Stone Worker Crushed To Death Under Toppled Granite Slabs
FACE Investigation #96-NJ-080-01
DATE: March 21, 1997
SUMMARY
On October 12, 1996, a 48-year-old worker at a stone fabrication shop was killed after being crushed by falling 700 pound slabs of granite. The incident occurred as the victim and a co-worker were using a forklift truck to move a granite slab to a metal A-frame used to store the slabs on edge. As the slab was lowered into position, the forklift pushed against three other granite slabs stored on a second A-frame, causing them to tip over and fall towards the victim. The victim, who was standing between the metal frames to release the slab from the forklift, was crushed between the falling slabs and the slabs stored on the A-frame in front of him. NJ FACE investigators concluded that, to prevent similar incidents in the future, these safety guidelines should be followed:
- The employer should examine alternate methods means of moving, storing or securing the stone slabs.
- Employers should conduct a job hazard analysis of all work activities with the participation of the workers.
- Employers should be aware of educational and training resources for health and safety information.
INTRODUCTION
On October 15, 1996, NJ FACE personnel received a newspaper article describing a work-related fatality involving a forklift truck that occurred on October 12, 1996. A FACE investigator contacted the company and arranged to do a site visit which was conducted on October 31, 1996. During the visit, FACE investigators interviewed the employer and photographed the incident scene and forklift. Additional information on the incident was gathered from the OSHA compliance officer, the police report, and the medical examiner’s report.
The employer was a small granite and marble fabricating shop that manufactured polished stone countertops and tables. The company also sold stone tiling and home decorations. At the time of the incident, the company had been in business for more than seven years and employed 13 workers. Although the company did not have a formal written safety program, they did have written procedures for wearing hardhats, eye protection, and hearing protection. Safety signs were posted throughout the shop, often in two languages for the benefit of the Polish speaking workers. The victim was a 48-year-old stone worker who had been employed by the company for six years. Formerly a farmer in Poland, the victim worked in construction for five years before being hired by the stone company. The owner of the company described him as an experienced worker who could run the shop when the foreman was absent.
INVESTIGATION
The incident occurred at the fabrication shop which was located in an urban industrial area. The company was housed in a large building containing the company showroom, stone shop, and storage warehouse. Materials were also stored outdoors in a fenced-in storage area. Specializing in manufacturing stone kitchen countertops and tables, the company imported large slabs of granite and marble from quarries in Europe. The slabs arrived finished (polished) on one side and varied in size, with the slabs involved in the incident measuring 9 feet long by 5½ feet wide by 1¼ inches thick. Most of the slabs were kept in the company warehouse, which provided a comfortable environment for customers to examine the stone. The slabs were stored by standing them on edge against an A-frame, a heavy gauge steel frame that supported the slabs in a manner similar to leaning books against a bookend (see Figure 1). Slabs were placed on both sides of the A-frame to prevent the free standing frames from moving under the weight of the stone. A forklift moved the slab to the cutting room where it was cut and finished to the customer’s specifications.
The incident occurred on a clear Saturday afternoon while the victim and a co-worker were moving stone slabs into the warehouse from the outdoor storage area. The victim acted as a spotter while the co-worker operated a sit-down riding forklift with a lifting capacity of 8,250 pounds. Because of the weight and relatively fragile nature of the stone, moving the slabs required a special lifting device called a jib-boom. This was a heavy-duty, extendable steel boom mounted horizontally on the forks of the lift. Hanging from the end of the boom was a scissor gripping device that firmly held the slab between two large rubber pads. To move a slab, the forklift operator raised the forks until the jib-boom and scissor gripper were over the slabs. The spotter pulled a slab away from the A-frame and positioned the scissor gripper over the center of the slab, allowing the gripper pads to close on the edge of the stone. After testing that the gripper was positioned properly, the spotter stood by the side of the slab to guide it as the forklift raised it off the A-frame and moved it across the floor.
At about 1:00 p.m., the victim and the forklift operator were moving a granite slab into the warehouse. The slabs were sorted by color on A-frames arranged into two rows, with about three feet of space between each A-frame. Because of the length of the forklift and attached boom, the forklift operator had to approach the row of A-frames at an angle. This brought the forklift mast near the A-frame where the slab was to be placed. While the forklift operator maneuvered the slab into position, the victim stepped between the two A-frames to guide the slab and release the gripper mechanism. When the forklift operator moved the lift forward, the mast of the lift pushed against the slabs on the A-frame, toppling three 700 pound slabs toward the victim. The victim apparently saw this and tried to duck out of the way, but was caught between the falling slabs and the neighboring A-frame behind him. Other workers immediately went to the victim and lifted the slabs off of him, but it was apparent that he had died instantly. The police and EMS arrived and transported him to the county medical examiner’s office where he was pronounced dead. Following the incident, employees received counseling from an emergency crisis counseling service recommended by the police.
CAUSE OF DEATH
The county medical examiner attributed the cause of death to “crushing head injuries due to an accident.”
RECOMMENDATIONS/DISCUSSIONS
Recommendation #1: The employer should examine alternate methods of moving, storing or securing the stone slabs.
Discussion: In this incident, the employee was crushed when the forklift inadvertantly pushed the stone slabs off the neighboring A-frame. Placing the slabs on the A-frames is a common industry practice for storing this type of material, allowing easy access to the stone and efficient use of space. However, using the jib-boom to move the stone required the worker to stand between the A-frames to attach and remove the gripper mechanism, exposing the worker to the falling stone slabs. To prevent future incidents, the FACE program recommends that the employer explore alternate methods of moving, storing, and securing the slabs to prevent their falling over. The following are possible methods:
Moving: The use of the jib-boom required the forklift to be positioned near the A-frames to reach the stone slabs. This became a problem due to the limited maneuvering room in the warehouse. If space permits, the employer should try to reposition the A-frames to allow the forklift enough room to approach the slabs directly from the side. An alternative method would be to use an overhead crane to move the slabs onto a dolly, eliminating the need for a forklift in this area.
