance of his assignments, intended to unloaded the paver first, followed by the compactor. Having successfully unloaded the paver, the victim had begun to back the compactor down the left ramp (Figure 1). The rear drum proceeded down the ramp approximately 12 inches when the compactor became unstable and began to slide off the left edge of the ramp and tip. According to a neighborhood resident (the witness), the victim jumped from the compactor and trailer. After taking several steps away from the trailer , the victim turned to face the trailer and was struck by the ROPS as the compactor settled onto its side (Figure 3). The victim remained pinned between the ground and the ROPS. The witness immediately called 911. At 2:14 PM fire department and ambulance personnel arrived on the scene and began to extricate the victim. The victim was transported by ambulance to the nearest medical center and was listed in critical condition. The victim died later that evening from his injuries.
CAUSE OF DEATH
The death certificate listed the immediate cause of death as crushed head.
RECOMMENDATIONS/DISCUSSION
Recommendation #1: Employers should reinforce safe operation techniques including the function of the rollover protection structure.
Discussion: The General Duty Clause of the Occupational Safety and Health Act of 1970 states employees must comply with all occupational safety and health standards, rules, regulations and orders that apply to their own actions and conduct on the job. Although the victim was an experienced low bed operator and reportedly familiar with the safe operation of the compactor, he did not observe safety procedures which would likely have prevented this fatality. The surface compactor in this incident was well-marked with safety labels stating the hazards of rollover, the need to “BUCKLE UP” and stay belted while operating the machine, and “DO NOT JUMP IF THE MACHINE TIPS.” Employers may consider implementing a spot inspection program to ensure compliance with safety requirements and positive incentives for safe work practices by employees.
Recommendation #2: Employers should ensure ramps used for loading and unloading equipment are an adequate width and trailers are appropriately positioned and level to minimize risk of rollover (tipover).
Discussion: Although the trailer was equipped with horizontally adjustable ramps to accommodate various axle lengths, the maximum adjustment to narrow the gap between the ramps could not have provided adequate support to safely load and unload the compactor. However, the procedure used by the victim required him to maintain nearly a 9-inch overlap of the drum on each side of the single ramp. The drum width in this incident was 17.4 inches or 44% wider than the width of the ramp, increasing the risk of slippage off either side of the ramp as the compactor proceeded down the ramp. A trailer with adequate ramp surface should have been used for the transportation of this machine. In addition, the use of a spotter may have also provided additional assurance that positioning on the trailer ramps was maintained during loading and unloading of machinery.

Figure 1. Aerial view of tilted trailer and ramps.
![]() |
![]() |
Figure 2a. Side view of compactor |
Figure 2b. End view of compactor |
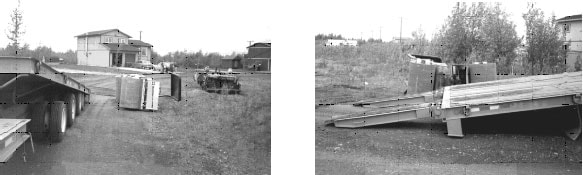
Figure 3. Position of compactor after tipover.
To contact Alaska State FACE program personnel regarding State-based FACE reports, please use information listed on the Contact Sheet on the NIOSH FACE web site Please contact In-house FACE program personnel regarding In-house FACE reports and to gain assistance when State-FACE program personnel cannot be reached.