Press Operator Dies After Forklift Rams Scrap Bin-- North Carolina
FACE 9604
SUMMARY
A 39-year-old female punch press operator (the victim) working in a computer components manufacturing plant died as a result of injuries she sustained after a forklift operated by a co-worker ran into a scrap bin pinning her against the frame of the press. The victim had been working at a four-station punch press located adjacent to a designated forklift aisle. A co-worker was backing a forklift along the aisle in preparation for retrieving material from a pallet rack. As the operator positioned the forklift to access the rack, it struck a scrap parts bin. The scrap bin was propelled into the victim’s punch press, rebounded, struck the forklift again, and was propelled once more toward the press where it struck and pinned the victim against the press frame as she tried to escape. Co-workers notified management and 911 was contacted for assistance. EMS responded within about 5 minutes and the victim was transported to a local emergency department where she was pronounced dead.
NIOSH investigators concluded to prevent similar occurrences, employers should:
- ensure that work areas in manufacturing plants are isolated from designated vehicle travel ways by the installation of physical barriers
- ensure that forklifts are operated at safe speeds, in the forward direction when visibility permits.
INTRODUCTION
On October 19, 1995, a 39-year-old female punch press operator (the victim) died after being struck and crushed by a large metal scrap bin which had been inadvertently set in motion by a forklift. On October 24, 1995, officials of the North Carolina Occupational Safety and Health Administration (NCOSHA) notified the Division of Safety Research (DSR) of the occurrence, and requested technical assistance. On December 12, 1995, a DSR safety engineer reviewed the NCOSHA case file with the assigned compliance officer. On December 13, 1995, the safety engineer visited the incident site and met with the employer’s human resources manager to discuss the case.
The employer in this incident is a manufacturer of chassis and cabinet components for personal computers. About 725 workers are employed at the incident site which started operation in August 1994. The plant’s human resources manager is responsible for safety management. The company has a written safety program. Forklift operators at this facility are provided a 3-day training course taught by a local community college which includes formal classroom work as well as hands-on operation in non-production settings while under instructor observation. Upon completion of the course, the operators are certified by the employer to operate forklifts and are provided an annual 1-day refresher course thereafter. The operator in the incident had successfully completed the course on August 5, 1995. The victim had been employed for 9 months as a punch press operator. This was the first fatality experienced by the employer.
INVESTIGATION
The victim’s work station was a four-station punch press which produced steel chassis components for personal computers. The press was located in line with other presses adjacent to and parallel to the east wall of the plant building (see Figure). A pallet rack system was mounted against the building wall and between the pallet rack and the press was a 7-foot 10-inch wide aisle, designated for forklift travel.
The propane powered forklift involved in the incident was approximately 13 feet long, 4 foot 8 inches wide, weighed just over 15,000 pounds and was capable of traveling at a maximum speed of 11.5 miles per hour. Brakes were mounted on the drive wheels and were hydraulically actuated.
On the day of the incident, the victim, along with other workers, had begun the shift at the normal 9:30 p.m. start time. Work had proceeded normally until just before 11:30 p.m., at which time a forklift en route to the pallet rack had rounded the corner of the aisle. The forklift was observed by a co-worker to be traveling in reverse at a “high rate of speed” as it approached the victim’s work area. The forklift struck a metal scrap bin, approximately 3 foot by 5 foot by 32 feet high, propelling it toward the punch press. The scrap bin hit the press and rebounded toward the forklift where it was hit once more and shoved against the southeast corner of the press, striking and crushing the victim against the press. Co-workers immediately notified 911. Local police and EMS personnel responded within minutes. Resuscitative efforts were begun and continued during transport to a local hospital where she was pronounced dead.
Immediately following the incident, the operator told a responding policemen that the controls, throttle and brake were malfunctioning; however, subsequent tests and examinations performed by the employer’s maintenance contractor failed to detect any defects in the machine and the machine was returned to service. Also, immediately after the incident, alternating skid marks were observed on the smoothly finished concrete floor. The alternating orientation of the marks on the floor, suggests that they were made by the drive wheels spinning during shifting from reverse to forward.
CAUSE OF DEATH
The report of autopsy listed the cause of death as multiple crush injuries.
RECOMMENDATIONS/DISCUSSION
Recommendation #1: Employers should ensure that work areas in manufacturing plants are isolated from designated vehicle travel ways by the installation of physical barriers.
Discussion: The employer had designated a travel way for plant vehicles by posting yellow lines on the plant floor. This type of posting allows easy access to all areas of the plant where forklifts may be needed for heavy lifting. The punch presses used at the plant produce variously shaped parts, depending on the press set-up configuration. When changing press configuration, it is necessary to provide forklift access to the press so that they can be used to change-out move heavy press parts during the set-up. For this reason, physical barriers had been viewed as being impractical. However, it might be possible to install removable barriers which would allow access to the presses for die change-out.
Recommendation #2: Employers should ensure that forklifts are operated at safe speeds, in the forward direction when visibility permits.
Discussion: The employer in this incident had an extensive written policy and licensing procedure for forklift operators. This included 24 hours of training and hands-on practice under instructor observation in non-production settings. Licenses are only issued after the employee has successfully passed a test on procedures and demonstrated competence to the observing trainer. After initial training, operators must attend annual 1-day refresher training to remain licensed. The operator of the forklift in the incident had successfully completed the training in August 1995. Although the employer had developed and implemented safe operating procedures including a provision addressing maximum operating speed, the procedures did not include a provision requiring the operator to face the direction of travel if possible. Since the forklift was being operated in reverse, the operator may not have been facing the direction of travel and may not have been aware of the proximity of the bin until the forklift struck it. It is not always desirable to operate a forklift in the forward direction because loads often block the operator’s view. However, in this instance the forklift was not loaded and if the operator had been facing the direction of travel, he may have been more aware of his location relative to the scrap bin and may have been able to avoid it. Operating in forward when traveling unloaded from place to place within the plant, or at least always facing the direction of travel, would ensure that operators are aware of their location with respect to other objects.
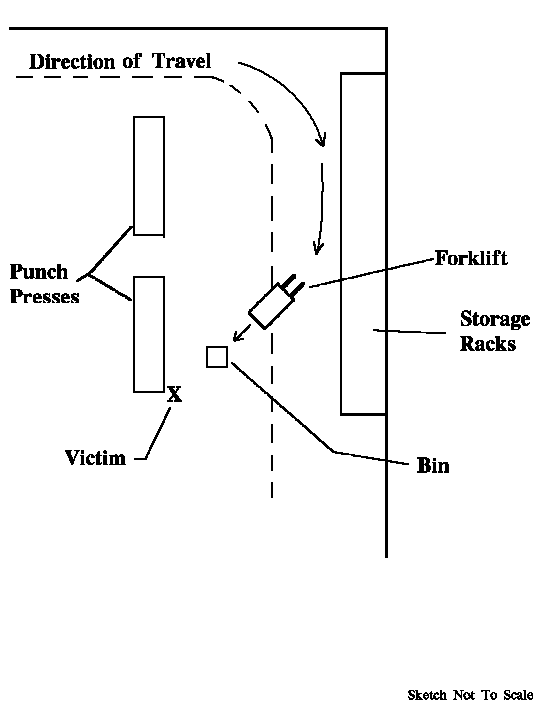
Figure.
Return to In-house FACE reports