Storage: A storage system should securely hold the stone slabs to prevent them from falling over while offering easy access to each slab. One possibility is to replace the A-frames with a W-frame that would catch a falling slab within the framework. (see figure 2). Another method is to design a racking system where each slab is held in an individual slot (see Figure 3). These types of frames must be strong enough to withstand the weight of the falling slabs, and may present a pinch-point hazard if an employee has his hand caught between the frame and the stone.
Securing: After the incident, the employer purchased a number of heavy nylon straps to wrap and secure the stone slabs to the A-frames.
Recommendation #2: Employers should conduct a job hazard analysis of all work activities with the participation of the workers.
Discussion: The employer was very proactive in seeking solutions to various safety hazards in the shop, such as providing safety equipment and posting bi-lingual safety notices. To assist in this process, FACE recommends that the employer conduct a job hazard analysis of all work areas and job tasks with their employees. A job hazard analysis should begin by reviewing the work activities that the employee is responsible for and the equipment needed. Each task is further examined for fall, electrical, chemical, or any other hazard the worker may encounter. The results of the analysis can be used to design or modify a written safety program. Further information is available in the attached OSHA puplication, Job Hazard Analysis. Employers may want to consider hiring a qualified safety consultant to conduct the initial analysis.
Recommendation #3: Employers should be aware of educational and training resources for health and safety information.
Discussion: It is important that employers obtain current information on OSHA regulations and methods of ensuring safe working conditions. Because obtaining this type of information is often difficult for a small business, the following sources may be helpful:
U.S. Department of Labor, OSHA: On request, the federal Occupational Safety and Health Administration (OSHA) will provide information on safety standards and requirements. OSHA has several offices in New Jersey that cover the following areas:
Hunterdon, Union, Middlesex, Warren and Somerset Counties………………..(908) 750-3270
Essex, Sussex, Hudson and Morris Counties………………………………………….(201) 263-1003
Bergen and Passaic Counties………………………………………………………………..(201) 288-1700
Atlantic, Gloucester, Burlington, Mercer, Camden, Monmouth,
Cape May, Ocean, Cumberland and Salem Counties……………………………….(609) 757-5181
NJDOL OSHA Consultative Services: The New Jersey Department of Labor OSHA Consultative Service will provide free consultation to business owners on improving health and safety in the workplace and complying with OSHA standards. Their telephone number is (609) 292-3922.
New Jersey State Safety Council: The NJ Safety Council provides a variety of courses on work-related safety. There is a charge for the seminars. Their address and telephone number is 6 Commerce Drive, Cranford, New Jersey 07016, telephone (908) 272-7712
Other Sources: Trade organizations, equipment manufacturers, and trade unions are good sources of information on suppliers of safety equipment and training.
REFERENCES
Code of Federal Regulations 29 CFR 1910. US Government Printing Office, Office of the Federal Register, Washington DC
ATTACHMENTS
Job Hazard Analysis. OSHA 3071, US Department of Labor, Occupational Safety and Health Administration, Washington DC. 1988.
FACE # 96-NJ-080-01
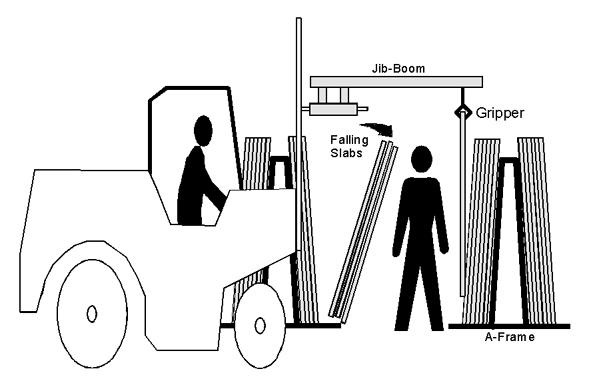
Figure 1. Worker crushed by stone stabs falling off A-Frame
*Not To Scale*
P. Bost
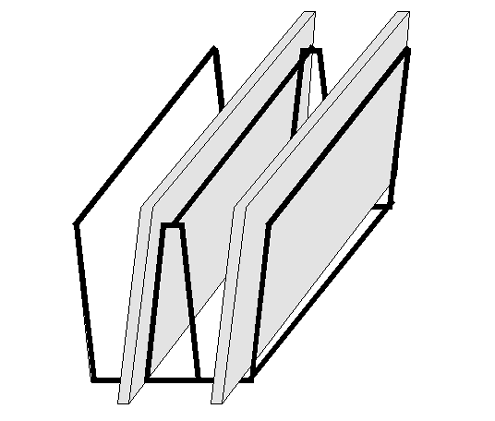
Figure2. W-Frame
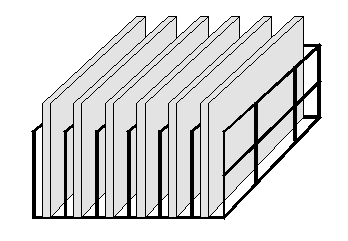
Figure 3. Slab Rack
To contact New Jersey State FACE program personnel regarding State-based FACE reports, please use information listed on the Contact Sheet on the NIOSH FACE web site. Please contact In-house FACE program personnel regarding In-house FACE reports and to gain assistance when State-FACE program personnel cannot be reached.